CBM
CBM(状態基準保全)とは
状態基準保全 (Condition Based Maintenance) とは生産設備や装置、各部品の状態や稼働状況を基準とし、劣化状況に応じてメンテナンスをする手法です。設備が壊れそうな際に対応する保全方法のため、不要なメンテナンスコストを抑えることが可能です。但し設備の状態を確認するスキルやシステムは高度な物が求められるため属人的な作業となり、人によっては見落としなどのリスクにつながる、そもそものシステム運用が実現できないといったデメリットがあります。設備の劣化していく予兆をとらえることができる段階まで行くと、一歩進んだ予知保全としてより最適な設備保全を行うことが可能となります。
CBM導入の目的・メリット
CBM導入における目的とメリットには大きく3つあります。
機械の安定稼働と長寿命化
事後保全では通常、機械に故障が起きてからメンテナンスや補修に移るため、予測ができない突発停止によって生じるダウンタイムが稼働率に大きな影響を与えます。予防保全では定期的なメンテナンスや部品交換などによって事後保全よりも設備停止のリスクは減らせますが0ではなく、定期的に設備を停止することから設備の稼働率が低下する問題があります。一方で状態基準保全では、機械が異常を発生する前の状態を確認してメンテナンスを行うことで突発停止を防ぐことができ、メンテナンス頻度を最適化する事で保全による設備停止も最小化する事ができます。