コード検証機とは
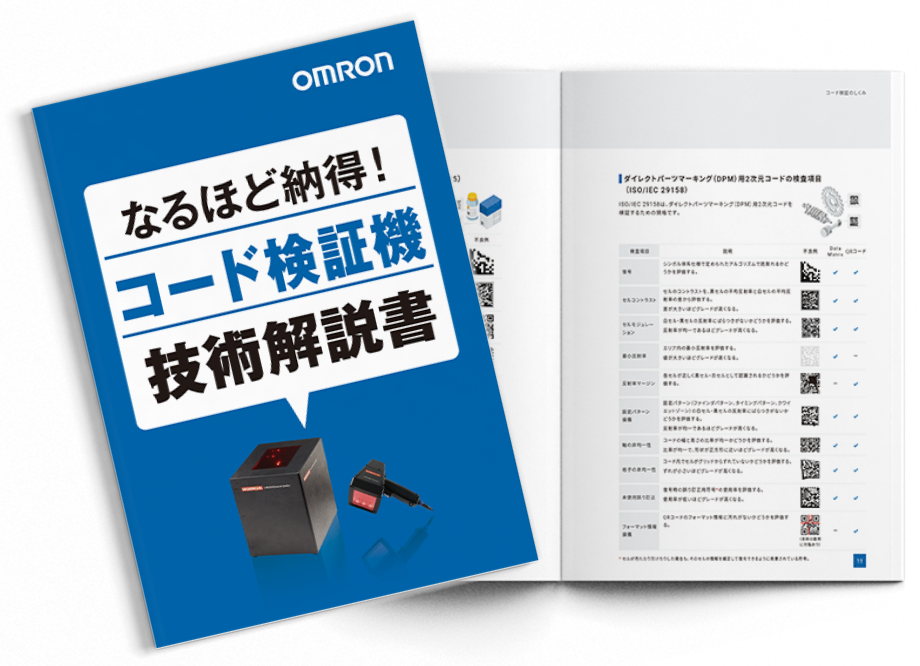
掲載内容
1. コード検証機とは
2. コード検証機のニーズが高まっている背景
- 使用範囲の拡大
- 法規制に伴うニーズの拡大
- コードの品質不良から発生するトラブル
- 例1: 返品トラブルによるペナルティ
- 例2: 生産ロス・ダウンタイムの発生-7
3. コード検証のしくみ
- 各コードの点数付けのルール
- 紙・ラベル用1次元コードの検査項目(ISO/IEC 15416)
- 紙・ラベル用2次元コードの検査項目(ISO/IEC 15415)
- ダイレクトパーツマーキング(DPM)用2次元コードの検査項目(ISO/IEC 29158)
- 検証できるコード不良例(オムロンのコード検証機LVSシリーズの場合)
- 検証の原理
- 光学的配置
- 検証機の精度基準
4. コード検証に関する規格
5. コード検証機の導入効果
- 例1: コード不良による返品発生時の原因分析
- 例2: 印字機導入時の条件出しと印字品質チェックを短時間で完了
- 例3: 印字機の予兆保全
- 例4: 納品時の品質検査レポート自動作成
6. オムロンのコード検証機のご紹介
- コード検証機 LVSシリーズ
- LVSシリーズの特長
1.コード検証機とは
コード検証機はコードの「採点機」
コード検証機は、印字されたコードが規格通りに印字されているかを評価する機械で、いわばコードの採点機のようなものです。
印字品質を複数の観点から検証し、検証結果を数値で管理します。
コードの印字品質は、「総合グレード」として0.0~4.0点の範囲で点数化され、4.0点に近いほど印字品質は良好といえます。
品質に問題なしと判断する基準の点数は、一般的に各業界団体で決められています。
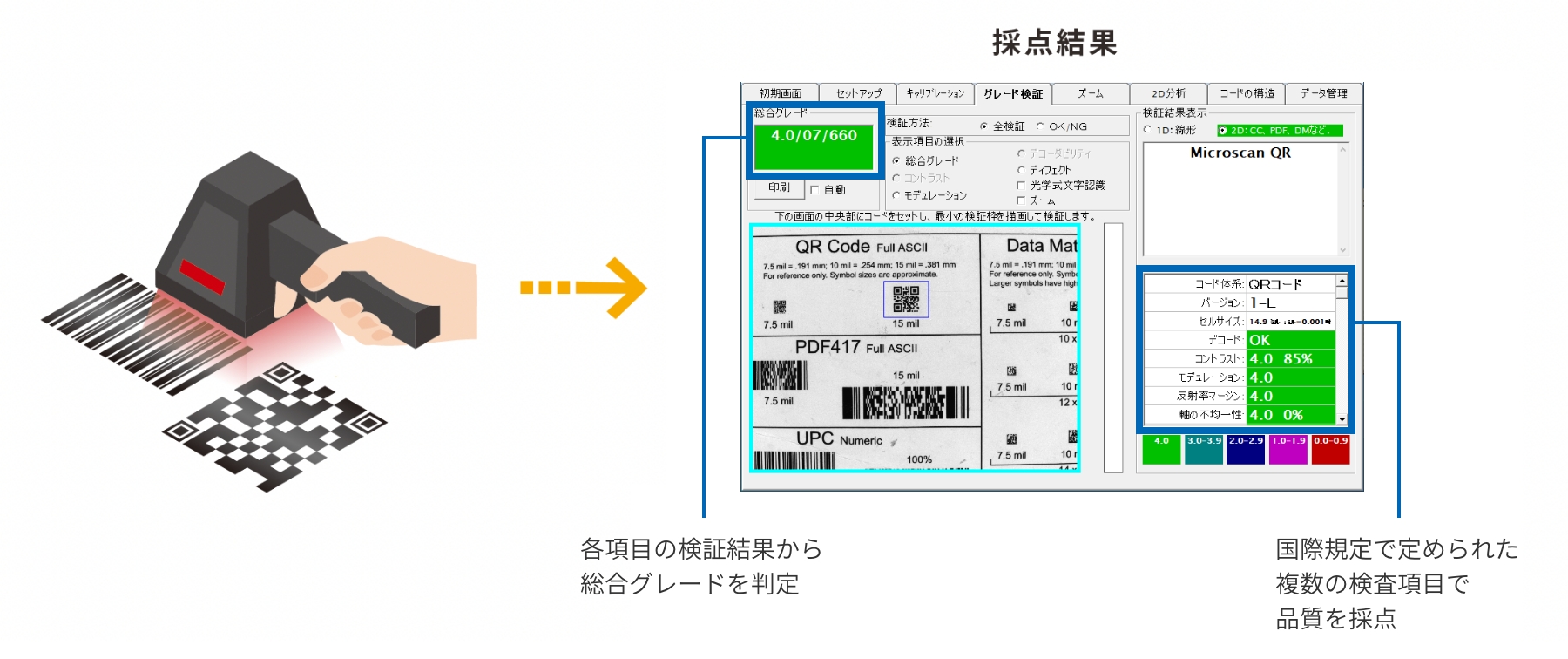
コード検証機でできること
国際規格に準拠した方法による、コード品質のチェック
検査項目や点数の算出方法は国際規格で定められており、読取り装置や読取り環境に左右されない客観的な品質チェックが可能です。
印字不具合の原因特定
複数ある検査項目の採点結果を個別に確認できるため、印字品質に問題ありと判断された場合の原因特定に役立ちます。
コードリーダのグレーディング機能と「検証」の違い
