予防保全(TBM)
予防保全(TBM)とは?
予防保全とは、定期的に保全業務を行うことによって、重大な事故や設備停止につながるトラブルやリスクを未然に防ぐことを目的とした保全方法です。
予防保全方式の一つして、時間基準保全 (Time Based Maintenance) があります。文字通り時間を基準として定期的に保全を行う方法です。一定期間ごとに修理や部品交換を行うことで、設備の正常状態を維持し続けます。特に使用状況が大きく変動しない設備に関しては、メンテナンスサイクルを設定することで多くの故障を防ぐことが可能になりますが、交換部品などは最短のサイクルに合わせる必要があるため、メンテナンスコスト自体は高価になる傾向がある保全方式です。
予防保全とその他の保全、違いについて
予防保全とその他の保全方式との違いについて説明します。
事後保全とは?
予防保全と事後保全の違い
事後保全とは、設備が異常状態となる故障が発生した際に対応する保全方法です。都度発生する異常に対して対応するため何も起きなければ保全工数が最小になりますが、一方で一度の異常による影響が重大な事故につながる可能性も含んでおり、損失額としては最も大きくなるリスクがあります。
予防保全は故障しないように事前に対応する保全であり、事後保全は故障してから対応するための保全であるため、保全のタイミングと目的が異なります。
予知保全・予兆保全とは?
予防保全との違い
予知保全は、監視機器を使って設備の状態を24時間リアルタイムで監視し、設備が故障する前の兆候を予測し、発見し対応する新たな保全の方法です。予防保全は計画されたスケジュールに沿ってメンテナンスを行いますが、予知保全では設備の異常の兆候を捉えたタイミングでメンテナンスの対応を行うので、定期点検の合間に発生する突発的な故障によるダウンタイムリスクや、交換に掛かっていた過剰な部品交換費用の削減、更には保全頻度を最適化する事での人件費削減も期待されている保全方式です。
定期保全とは?
予防保全と定期保全の違い
定期保全は予防保全の一つの方式です。JISでは、従来の故障記録、保全記録の評価から周期を決め、周期ごとに行う保全方式と定義されています。
計画保全とは?
予防保全と計画保全の違い
計画保全とは、定期保全を実行するにあたってより上流で検討が必要なものです。予防保全に限らず設備保全業務全体を適正に実施できるように、方法やその計画、評価方法や期待される改善効果などを元に合理性のある計画から保全が実行される仕組みづくりを指します。
予防保全の目的やメリット
予防保全の目的やメリットについて説明致します。
製品品質の維持
設備が故障もしくは劣化することで製品を製造する能力に影響が生じ、それは製品品質に直結します。定期的な保全業務を行うことで、設備の状態を最適な状態に保つことで、同時に製品品質を維持する事にもつながります。
生産性の向上
(ダウンタイムの回避)
突然、生産設備が止まるような故障や異常が発生すると、生産が復旧するまでの部品交換や修理の時間、更には交換に必要な部品が到着するまでの期間は生産を止めることになり企業にとっては大きな打撃となります。定期的な工数はかかりますが、一定期間ごとに部品交換やメンテナンスを実施することで重大な影響のあるダウンタイムを回避することができます。
保全業務が計画的にできる
事後保全では、突発的な故障に対応しなければならず、夜間や休日に呼び出しがかかるような業務が発生する可能性があります。定期的な予防保全であれば、通常勤務時間内に保全を実施するスケジュールを組むことができ、計画的な運用が可能になります。
予防保全のデメリット
予防保全のデメリットについて説明します。
オーバーメンテナンス
予防保全では定期的なメンテナンスを行うため、点検時期になれば設備の稼働率や負荷状況に限らず保全を行うことになります。全く劣化していない部品や寿命が残っているにも限らず交換をしてしまうなど、過剰な保全業務を行ってしまうことがあり、現場の交換コストや部品在庫、工数の圧迫につながるオーバーメンテナンスとなることがあります。