また適切なタイミングでメンテナンスを実施することは、機会の状態を最適に保つことができ、高寿命化にもつながります。
メンテナンス頻度の最適化と
コスト削減
TBMによる定期保全では、定期的に部品の交換やメンテナンスを行うことで、設備停止のリスクは一定の割合で減らすことが可能です。しかし、メンテナンスの周期は最も寿命が短い製品に左右されるため、実際には不具合が起きる前のタイミングであるにも関わらず、寿命が残っている部品と交換することで部品代と保全工数の両方を圧迫することとなります。CBMでは設備の状態を見てからメンテナンスの対応に移るため、メンテナンス頻度を最適化することができ、今まで寿命が残っているにもかかわらず交換していた部品の使用時間を延ばせることから、交換する部材量も最適化する事ができ、交換部材のコスト削減にもつながります。
保全業務の標準化
騒音の中から設備の異常を聞き分ける聴覚やいつもと違う設備の揺れを感じ取る触覚など、メンテナンス要否の判断は経験値に依存します。そのため属人的な作業となりやすく、保全にばらつきが生じます。匠が長年培ってきたノウハウや五感による保全判断を自動化する事で、保全業務の標準化につながり、若手でも熟練の保全員と同様の保全判断を実現することができ、若手の育成や技術の伝承にも貢献が可能です。