コードリーダの中には、読取ったコードの印字品質をグレーディングする機能を備えている製品があります。
しかし、検証のための規格に準拠していないコードリーダでは、設置距離や明るさの設定により結果が変わるため、相対的な評価しかできません。
また、コードリーダはあくまで読取りに特化した機器のため、コードに多少の汚れや欠けがあっても問題なく読取れてしまう場合があります。
これでは、装置や環境が変わったときに読取り不良が発生するリスクが残ってしまいます。
コード検証機を使用すれば、印字品質が正常かどうかを規格に基づいて客観的に判断でき、検証結果を品質確認のエビデンスとして利用できます。
2.コード検証機のニーズが高まっている背景
これまでもモノづくりのトレーサビリティにおいて重要な役割を果たしてきたコードですが、近年使用範囲が拡大し、印字内容の重要度が増していることから、読取り不良時のインパクトを軽減する対策が必要になっています。
対策として、さまざまな業種や生産品目において、コードを印字する工程での印字品質検査、部品受け入れ時の印字品質検査などが実施されており、これらの検査に求められる高い信頼性を備えた検査機器として、コード検証機への注目が高まっています。
使用範囲の拡大
コードを利用して製品の情報を管理したり、確認したりする範囲は、製造工程だけではなく流通・消費のフローにまで拡大しており、各工程で安定して読取り可能なコードの印字、印字品質の維持が求められています。
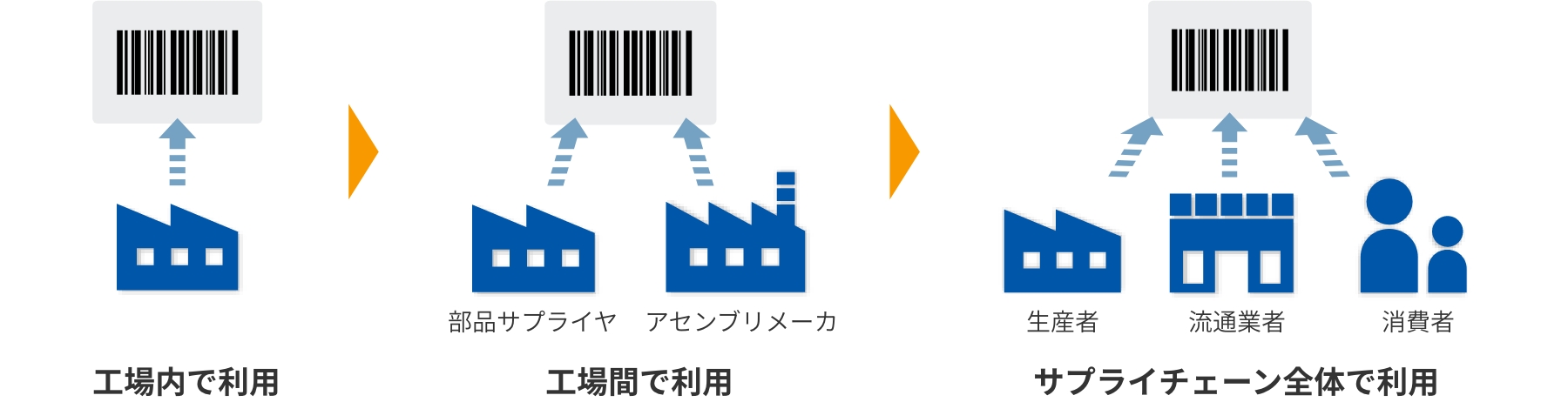
法規制に伴うニーズの拡大
製品リコールや医療事故の増加を受けて、国や業界ごとにトレーサビリティに関連する法規制や規格の整備が進んでいます。
医薬品・食品
- ・食品表示法改正によるアレルギー表示の義務化
- ・FDAや厚生労働省通達によるGS1コードの義務化
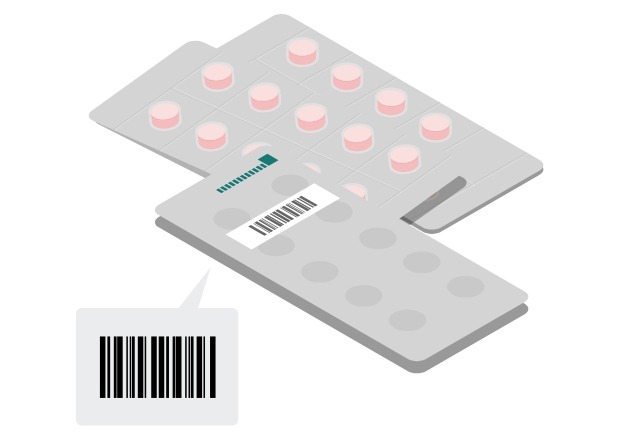
外装箱やパッケージだけではなく個装、シートにもコードを印字して、製品情報を厳格に管理。
自動車
- ・EVやADASの安全要求
- ・欧米自動車のIATF 16949規格制定
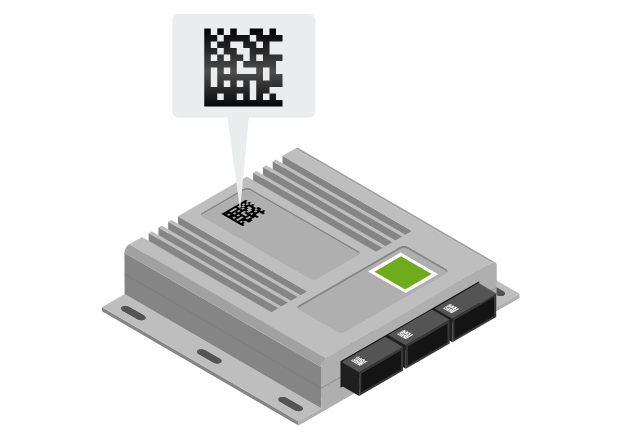
コードを印字して管理する部品の範囲をモータやインバータ、ECUなどのEV部品、ブレーキ部品にも拡大。
電子機器
- ・車載電装化のためのEIA規格への対応
