リスクアセスメントの手順
リスクアセスメント
機械を安全にするためには、機械の危険を分析・評価し、リスクを減らすことが必要です。そのためのリスクアセスメントとリスク低減の手順がISO規格で定められています。
機械に存在する危険源やリスクレベルは機械のライフサイクル(製造、改造、運搬や解体、廃棄となど)の各段階によって異なります。これらのライフサイクルすべてにおいて機械が安全であるように設計・製造される必要があります。ISO 12100は、リスクアセスメントを論理的に実行し、その後に続くリスク低減方策の選択へとつなげていくための原則を定めた規格です。
機械の安全化は5つの手順で実現することができます。一連のプロセスで検討した内容は文書化し、機械の安全設計の根拠を示すものとして保管しておく必要があります。
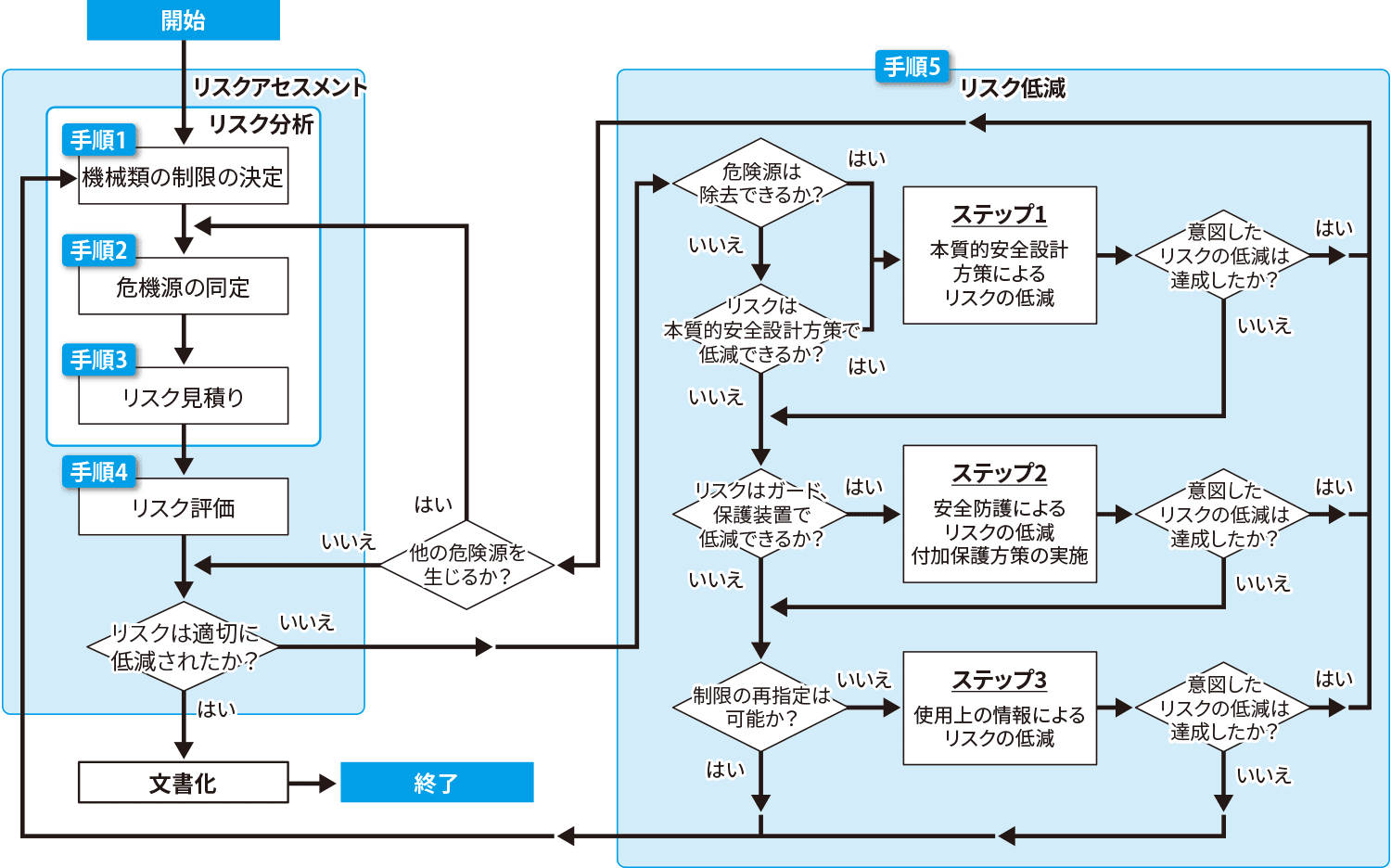
手順1 機械類の制限の決定
『機械類の制限の決定』とは、リスクアセスメントを実施する際に考慮すべき前提条件を決めることです。「使用上の制限」としては、以下のような内容を考慮する必要があります。
- ライフサイクルの各段階に対する要求事項
- 機械の意図する使い方と動作および合理的に予見可能な誤使用と誤動作
- オペレータの性別、年齢、使用する利き腕または身体能力の限界(視覚又は聴覚の減退、体型、体力など)などによる制限
- 予想される使用者の訓練、経験、能力の度合い など
この他にも、「空間上の制限」として機械の可動範囲や機械の保全に必要な空間、「時間上の制限」として機械の寿命や点検間隔、「その他の制限」として機械で加工する材料の特性や機械の稼働に必要な環境要件などについても考慮する必要があります。
手順2 危険源の同定
『危険源の同定』とは、機械に付随するすべての危険源、危険状態および危険事象を見つけだすことです。危険源の種類としては、以下のようなものが挙げられます。
- 機械的危険源
- 電気的危険源
- 熱的危険源
- 騒音による危険源
- 振動による危険源
- 材料及び物質による危険源
- 人間工学原則の無視による危険源
- 機械が使用される環境に関連する危険源
詳細については、代表的な危険源の例を参照ください。
手順3 リスク見積り
『リスク見積り』とは、機械の危険な状態および危険事象を確認後、リスク要素を決定し、「起こりうる危害のひどさ」と「危害の発生確率」から危険の推定を行うことです。恒久的な危険源のほかに予期せず顕在化する危険源も含む全ての危険源に対して可能な限り定量的にリスクを見積もります。
手順4 リスク評価
『リスク評価』とは、リスク見積りを行った後、そのリスクを評価し、リスク低減が必要か否かを決定することです。リスク低減が必要な場合、手順5で示す設計変更、安全防護措置などの安全対策を行います。
手順5 リスク低減
『リスク低減』とは、リスクに対して下記のような方策を適用することです。「ステップ1:本質的安全設計方策」「ステップ2:安全防護及び付加保護方策」「ステップ3:使用上の情報」の3つのステップを通して適切なリスク低減を達成する必要があります。
- できる限り危険源を除去または削減する
- 危険源への暴露の確率と危害の重大度を下げる
- 防護装置および安全装置を使用する
- 安全装置の性能と機能特性が機械とその使用に適切であることを判断する