CBMとTBM、BMとの違い
CBM(状態基準保全)、TBM(時間基準保全)、BM(事後保全)は下記の分類となります。
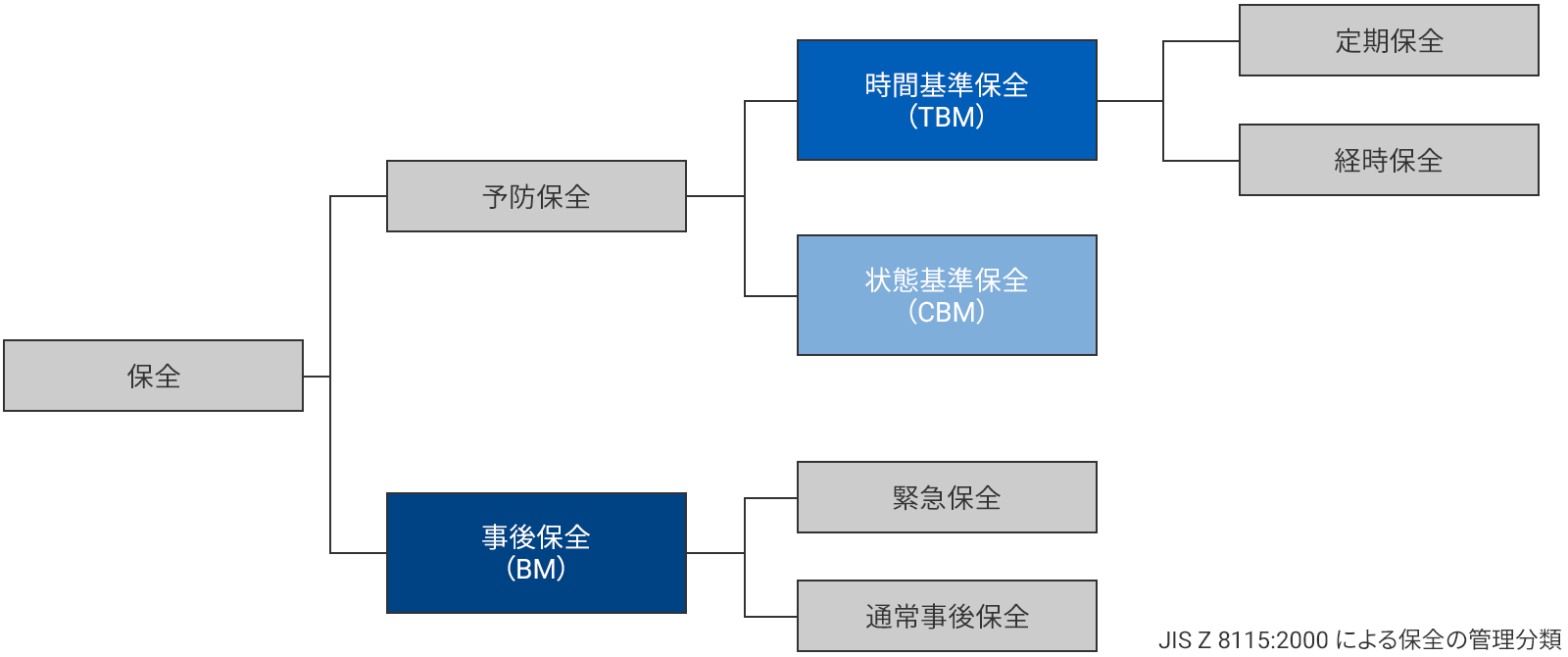
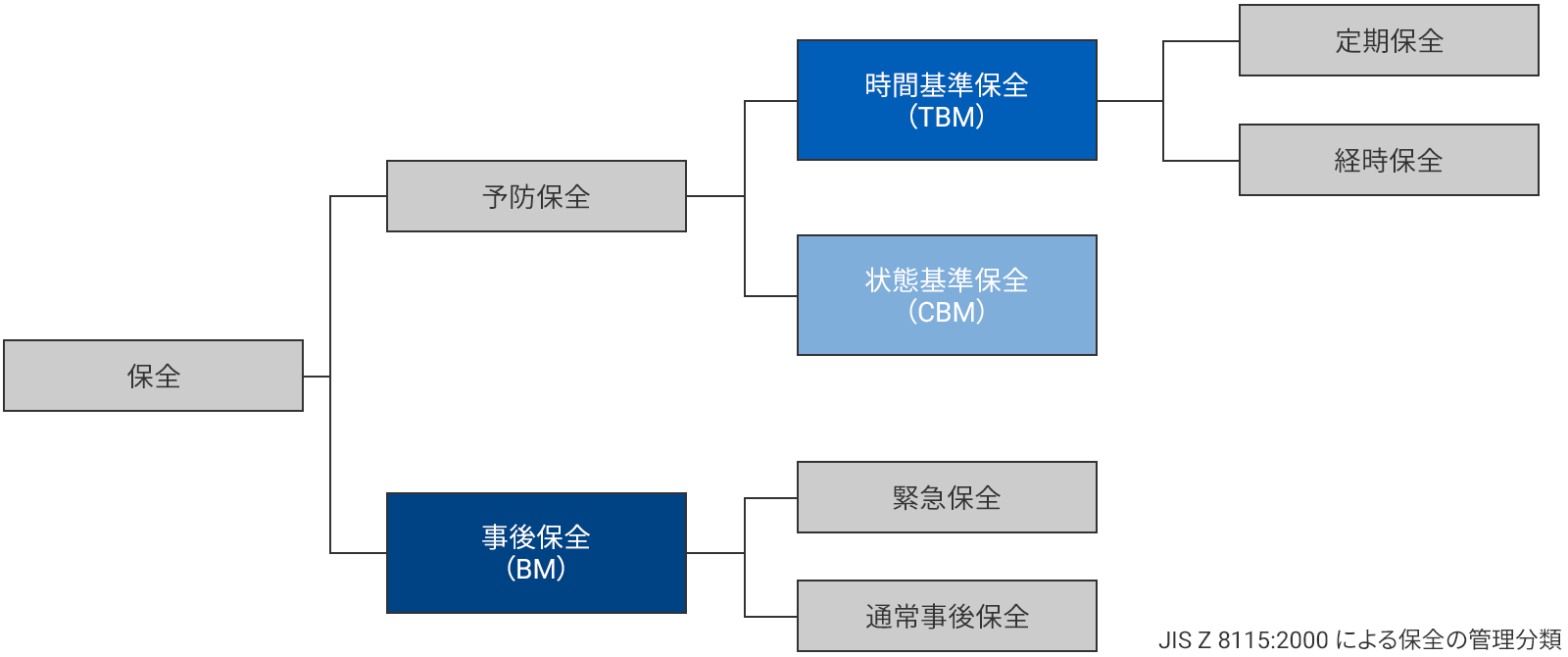
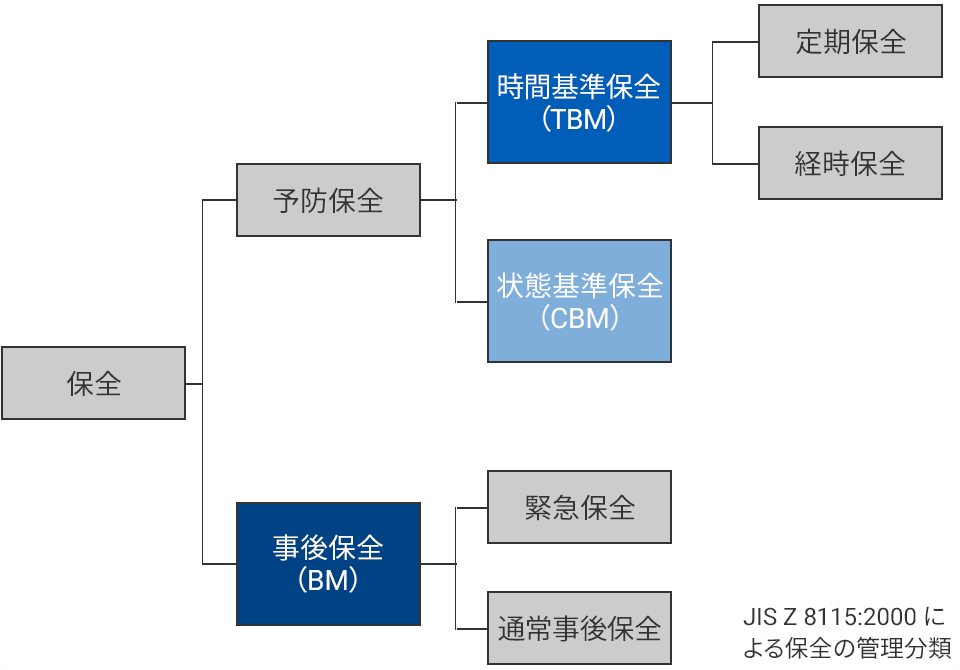
保全は大きく分けて予防保全と事後保全 (BM) に分類され、予防保全の中でもTBM(時間基準保全)とCBM(状態基準保全)の2つに分類されます。
CBMとTBMの違いは、どちらも予防保全の分類ですが、メンテナンスを実施する基準にあります。TBMの細かな分類として定期保全や経時保全がありますがどちらも時間を基準としており、経過した時間や定期的に設定された時間に対してメンテナンスを行うため、現場での運用が習慣化しやすく定期的に設備状態が更新されますが、一方で設備に異常が見られない状態でもメンテナンスを行い過剰保全によって余分なコストが発生します。一方でCBMは設備の状態を基準とするため、メンテナンス頻度やコストをTBMと比較して小さくできる保全方法と考えられています。