- ・電子部品のサプライヤコントロールの範囲拡大
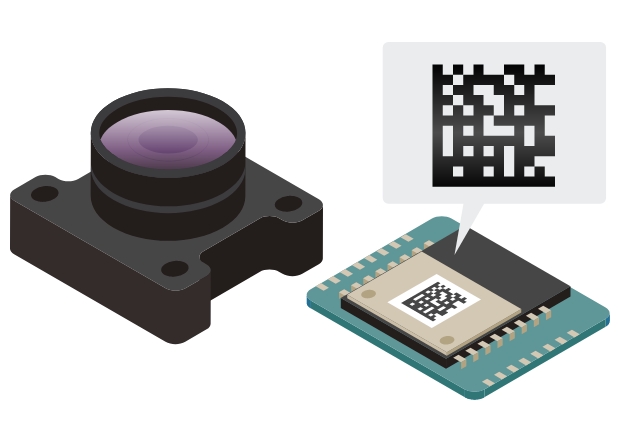
基板上のチップやセンサなどの各モジュールにもコードを印字して、個別トレースを可能に。
医療機器UDI規制への対応
医療の安全向上と効率化のため、コードによる医療機器と医療器具の個体管理、データベース登録の義務化が各国で進んでいます。
手術用のメス等の鋼製器具などに代表される、滅菌あるいは洗浄して繰り返し使用される医療器具には、ダイレクトマーキング(Direct Marking:直接印字)が必須とされており、米国FDAのUDI規則では2022年までにダイレクトマーキングが順次行われることが決まっています。
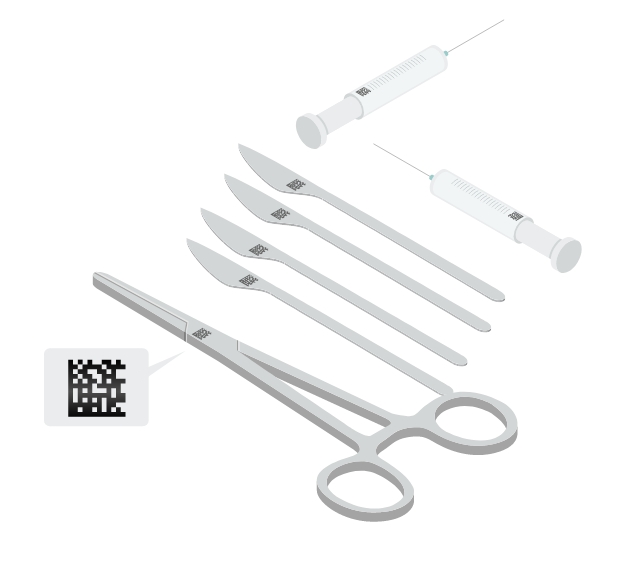
物流荷物搬送の自動化
流通網の広がりや、流通させる品物の増加と多様化に伴い、品物の仕分けや在庫管理、輸送の省人化と効率化のため、コードによる情報管理が不可欠になっています。
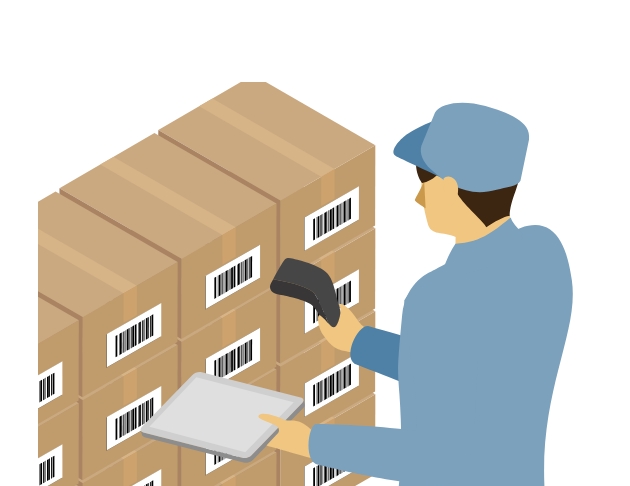
コードの品質不良から発生するトラブル
たとえば日常の場でも、小売店のレジでバーコードの読取り不良が発生すると、再読取りを繰り返したり、商品情報を確認して値段を手入力したりといった、ムダな作業が発生します。
同じことが工場内やサプライチェーンの中で発生すると生産効率の低下につながり、納入先から罰金やペナルティを課されたり、ブランドイメージが低下したりといった、さらに大きなリスクに発展するおそれがあります。
3.コード検証のしくみ
検証結果の正確性を担保するには、「適切な検証方法」と「検証精度の一貫性」の両方を確保することが重要です。
「適切な検証方法」についてはISO/IEC 15416、15415、29158などの印刷品質試験仕様で、「検証精度の一貫性」についてはISO/IEC 15426-1、15426-2などの検証機適合仕様で定められています。
コード検証機は、これらの国際規格の仕様に基づいて検証することにより、検証結果の正確性を担保しています。
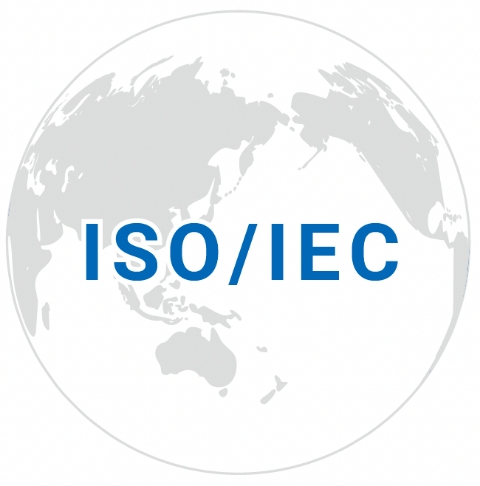
各コードの点数付けのルール
コードの採点結果は、印刷品質試験仕様に基づいて算出されます。
確認できる点数は、総合グレードと検査項目ごとの点数の2種類です。
