予知保全
予知保全とは
予知保全とは、従来の計画的なスケジュールに従って設備をメンテナンスする予防保全と異なり、監視機器を使って設備の状態を24時間リアルタイムで監視し、設備が故障する前に発見し対応する新たな保全の方法です。
予知保全システム導入事例
まずはオムロンの保全革新ソリューションで予知保全を実現した事例をご紹介します。ここで、予知保全がどのように運用されているか確認します。
事例①自動車業界
塗装乾燥工程エアダクト亀裂による
熱漏れ事故防止に対する予知保全
導入前の課題
装置の自動化が進む中、工場には現場作業者がいないエリアもあり、気づかずに異常が進行しているケースが多発しています。そのような中でエアダクトの熱漏れ事故により設備停止を余儀なくされたケースがあります。エアダクトは天井付近に敷設されているものが多く日常点検が困難であり、火災や人災など重大な事故につながる危険性も危惧されます。現状の保全リソースに限界がある中で、保全効率向上と火災リスク削減の両立を実現することが課題となります。
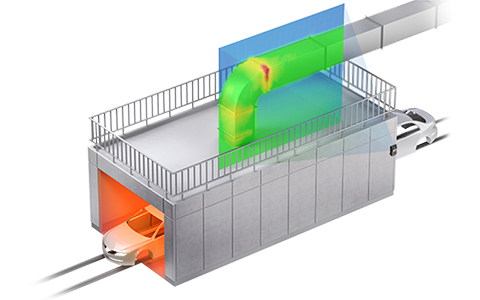
実施したソリューション内容
赤外線カメラで対象の温度を広角に監視できるオムロンの温度状態監視機器K6PMを活用し、対象設備の24時間監視を実現かのうです。温度変化をリアルタイムに捉え、異常兆候を早期に発見できます。
導入後の結果・効果
オムロンの保全革新ソリューションは温度センサと、その計測データから異常を判断する本体が一体となった構成です。非常にシンプルな構成のため、スモールスタートが可能で、余った保全予算ですぐに効果を検証できます。火災事故は、消費者への供給責任を果たせなくリスクや、管理体制に関わる企業ブランドの低下に陥る可能性があるため、周辺住民や消費者、関連会社への信頼という意味でも導入する効果を見いだせます。
事例②食品業界
ホモジナイザ内パッキン消耗による
品質低下に対する予知保全
導入前の課題
油分/水分を均質化するホモジナイザは、製造品質を担保するために非常に重要な装置です。とくにホモジナイザ内部の消耗部品である樹脂パッキンの劣化は製造品質に関わる異常の1つですが、この劣化は今までどのような手段を用いても検知することが困難な異常です。そのため、早めの定期メンテナンスによる対応がメインでしたが、定期保全の間にもまだ品質低下のリスクが残ることとメンテナンスコストの増加が課題となります。
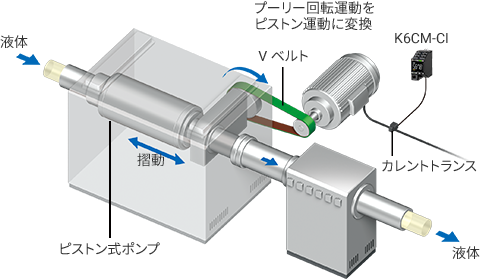
実施したソリューション内容
パッキンを含む摺動部を駆動しているモータの状態監視を行うことで、パッキンの摩耗異常の検出が可能となりました。オムロンのモータ状態監視機器K6CM-CIはモータにつながる負荷側の異常の兆候を捉えることができます。
導入後の結果・効果
パッキンの劣化状態の見える化ができたため、品質問題の未然防止と保全コストを抑えることが可能となります。それにより食品の品質維持に繋がり、消費者に安心を与え企業ブランドの向上につながることが期待されます。
事例③デジタル業界
