設備保全とは?
設備保全とは
設備保全 (Productive Maintenance) とは、JIS(日本工業規)において、故障の排除及び設備を正常・良好な状態に保つ活動の総称と定義されています。具体的には活動の計画、点検、検査、調整、修理、取り換えなどの作業が該当します。
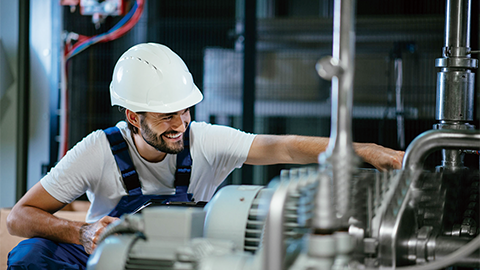
設備保全の目的や意味
設備保全の目的は、時間経過と共に劣化する設備に対して大きく分けて下記3つの目的が存在します。
安全性の確保
適切な設備状態を保つことで、設備の誤作動や故障の回数を減らすことができ、稼働率を上げることができます。加えて誤作動や故障などが要因になる重大な設備トラブルを防ぎ人命などに関わる重大な事故リスクを減らすことにもつながります。
生産活動 (QCD) の維持
設備部品を適切にメンテナンスすることで、突発破損での緊急保全を減らし、急な生産計画の変更から発生する納期遅れのリスクを減らすことができます。加えて、部品の劣化状況を把握することで、設備性能のダウンを防ぎ、製造品質の安定化にもつながります。また保全工数に関連する人件費や不良品の製造におけるコストについても削減が可能となり、全体の生産活動の維持につながります。
無駄なコストの削減
生産設備の安定的な稼働は、単純に稼働停止に依るロスを減らすだけでなく、性能劣化によって不良品を作ってしまう設備の機能低下を防ぐことができ、発生しうる無駄なコストを未然に防ぐことが可能となります。
保守・メンテナンス・
修理と設備保全の違い
設備保全は、前述の3つの目的を達成することであり、それらを実現する活動として保守・メンテナンス・修理等の行為が含まれます。
保守・メンテナンスと
設備保全の違い
一般的に保守・メンテナンスは設備が故障しないように、事前に整備や修理を行う作業を指すことが多く、設備を提供しているメーカーの提供するサービスが指されることが多いです。一方で設備を使用するユーザ側の設備を維持する活動が設備保全と言われる傾向が多いです。保守・メンテナンスと設備保全はほとんど同義です。
修理と設備保全の違い
修理は設備保全で行う活動の一部です。修理とは、設備でトラブルが発生した際に正常状態に復旧させる活動を指します。設備保全とはトラブルからの復旧に加えて、設備が正常な状態で稼働を維持するためのより包括的な活動を指します。
設備管理と設備保全の違い
設備管理とは、JIS規格上では下記のように生産管理用語の一つとして定義されています。
設備管理 (Equipment management) :設備の計画、設計、制作、調達から運用、保全を経て廃却・再利用に至るまで、設備を効率的に活用するための管理。