総合グレード
コードの印字品質の検証結果を点数で表したものです。(0.0~4.0点)
品質に問題なしと判断する基準の点数は、一般的に各業界団体で決められています。
例として、下記に紙・ラベル用1次元コードの検査項目(ISO/IEC 15416)の総合グレードを説明します。
3.5~4.0 | 最も読取りの信頼性が高い。 以下のような場合にこのグレードを指定することが望ましい。 ・コードリーダが1回だけしか走査できない場合 ・固定式リーダで1本の走査線に限定されているような場合 |
---|---|
2.5~3.4 | 1本の走査線では再走査が必要になる場合がある。 |
1.5~2.4 | 2.5点以上のコードより、再走査が求められる回数は多くなる。 以下のような条件が望ましい。 ・複数の走査線を持つ読取り装置を使用・頻繁に再走査を試みる機能を持つシステム設計 |
0.5~1.4 | 読取り装置によっては、読取りに失敗する場合も成功する場合もある。 読取り失敗時のリスクに備え、別のデータ入力手段を備えておくなど回避策が必要。 読取りが可能かどうか、事前にテストしてから使用することが望ましい。 |
~0.4 | 読取りに失敗する可能性が高い。 |
検査項目ごとの点数
印刷品質試験仕様で定められた検査項目ごとの採点結果です。
検査項目は、コードの種類や印字方法によって異なります。
次に、代表的なコードの検査項目と、各検査項目でエラーになるコードの例を紹介します。
紙・ラベル用1次元コードの検査項目(ISO/IEC 15416)
ISO/IEC 15416は、紙・ラベル用1次元コードを検証するための規格です。(対応するJIS規格:JIS X 0520)
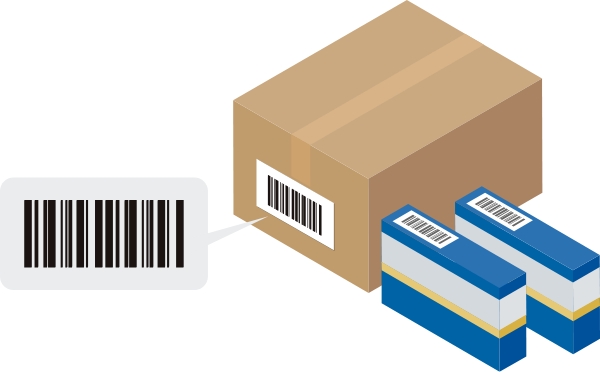
検査項目 | 説明 | 不良例 |
---|---|---|
復号 | シンボル体系仕様で定められたアルゴリズムで読取れるかどうかを評価する。 |
![]() |
シンボルコントラスト | バーとスペースのコントラストを、最大反射率と最小反射率の差から評価する。 |
![]() |
最小反射率 | バーの反射率がスペースの反射率に比べて十分小さいかを反射率波形から評価する。 |
![]() |
最小エッジコントラスト | バーとスペースの境界部のコントラストを反射率の差から評価する。 |
![]() |