CBMとBMの違いは、異常が起きる前に対応するか、異常が起きてから対応するかの違いとなります。前者の対応では異常が起きる前に対応する予防保全になるため、異常発生による影響を最小限にし、設備停止や不良品を作り続けるといった不具合を防ぐことができます。後者の対応では、異常が起きなければ最もメンテナンスコストを抑えることができる保全方法でありますが、異常が発生した後の対応はすべて緊急保全となり、その設備停止や交換対応の工数が比較的大きくなる保全方法です。
CBMが注目されている背景
CBMは主に以下4つの理由から、注目を集める保全方法となっております。
センシング技術の進化
センシング技術の発達により、製造現場での計測データは様々な物理量をより高速・高精度さらには安価に取得可能になっています。現場の熟練保全員が長年の経験と現場実務により培ってきた暗黙知を、最新のセンシング機器によって形式知化することでより多くの設備の保全レベルの向上が期待されます。
IoT化が進み設備データの取得が
容易に
製造現場でのIoT化の浸透と技術の進化により、データ収集とリアルタイムでの常時監視に対する導入ハードルとコストが下がり、より合理的な保全の実現が可能となっています。現場のIoT化やDX推進は、各企業が競争力維持・強化のためにスピディーに取り組まなければならない問題であり、保全活動における活用も期待されています。
AIによるビッグデータの解析