つまり設備管理とは保全業務におけるマネジメント領域も含めた活動のことを指し、広義では保全と同義に捉えることができます。重要であるのは、設備の運用のみでなく、事前の計画や補修などの範囲を含めた全体のマネジメントによって設備を正常な状態で稼働維持されることです。
設備保全の種類
設備保全 (Productive Maintenance) には、その内容や形態、技術の進歩などが関連して大きく分けると3種類あります。新規にできた順に、予知保全(予兆保全)、予防保全、事後保全の3種類です。以下、各項目で詳細を説明します。
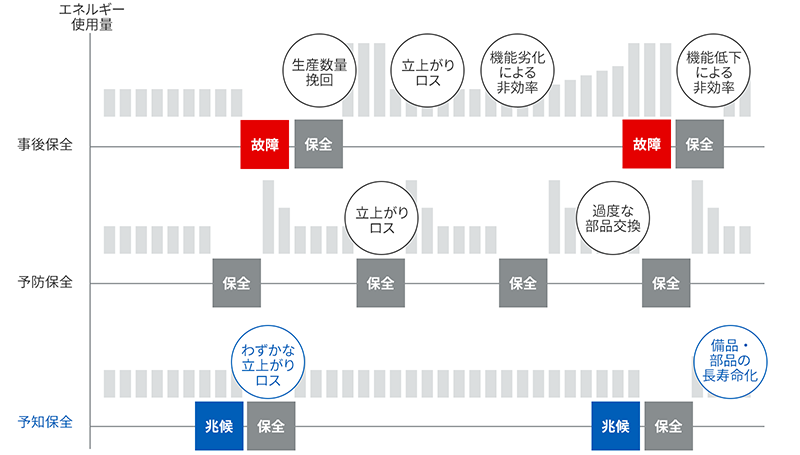
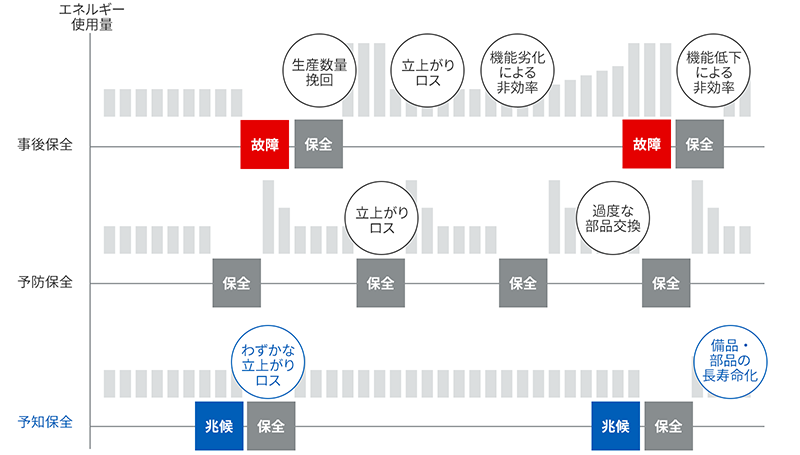
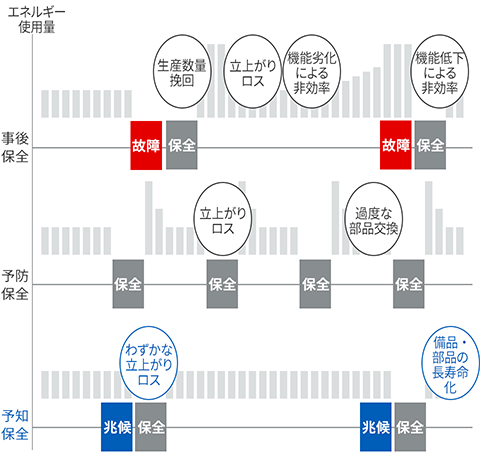
予知保全(予兆保全)
予知保全は、従来の計画的なスケジュールに従って設備をメンテナンスする予防保全と異なり、監視機器を使って設備の状態を24時間リアルタイムで監視し、設備が故障する前の兆候を予測し、発見し対応する新たな保全の方法です。後半で説明する状態基準保全 (CBM) が類義語としてありますが、「異常の予兆」を捉えるという点でより一歩進んだ保全の方法となります。システム構成としては、設備状態の計測データをクラウド上で専門のSEがデータ解析し異常を判定する方法(クラウドコンピューティング)と、計測データを現場で判定する方法(エッジコンピューティング)の2種類あり、様々なソリューションが各社から提供され始めています。この予知保全よって、定期点検後に起こっていた設備の突発的な故障によるダウンタイムをゼロにすることが現実的になってきています。また予防保全で掛かっていた過剰な部品交換費用の削減や、人手不足の解消なども期待されています。
予知保全とは?
予防保全
予防保全とは、定期的に保全業務を行うことによって、重大な事故や設備停止につながるトラブルやリスクを未然に防ぐことを目的とした保全方法です。メリットとしては前述の通り、定期的な保全によって、壊れてから対応する事後保全と比較して重大な停止リスクを大幅に軽減することができ、保全活動を定期的なイベントとして計画することで現場での運用もしやすくなります。一方で、定期的な保全活動を前提とする保全工数や交換の部材費がコストを圧迫する、定期点検においても突発故障による設備停止リスクはゼロにではできないといったデメリットがあります。これら予防保全における、定期的な保全タイミングを決定するための基準によって大きく二つの予防保全方式が存在します。
予防保全とは?