モジュレーション | バーとスペースの反射率に、箇所ごとのばらつきがないかどうかを評価する。 |
![]() |
欠陥 | バーとスペースに欠けや汚れがないかどうかを評価する。 |
![]() |
復号容易度 | バーとスペースの幅がシンボル体系仕様の規定に一致しているかどうかを評価する。 |
![]() |
紙・ラベル用2次元コードの検査項目(ISO/IEC 15415)
ISO/IEC 15415は、紙・ラベル用2次元コードを検証するための規格です。(対応するJIS規格:JIS X 0526)
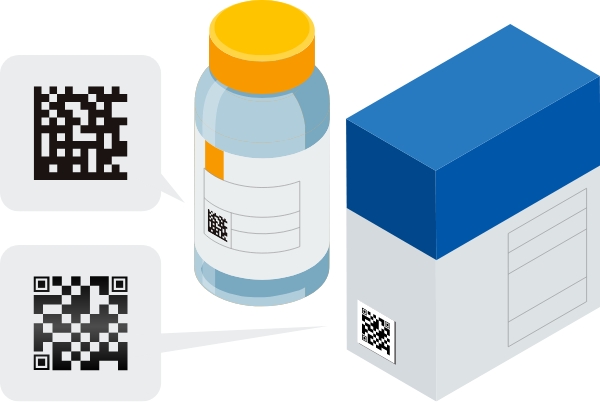
検査項目 | 説明 | 不良例 | Data Matrix |
QR コード |
---|---|---|---|---|
復号 | シンボル体系仕様で定められたアルゴリズムで読取れるかどうかを評価する。 |
![]() |
||
シンボルコントラスト | セルのコントラストを、最大反射率と最小反射率の差から評価する。 |
![]() |
||
モジュレーション | 白セル・黒セルの反射率にばらつきがないかどうかを評価する。 |
![]() |
||
反射率マージン | 各セルが正しく黒セル・白セルとして認識されるかどうかを評価する。 |
![]() |
||
固定パターン損傷 | 固定パターン(ファインダパターン、タイミングパターン、クワイエットゾーン)の白セル・黒セルの反射率にばらつきがないかどうかを評価する。 |
![]() |
||
軸の非均一性 | コードの幅と高さの比率が均一かどうかを評価する。 |
![]() |
||
格子の非均一性 | セルが、基準となるグリッドからずれていないかどうかを評価する。 |
![]() |
||
未使用誤り訂正 | 復号時の誤り訂正符号*の未使用率を評価する。 |
![]() |
||
フォーマット情報損傷 | QRコードのフォーマット情報に汚れがないかどうかを評価する。 |
![]() |
ー |
* セルが汚れたり欠けたりした場合も、そのセルの情報を補正して復元できるように用意されている符号。
ダイレクトパーツマーキング(DPM)用2次元コードの検査項目(ISO/IEC 29158)
ISO/IEC 29158は、ダイレクトパーツマーキング(DPM)用2次元コードを検証するための規格です。