自動搬送装置における突発停止に
対する予知保全
導入前の課題
半導体の自動搬送装置の突発停止は生産計画の遅延や納期トラブルなどにつながり大きな機会損失を招きます。自動搬送装置制御盤の温度上昇による加熱保護での装置停止を起こしてから、暫定対策として定期的に保全員による温度点検を実施します。しかしながら、クリーンルーム内にある制御盤の点検は非常に多くの工数がかかるため、保全員は頻度高く点検できずに突発停止リスクが生じることが課題となります。
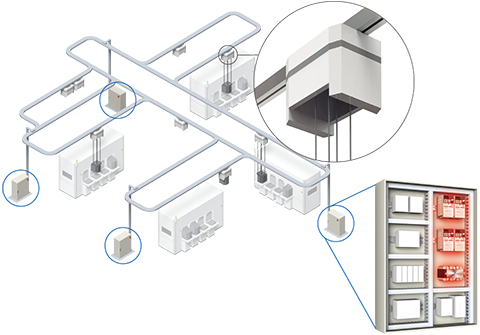
実施したソリューション内容
設備設計グループよりプロジェクトが立ち上がり、制御盤内の温度の常時監視が可能な点でオムロンの温度状態監視機器K6PMが検討対象となります。検討内容として、実際に異常を模擬し状態監視機器からの警報を受信後、対策のために保全員が現場に到着するまでの時間の評価が必要です。評価結果を確認することで、突発停止を防ぐ十分な検出精度と時間を確保できることがわかります。実際の効果の結果の確認が取れたことで他工場にも展開し導入を拡大している状況です。
導入後の結果・効果
お客様は多くのソリューションを同時に検証される中で、オムロンは検討や予知保全システム構築の簡単さと言った「短期間で持続的な保全活動に進化できる」という観点での貢献が可能です。具体的には装置の突発停止リスクを低減することができるだけでなく、導入における設備投資コスト、データアナリストの育成コスト、検出漏れリスクなどの点でオムロンの優位性が確認され、お客様の突発停止リスクの削減に貢献しています。
予知保全のための
AI導入の流れ
予知保全を実現するための手段として、昨今、AI(人工知能)活用が多くの企業の注目を集めています。ここでは、AI導入の流れを説明していきます。
1.課題共有
まずは、AIに関するソリューションを保有しているメーカと、自社の保全課題を共有します。課題を共有することで、AI活用の必要性と解決することによる効果などを確認することができます。
2.対象テーマの選定
次にテーマ選定です。ここでは、あえてテーマを絞っていくことが必要です。AI活用にはまだまだ懐疑的な人も多く、効果の見えない大きな投資に対してよく思わない人も存在します。だからこそ優先度の高いところからスモールスタートすることが重要なのです。
テーマを絞り、小さな成功を繰り返しながら大きな成果を上げていくことを目指していきます。
3.データ準備
次にAIに学習させるデータを準備します。捉えたい事象の予兆と相関のあるデータや特徴量を見出すために、複数のデータを準備しなければなりません。例えば以下のようなデータです。
- センサデータ(振動、電流など)
- 生産量データ
- 不良発生データ
- 機械制御データ
そしてこれらのデータの時系列が揃っていることが非常に重要となります。
学習に必要なデータ量については、解決したい課題によって異なります。理想としては、捉えたい事象の発生タイミングまでデータを収集することになります。
4.PoC(技術検証)
