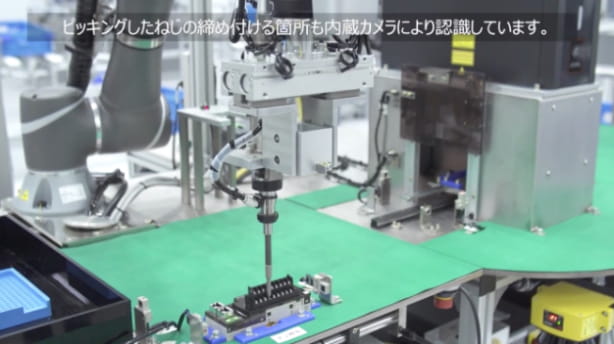
組立工数の削減のために
セル生産に導入した協調ロボット活用と工夫
導入事例:
旭光電機株式会社様
商品名:協調ロボット「TMシリーズ」
組立 省力化・自働化 情報化
2人持ちU字セルラインを1人持ちに変えた協調ロボット
-
1. 限られた生産リソースを最大限に活用、生産人員削減と生産性アップを達成
-
2. 『銘板視認』、『ハンドリング』、『ネジ締め』の複合動作を実現
-
3. 『横からのネジ締め』 ネジ締結時に発生していたチョコ停への対策
主に産業用機器に組み込まれて使用される少量多品種のユニット機器を生産されている旭光電機様です。
増えてきた生産量に対応するには、工場全体の生産リソースに限りがあるため、既存の生産ラインにかけてきた工数の見直しが必要になってきました。
今回生産品目のなかでは比較的生産量の多いドア制御コントローラの2人持ちU字生産ラインに着目し、作業者とともに働ける協調ロボットを導入されました。
元は2名で担当されていたU字ラインのなかで協調ロボットが担当したのは、ネジ組立と耐圧試験、機能検査試験の工程です。それまで人1名が作業していた部分を担いました。U字ライン内では、協調ロボットは機能検査試験のタクトに合わせてネジ締め作業と搬送作業を行い、残る1名の作業者はその他の工程を負担することで全体のタクトタイムが平滑になり生産効率が上がりました。
1台の協調ロボットで、『ワーク銘板の読み取り』、『ワークをつかんで各作業ポジションへ搬送』、『ネジをピックアップして複数個所締結』という作業を繰り返しています。複数の機能を果たすために配管やケーブルも増えたため、運用当初はたびたびトラブルにみまわれました。試行錯誤の末に、現在ではロボットアーム6軸の可動域を最大限に動かしながらも耐久性のある取り回しができるようになりました。
今回は、『横からのネジ締め』を採用されました。なぜ難しいとされる横からのネジ締めにチャレンジされたのか、また当初は頻発していたチョコ停をどうやって撲滅されていったのか、その取り組みについても披露いただけました。
プロジェクトリーダの横田課長は、「協調ロボットと旭光電機製のIoT監視機器を組み合わせたラインを、製造モニタリングのモデルケースとして運用していきたい。」と抱負を述べられました。
担当された山崎様からはロボット立ち上げでの利用者視点でのご意見をいただきました。また「今後ロボットを工程検討のリソースとして当たり前に活用できるようになりたい。」との期待を込められています。
旭光電機株式会社
自動ドア、鉄道、船舶などで培ってきたセンシング・コントロール・無線通信ネットワーク技術を核にして、常に独創的な開発テーマに取り組んでいます。これらの技術は幅広い分野に応用され、安全で快適な暮らしを支える役割を担っています。
旭光電機の生産・製造技術部門は充実した設備とこれまで培ってきた製造技術で、信頼できる高品質な製品をご提供できるように独自の生産管理システムと試験設備で万全の品質管理を行っています。工場構内にはモバイルロボットによる生産仕掛品の工程間自動搬送システムを導入しており、国内外からの見学者も増えています。