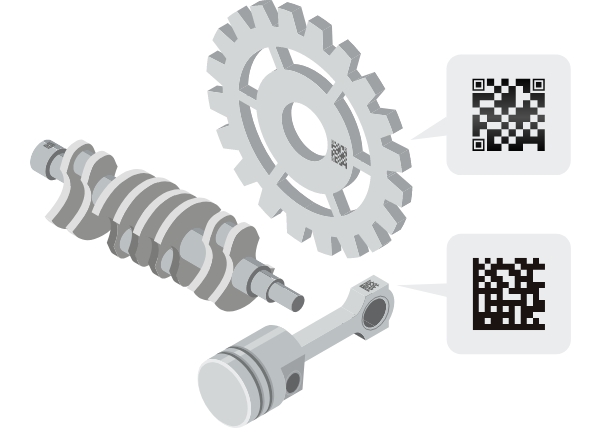
検査項目 | 説明 | 不良例 | Data Matrix |
QR コード |
---|---|---|---|---|
復号 | シンボル体系仕様で定められたアルゴリズムで読取れるかどうかを評価する。 |
![]() |
||
セルコントラスト | セルのコントラストを、黒セルの平均反射率と白セルの平均反射率の差から評価する。 |
![]() |
||
セルモジュレーション | 白セル・黒セルの反射率にばらつきがないかどうかを評価する。 |
![]() |
||
最小反射率 | 白セルの反射率が充分大きいかどうかを評価する。 |
![]() |
||
固定パターン損傷 | 固定パターン(ファインダパターン、タイミングパターン、クワイエットゾーン)の白セル・黒セルの反射率にばらつきがないかどうかを評価する。 |
![]() |
||
軸の非均一性 | コードの幅と高さの比率が均一かどうかを評価する。 |
![]() |
||
格子の非均一性 | コード内でセルがグリッドからずれていないかどうかを評価する。 |
![]() |
||
未使用誤り訂正 | 復号時の誤り訂正符号*の未使用率を評価する。 |
![]() |
||
フォーマット情報損傷 | QRコードのフォーマット情報に汚れがないかどうかを評価する。 |
![]() |
ー |
* セルが汚れたり欠けたりした場合も、そのセルの情報を補正して復元できるように用意されている符号。
検証の原理
検証の原理について、1次元コードを例に説明します。
ISO/IEC 15416では、1次元コードを10回掃引して反射率プロファイルを生成し、各掃引で得た反射率プロファイルをもとにして、すべての検査項目を測定します。
印字品質の総合グレードは、各掃引の最低総合グレードの平均から求めます。
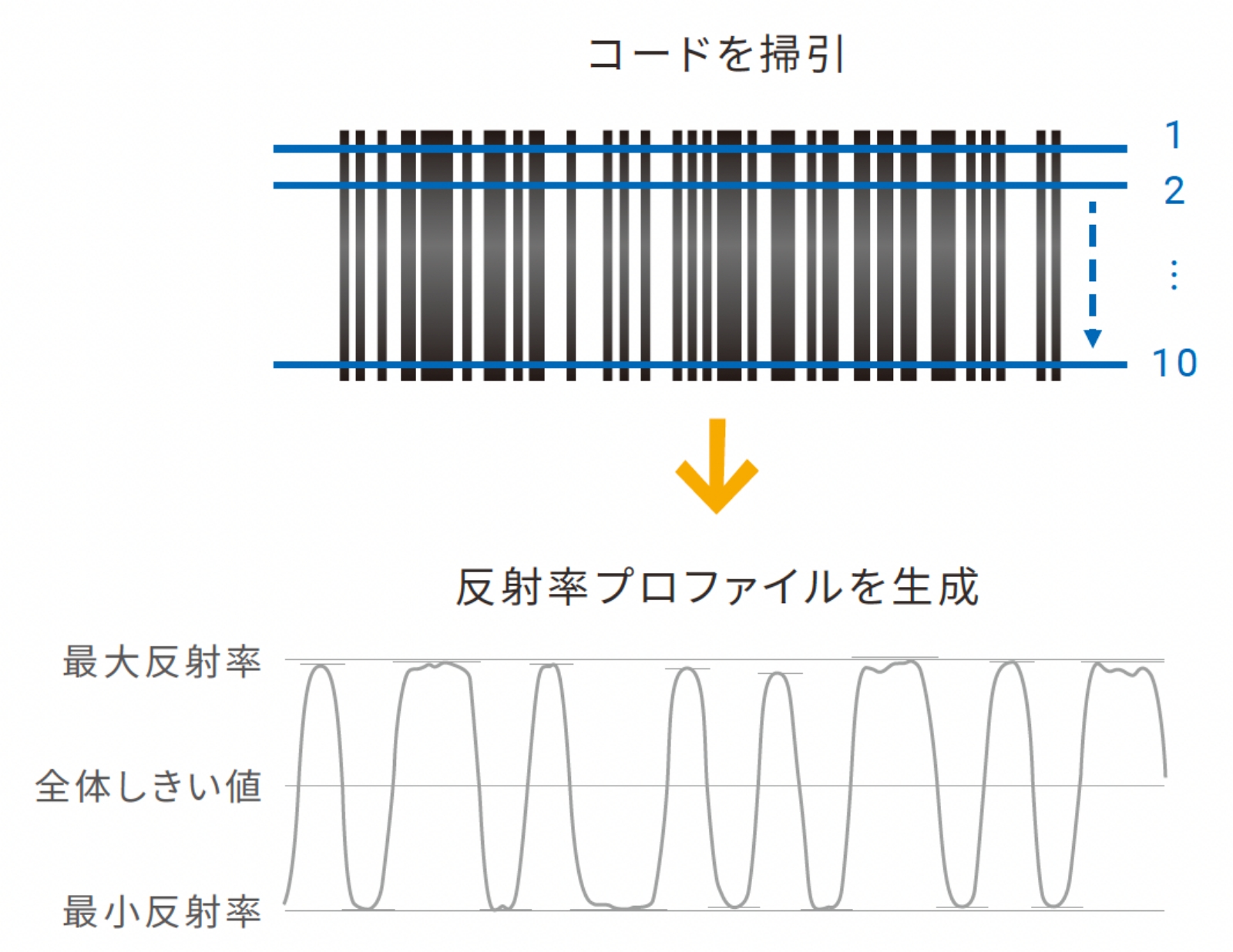
たとえばコード内に欠陥が存在した場合、10回の掃引のうち、その部分を掃引したときのみ反射率が変化します。反射率の変化が観測されると印字品質に問題ありと判断されるため、グレードは低くなります。
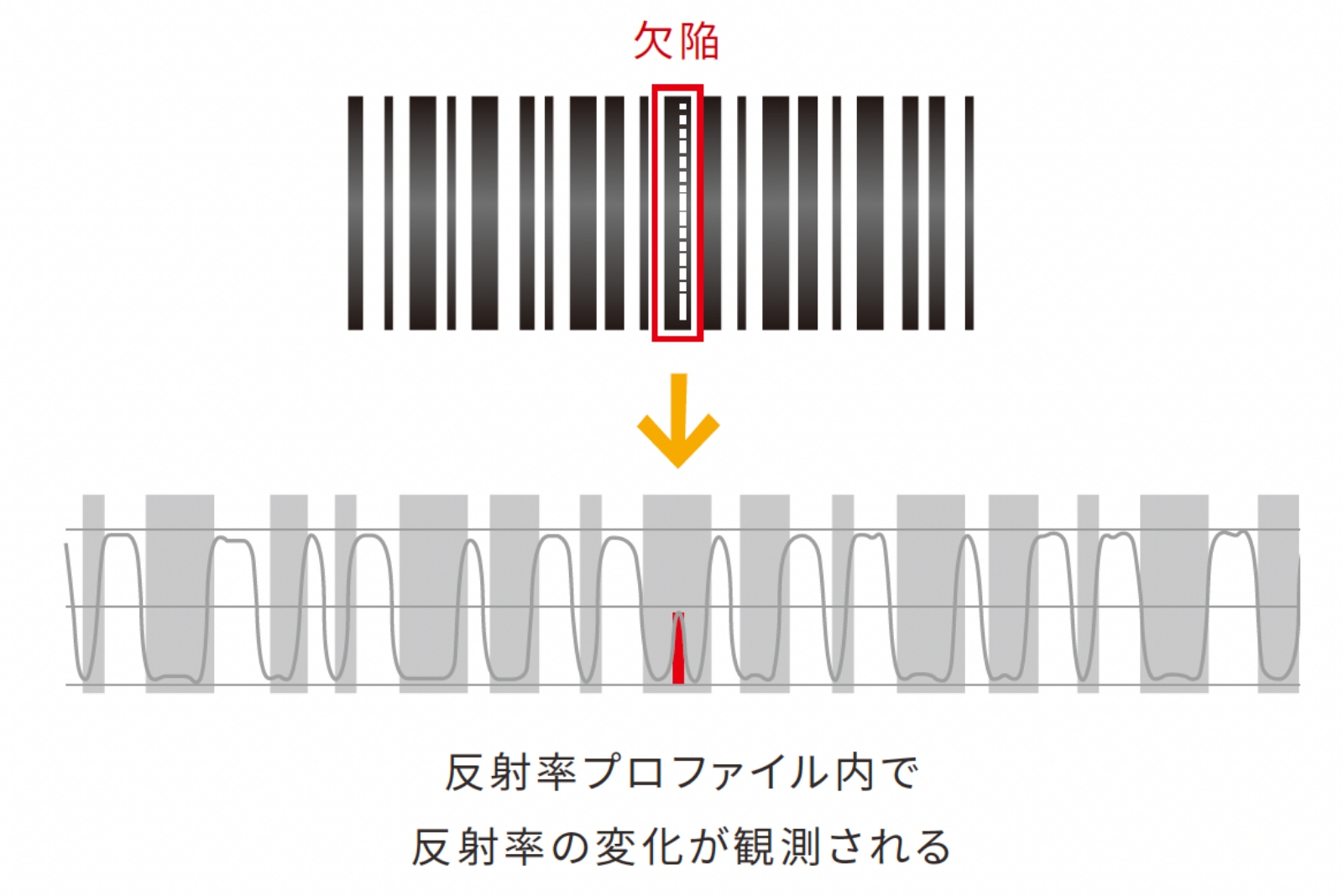
光学的配置
各規格では検証項目に加え、検証時の光源の角度を規定しています。コード検証機は、規定に沿った光源を備えるか、規定の光学的配置と性能面で相関が取れる光学的配置を使用する必要があります。