CBMの実現において、基準となる設備の状態を判断するデータ分析が非常に重要となります。現場の熟練保全員であれば五感や経験則から今までと設備の何かが違うという状態を判断し保全を行うことができます。データ上で実現するためには様々なセンシングデータや変動要因の大量にあるデータから解析する必要がありますが、近年のAI技術の進化により、異常検知や故障予測の精度がどんどん向上し、実際に現場に実装するレベルまで進化しています。
新型コロナウイルスによる
環境の変化
コロナウイルスが与えた影響も大きいです。社会の変化に伴い、製造現場においても人数の制限や、遠隔監視のニーズなど最小限の人員での対応を余儀なくされ、保全活動における熟練保全員の人依存・技術依存からの脱却という現場変革が急がれることで、よりCBMへのニーズというものが高まっています。
CBM構築における
3つの課題・デメリット
CBMは効果的な保全方法ですが、下記の様な構築に対する課題とデメリットが存在します。
一連のシステムが
大掛かりなものになってしまう
異常検知のためのデータを取得するセンシング機器、データを吸い上げる通信機器やデータサーバ、それらを設置する大規模な工事、取得したデータをモニタリングするソフト、分析するソフト、とCBM実現の為には協力部門や構成機器などが多岐に渡り、システムとしての規模がかなり大きくなってしまうことが問題に上がります。
トラブルが発生しない限り
異常データが取れない