保全員の作業工数がかかる
故障や異常とは関係なく定期的な保全業務を行わなければならないため、事後保全や予知保全と比較すると、メンテナンスの工数が増えることになります。定型業務は保全員によってはモチベーションの低い作業となるため、保全員の作業工数を増やす点がデメリットとなります。
IoTを活用して
予防保全から予知保全へ
予知保全とは、従来の計画的なスケジュールに従って設備をメンテナンスする予防保全と異なり、監視機器を使って設備の状態を24時間リアルタイムで監視し、設備が故障する前に発見し対応する新たな保全の方法です。予知保全は予防保全とは異なり、設備停止によるダウンタイムリスクを最小化するだけでなく、点検の頻度や交換部品も最適化する事で保全コストの削減にもつながることから注目を集める保全方式です。
予知保全の具体的な事例
予知保全の事例について、2件紹介いたします。
事例①食品業界
ホモジナイザ内パッキン消耗による
品質低下に対する予知保全
導入前の課題
油分/水分を均質化するホモジナイザは、製造品質を担保するために非常に重要な装置です。とくにホモジナイザ内部の消耗部品である樹脂パッキンの劣化は製造品質に関わる異常の1つですが、この劣化は今までどのような手段を用いても検知することが困難な異常です。そのため、早めの定期メンテナンスによる対応がメインでしたが、定期保全の間にもまだ品質低下のリスクが残ることとメンテナンスコストの増加が課題となります。
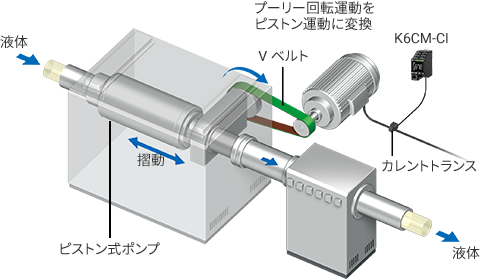
実施したソリューション内容
パッキンを含む摺動部を駆動しているモータの状態監視を行うことで、パッキンの摩耗異常の検出が可能となりました。オムロンのモータ状態監視機器K6CM-CIはモータにつながる負荷側の異常の兆候を捉えることができます。
導入後の結果・効果
パッキンの劣化状態の見える化ができたため、品質問題の未然防止と保全コストを抑えることが可能となります。それにより食品の品質維持に繋がり、消費者に安心を与え企業ブランドの向上につながることが期待されます。
事例②デジタル業界
自動搬送装置における突発停止に
対する予知保全
導入前の課題
半導体の自動搬送装置の突発停止は生産計画の遅延や納期トラブルなどにつながり大きな機会損失を招きます。自動搬送装置制御盤の温度上昇による加熱保護での装置停止を起こしてから、暫定対策として定期的に保全員による温度点検を実施します。しかしながら、クリーンルーム内にある制御盤の点検は非常に多くの工数がかかるため、保全員は頻度高く点検できずに突発停止リスクが生じることが課題となります。
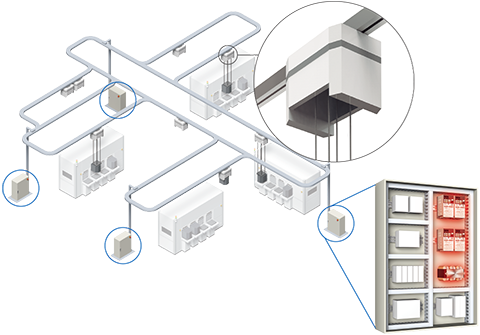
実施したソリューション内容
設備設計グループよりプロジェクトが立ち上がり、制御盤内の温度の常時監視が可能な点でオムロンの温度状態監視機器K6PMが検討対象となります。検討内容として、実際に異常を模擬し状態監視機器からの警報を受信後、対策のために保全員が現場に到着するまでの時間の評価が必要です。評価結果を確認することで、突発停止を防ぐ十分な検出精度と時間を確保できることがわかります。実際の効果の結果の確認が取れたことで他工場にも展開し導入を拡大している状況です。
導入後の結果・効果
お客様は多くのソリューションを同時に検証される中で、オムロンは検討や予知保全システム構築の簡単さと言った「短期間で持続的な保全活動に進化できる」という観点での貢献が可能です。具体的には装置の突発停止リスクを低減することができるだけでなく、導入における設備投資コスト、データアナリストの育成コスト、検出漏れリスクなどの点でオムロンの優位性が確認され、お客様の突発停止リスクの削減に貢献しています。