オムロンのコード検証機LVSシリーズは、規定の光学的配置と性能面で相関が取れる光学配置となっているので、問題なくご使用いただけます。
ISO/IEC 15416(紙・ラベル用1次元コード)
検証時、光源からの光は測定対象の面に対して45°で照射するように規定されています。
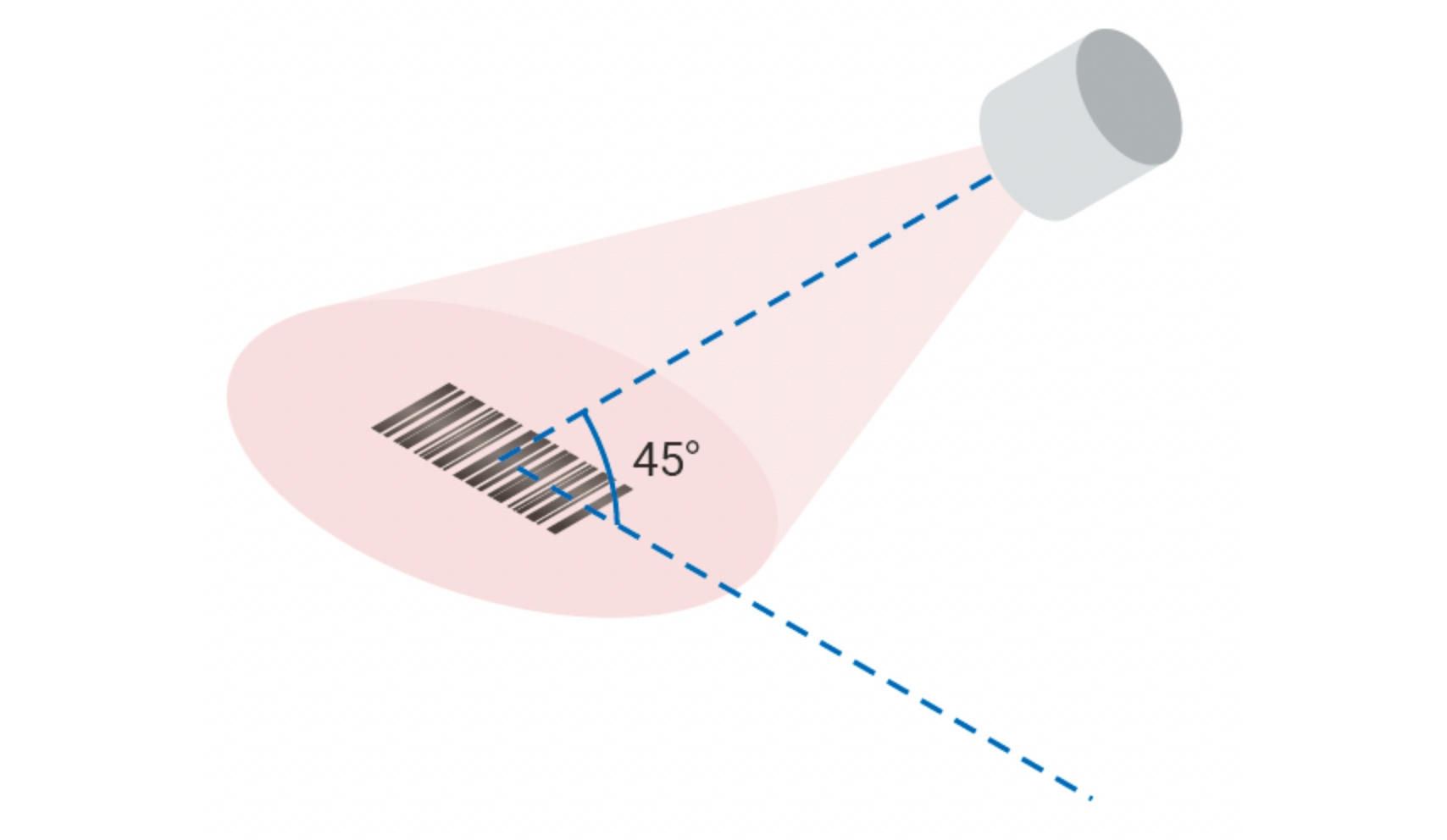
ISO/IEC 15415(紙・ラベル用2次元コード)
検証時、光源は4つ使用し、光は測定対象の面に対して45°で照射するように規定されています。
規定の光学的配置と性能面で相関がとれる光学的配置を使用することも可能ですが、その場合は総合シンボルグレードの報告書にその旨を明記する必要があります。
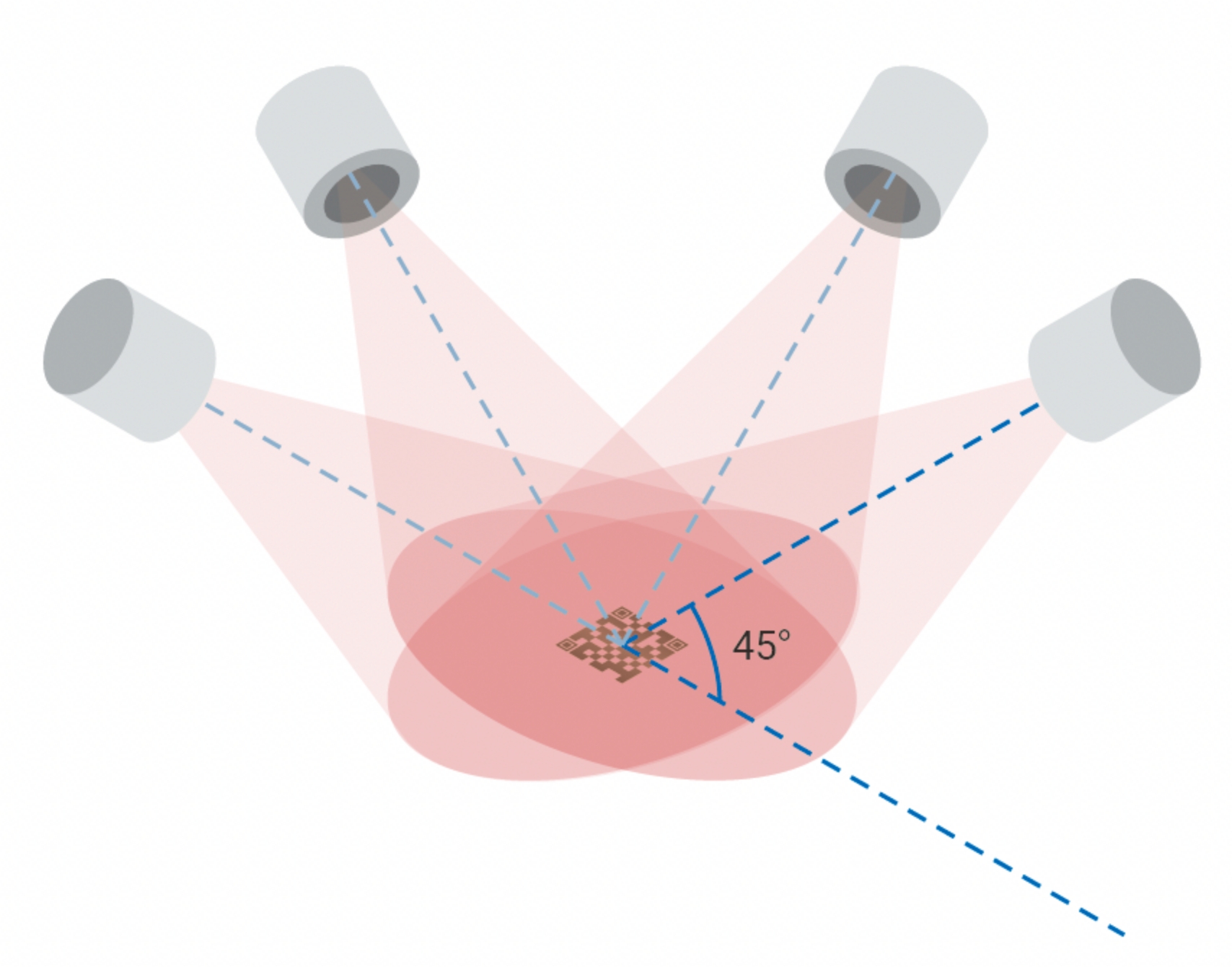
ISO/IEC 29158(ダイレクトパーツマーキング用2次元コード)
- ・拡散ドーム照明
拡散反射ドームから照射される無指向性の照明。
通常、湾曲したパーツを検査するために使用されます。 - ・垂直(90°)照明
検査ワークの平面に対して光軸が90±15°で入射する照明。 - ・N°方向照明(4方向、2方向、1方向)
シンボル表面に対して光軸が斜め方向で入射する照明です。照射角度に規定はありません。使用した照明の方向、角度は検証結果に記載が必要です。
オムロンのコード検証機LVSシリーズは、拡散ドーム照明・30°照明(4方向、2方向、1方向)に対応しています。
検証機の精度基準
検証機の精度基準に関する機能要件は、ISO/IEC 15426-1などの検証機適合仕様で規定されています。
定期的にキャリブレーション(校正)を行うことにより、検証機を常に規格に準拠した状態に保つことができ、検証機の正確性を担保できます。
キャリブレーションの方法
オムロンのコード検証機には、以下のようなキャリブレーション用カードが付属しています。
カードには特定の測定値(反射率など)が得られるコードが印刷されており、このコードを検証したときの測定値が許容範囲に入るように検証機をキャリブレーションします。
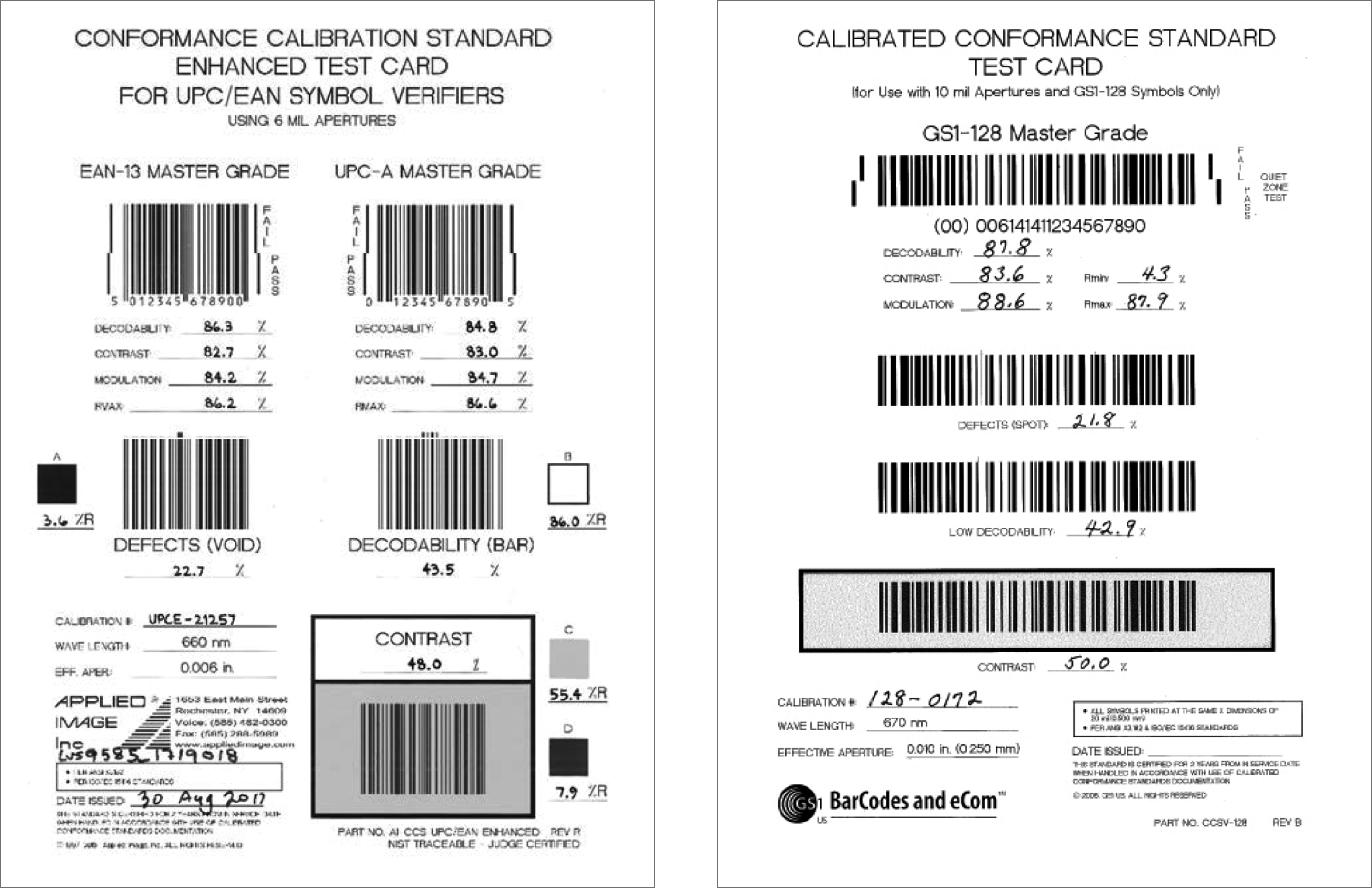
キャリブレーション用カードの交換