CBMでは設備状態を基準としてメンテナンスを行うため、正常の状態と異常の状態をデータ上で認識させることが必要です。異常が模擬できる設備であれば問題はありませんが、再現が難しい異常を検知させたい場合は、異常時のデータがないため、トラブルが発生するまでデータを取得しなければならない問題があります。
機会ごと、素材ごとに
センサの値が異なるので、
画一のモデルでは対応しきれない
同じ機械や装置、ライン、もしくは異常や不良などが対象の場合でも、それぞれに個体差や機差、使用条件などが異なるため、1つの機械でCBMのモデルが構築できたとしても、工場内にある同じ機械にまったく同じように展開するのは困難であるということが想定されます。
オムロンの予知保全の特徴
オムロンの状態監視機器では、現場機器でデータ収集・分析・判定まで行うため、システム設計やデータ分析が不要になり、少ない工数・少ない費用でスモールスタートすることができます。またスモールスタートすることにより、早い段階で投資対効果の確認ができ予知保全導入に向けた判断が可能となります。
従来PLCやクラウドを使った
予知保全システム
分析が難しく、IT/OTの融合も必要で、技術的な壁や組織的な壁があり、導入障壁が高い。
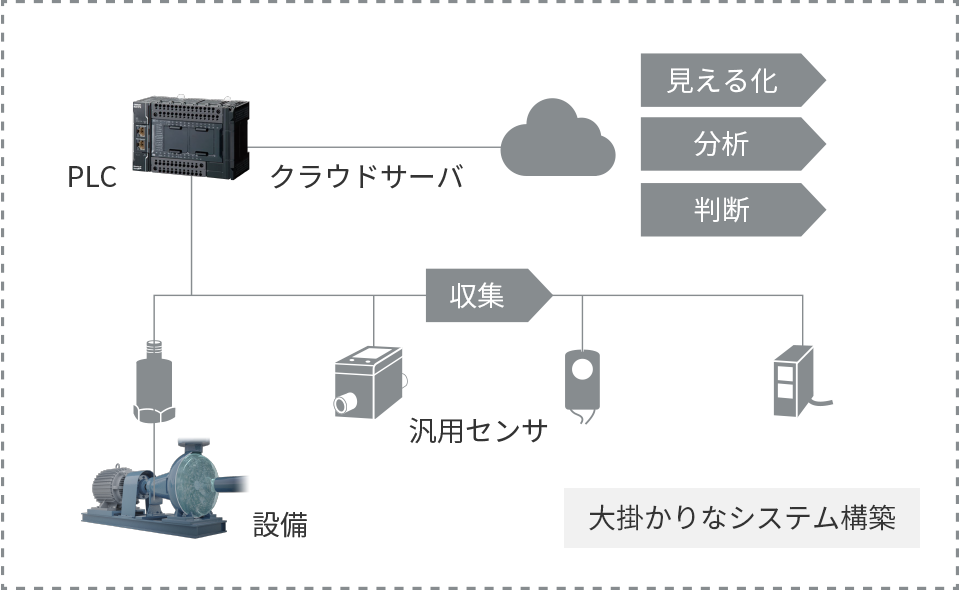

オムロンの