次にAI製品を活用して、データを処理していきます。すぐに本番というわけではなく、テスト環境を使った検証を開始します。これを「PoC (Proof of Concept) 」といいます。
用意したデータをもとに、AI製品にて分析を行い、設定した課題の解決を実現できるかどうか、リアルなデータを使って技術検証を行います。
5.評価システム構築
PoCで実現手段に目処がたったら、今度は評価システムを構築し、実際の生産ラインで評価を行います。
具体的には以下の項目を評価していきます。
- 実際の生産ラインへの導入可能性
- 実運用を見据えたときの検出精度の確認
- 不足している機能の確認
- 捉えた予兆を通知するシステムの確立
- 効果を確認するための評価指標の決定
予兆を通知するシステムとしては下記のような手段があります。
- 既存のモニタリングシステムに判定結果を表示する
- 汎用のBIツールを利用して可視化する
- タッチパネルなどでモニタリング画面を開発する
- 生産現場のパトランプなどで表示する
6.本番システム構築
評価システムでの検討結果を改善し、本番のシステム構築を行います。
ただしこれらのシステムは最終的にラインや工場全体での統一が必要となります。そのため、最初は簡単な手段で構築し、AI活用による成功事例を積み上げてから全体最適されたシステムを検討する必要があります。
7.運用開始
本番システムの構築が完了したら、実運用を開始します。実環境で運用する中で、さらなる精度向上を行うために、評価指標に基づいて定期的な評価を行います。
データの特性によっては再度学習を行い、精度を担保することも可能です。
予知保全でAI導入する際の
注意点
既存設備へセンサー機器の設置が
可能か調査する
生産現場では4M変動が厳しく管理されています。既存設備へセンサーを取り付ける際には、生産影響がないことの確認がとても重要です。目的を満足することを大前提とし、後付しやすいセンサーを選定します。
コストメリットについて検討する
導入に向けた整理を行う中で、抱えている課題を解決したときのメリットと、導入コストや運用コストを評価する必要があります。
オムロンの目指す予知保全
オムロンの保全革新ソリューションでは、現場に設置した監視機器でデータ収集・分析・判定まで行うため、システム設計やデータ分析が不要になり少ない工数・少ない費用でスモールスタートすることができます。またスモールスタートすることにより、早い段階で投資対効果の確認ができ予知保全導入に向けた判断が可能となります。
従来PLCやクラウドを使った
予知保全システム
分析が難しく、IT/OTの融合も必要で、技術的な壁や組織的な壁があり、導入障壁が高い。
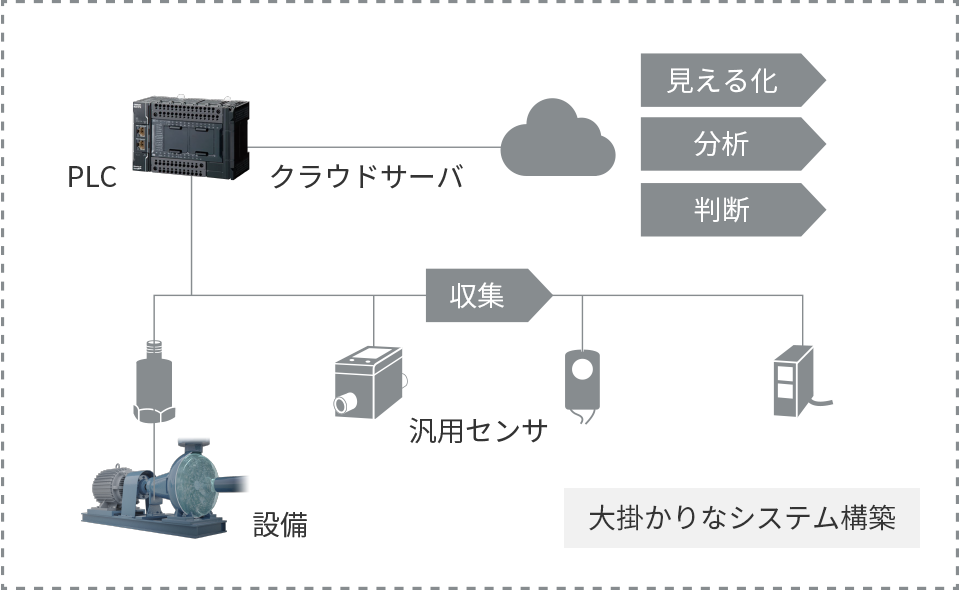

オムロンの
予知保全オムロン状態監視機器を
使った
現場完結型の
予知保全システム
分析・見える化まで保全現場で完結するので、導入障壁が低い。またそこから展開に向けた拡張も容易。まず現場で投資対効果を検証し大きく展開していくストーリーを作りやすい。
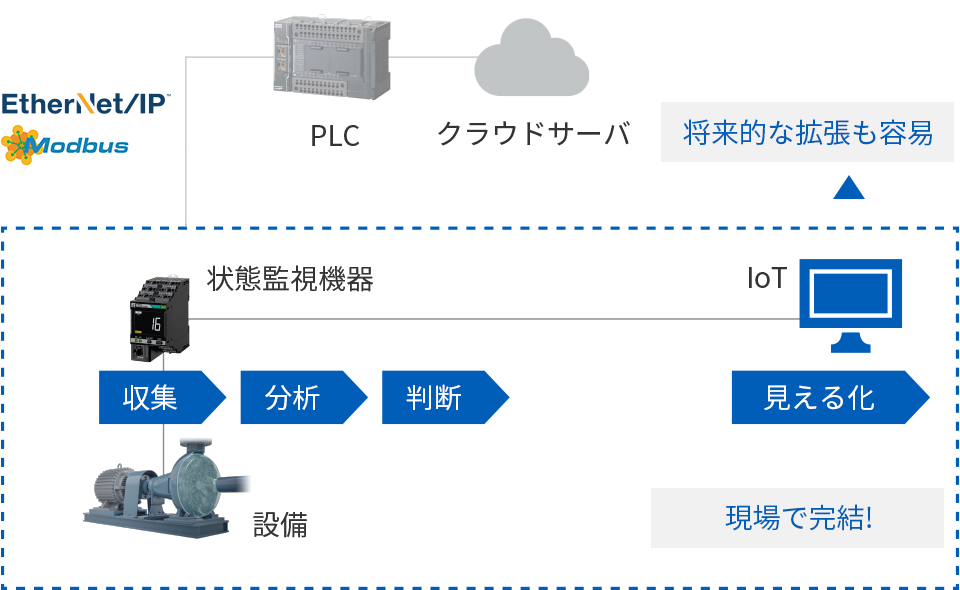