キャリブレーション用カードは、2年ごとに交換する必要があります。
直射日光を避けて清潔な場所で保管し、傷や汚れ、または何らかの破損が見られる場合は適宜交換してください。
4.コード検証に関する規格
検証方法に関する規格
正確なコード検証を行うために、各規格で印刷品質試験仕様と検証機適合仕様が定められています。
コード検証機は、必ずこれらの規格に準拠していることが求められます。
印刷品質試験仕様
主に、検証に必要な検査項目や各項目の点数の算出方法について定めた規格です。
検証時の照明角度などのハードウェア条件についてもこの規格で厳密に定められています。
検証機適合仕様
検証機としての精度を備えるために必要な機能や、キャリブレーションの実施などについて定めた規格です。
コードそのものの関連規格
シンボル体系仕様
形状や寸法、桁数などの特徴、符号化/復号化方法の定義を示す仕様です。
各コードを仕様通りに正しく作成するために参照します。
- 例:ISO/IEC 16022
- DataMatrixのシンボル体系仕様。
- 例:ISO/IEC 18004
- QRコードのシンボル体系仕様。
アプリケーション仕様
特定の業界・用途で使用されるコードの形式を定めた仕様です。
軍用、医療、航空輸送、トラック輸送、小売業など、さまざまな業界で独自の規格が定められています。
- 例:GS1総合仕様書
- 製造年月日、使用期限、ロット番号、シリアル番号など、製品を流通させるために必要な属性情報を付与できるコードの仕様を定めたものです。
この仕様に従って作成されたコードは、この仕様をサポートする機器で情報を適切に読み取ることができます。
- 例:医療用医薬品新コード表示ガイドライン
- 名前や外見に類似が多い医薬品の取り違え事故を防止するために厚生労働省が2006年に発出した「医療用医薬品へのバーコード表示の実施について」の通知を受けて、日本製薬団体連合会(FPMAJ)が策定したガイドラインです。
厚生労働省通知では、医薬品の包装単位ごとに商品コードや有効期限、数量、製造番号をバーコードで表示すること、バーコードはJANコードやITFコードではなくGS1データバーを使用することなどが規定されており、日薬連のガイドラインでは新しいコードの具体的な導入方法を示しています。
技術解説ダウンロード
コード検証機基礎知識
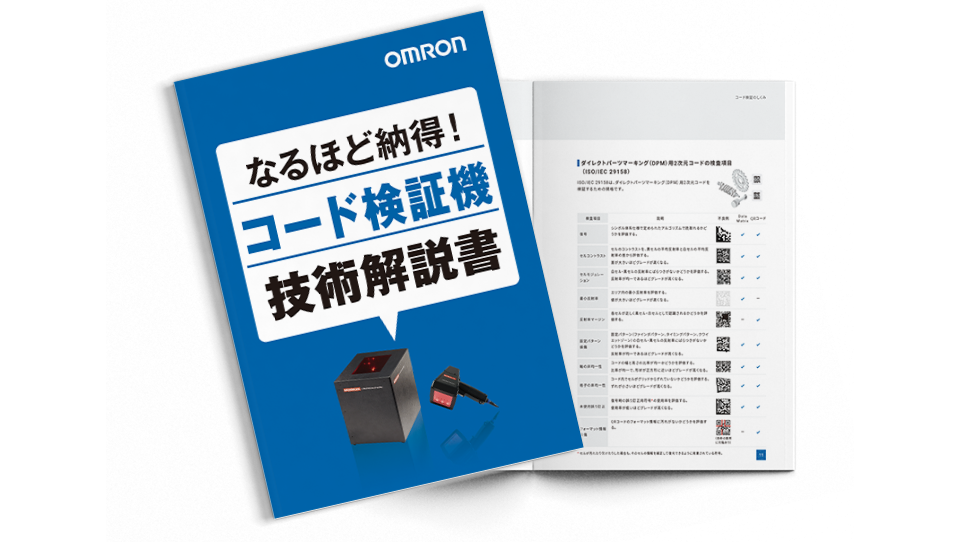