予知保全オムロン状態監視機器を
使った
現場完結型の
予知保全システム
分析・見える化まで保全現場で完結するので、導入障壁が低い。またそこから展開に向けた拡張も容易。まず現場で投資対効果を検証し大きく展開していくストーリーを作りやすい。
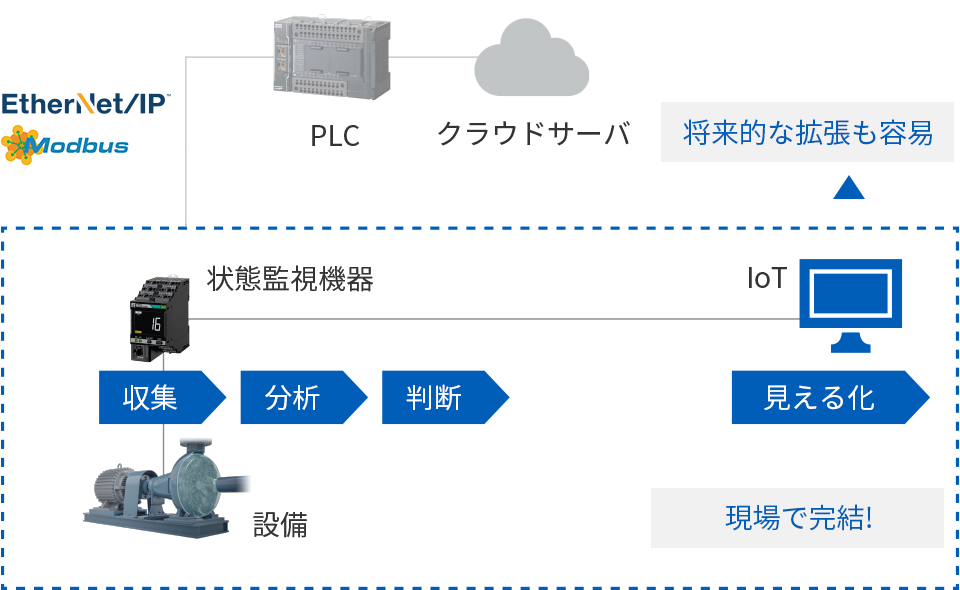
オムロン製品導入の
メリット
オムロン状態監視機器による
予知保全導入コストイメージ
故障頻度の高いアプリケーションに特化してスモールスタートしてみませんか
オムロンの状態監視機器では、リモート保全活用を想定した機能が、現場完結する形でオールインワンの搭載になっています。例えばファンやポンプのモーターなど故障頻度が高いアプリケーションに特化して現場レベルで検証をスモールスタートできます。
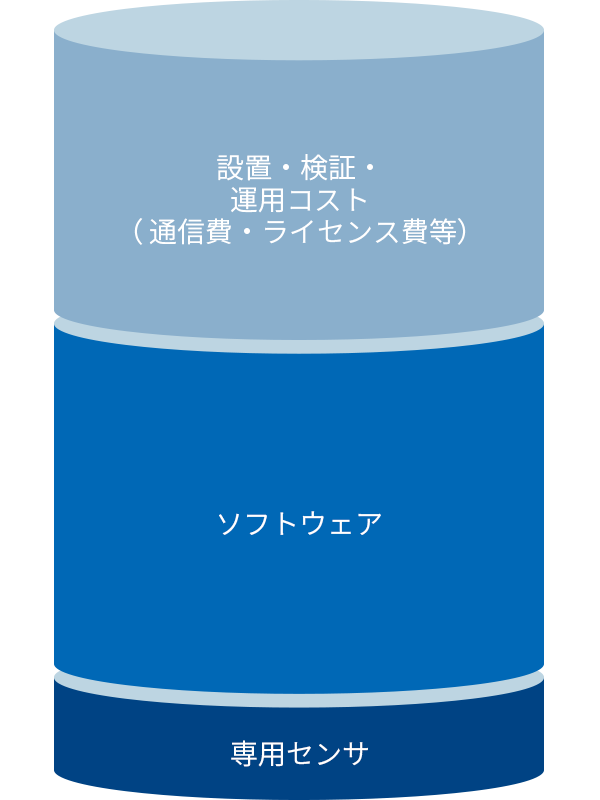
A社:クラウドシステム
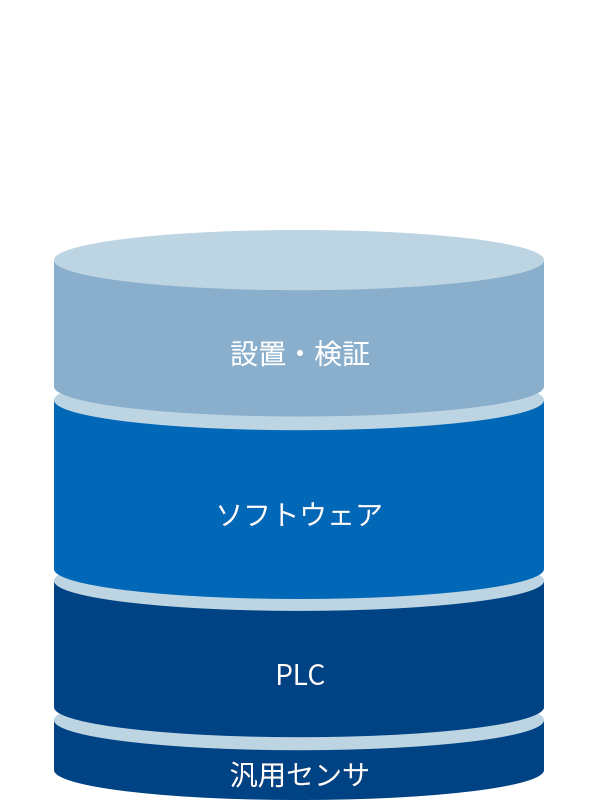
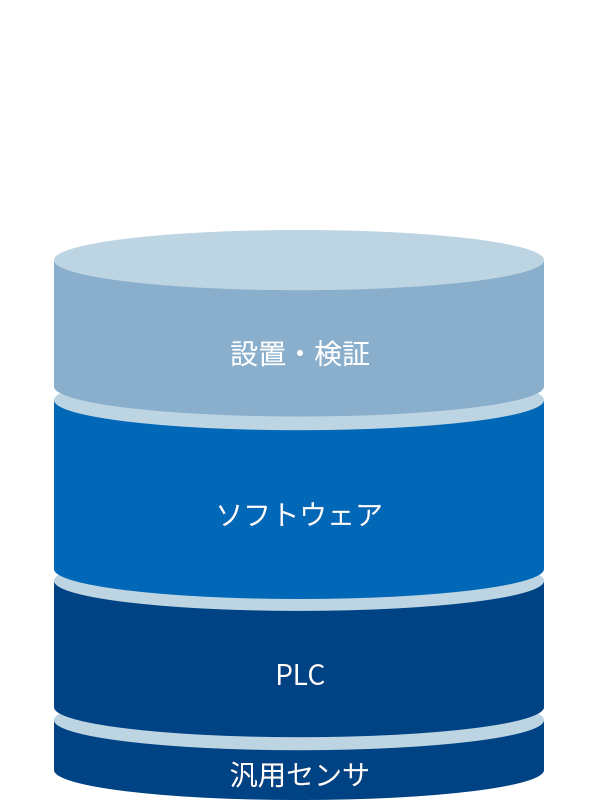
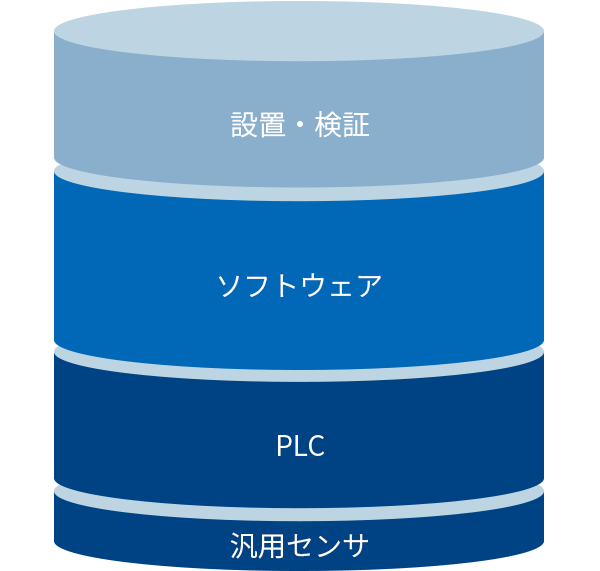
B社:PLCベースシステム
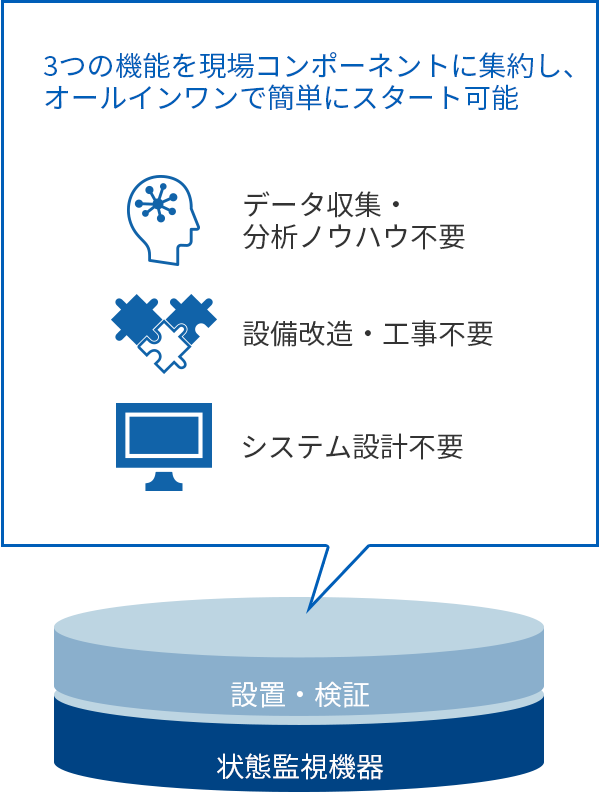
オムロン:状態監視機器システム