時間基準保全
時間基準保全 (Time Based Maintenance) とは、文字通り時間を基準として定期的に保全を行う方法です。一定期間ごとに修理や部品交換を行うことで、設備の正常状態を維持し続けます。特に使用状況が大きく変動しない設備に関しては、一定のメンテナンスサイクルを設定することで多くの故障を防ぐことが可能になりますが、交換部品などは最短のサイクルに合わせる必要があるため、メンテナンスコスト自体は高価になる傾向があります。
状態基準保全
状態基準保全 (Condition Based Maintenance) とは生産設備や装置、各部品の状態や稼働状況を基準とし、劣化状況に応じてメンテナンスをする手法です。設備が壊れそうな際に対応する保全方法なので、不要なメンテナンスコストを抑えることが可能です。但し一方で設備の状態を確認するためのスキルやシステムは高度な物が求められるため、属人的な作業となり人によっては見落としなどのリスクにつながる、そもそものシステム運用が実現できないといったデメリットがあります。設備の劣化していく予兆をとらまえることができる段階まで行くと、一歩進んだ予知保全としてより最適な設備保全を行うことが可能となります。
事後保全
事後保全 (Breakdown Maintenance) とは、設備が異常状態となる故障が発生した際に対応する保全方法です。都度発生する異常に対して対応するため、保全工数は最小で済みますが、一方で一度の異常による影響が重大な事故につながる可能性も含んでおり、損失額としては最も大きくなるリスクがあります。事後保全として対応しなければならない事象としては下記2種類の故障があります。
機能停止型故障
機能停止型故障とは、生産設備が停止するような故障のことを指します。
実際に設備が停止する、もしくは再開不可能な状況になってはじめて気づく際には大幅な設備停止時間が発生します。
機能低下型故障
機能低下型故障とは、生産設備の性能が低下するような故障のことを指します。実際には製造のタクトが落ちたり、歩留り率が低くなっていくことでわかる故障であり、不良品の廃棄やエネルギー効率が落ちるなどのロスが発生します。
設備保全の問題点や
デメリット
今までの記述内容の中で、各保全方式や共通する問題点やデメリットがあるので、以下に代表的な3つの内容を記載します。
予防保全コストが生産コストに直結
予防保全において、定期的にメンテナンスを計画することで保全工数と交換部材費用が、年間でかかる保全費用として固定されてしまいます。そのため生産コストにおけるベースとして考えることとなり、会社としての利益をダイレクトに圧迫する要因となります。
導入にコストがかかる
予知保全(予兆保全)の実現に当たって、異常の兆候を検知するためにIoTデバイスや、クラウド・AIシステムなどの技術的に高度な機器の採用が必要になります。ROIの計算ができればコストが高くなることも問題にはなりませんが、導入だけではなく、運用や保守などの全体を考慮した際に、人的リソースや効果効用の大小がお客様だけではなく、工程や品目ごとにも異なるため、工場全体で見た際には導入コストがかかるという問題点が多く見られます。
人的リソースのスキル差が発生する
予知保全(予兆保全)の実現においては、熟練技術者のスキルをデジタル化することが必要です。ベテランの保全員は、例えば温度や湿度、音やにおいなど総合的に五感で捉えたいつもと違う状態という感覚を頼りながら設備の正常な状態というものを維持します。こういった感覚が磨かれるには年単位での実務経験が必要となり、保全員のシフトや工場ごとの教育差などによって、人によって同じ装置でも設備の稼働状況が全く異なるといった問題が生じます。
設備保全のあるべき姿
オムロンでは保全業務から製造現場を革新するために、保全革新ソリューションというコンセプトを掲げ、これまでの三現主義の現場思想を重視しながらも「現物をデータで監視・分析し、現実をリモートで最適に捉え判定し、適切なタイミングで現場作業をする」新たな三現主義(新・三現主義)を考案しています。現場のコンポーネント機器レベルでの高度な状態監視により、明日から手軽に始められる保全革新ソリューションを提案しています。
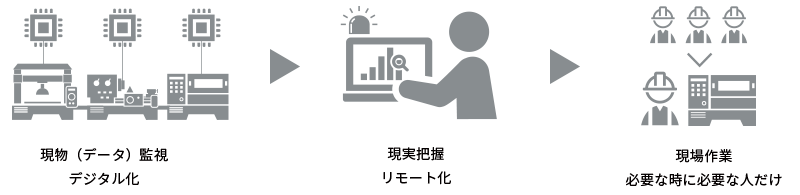
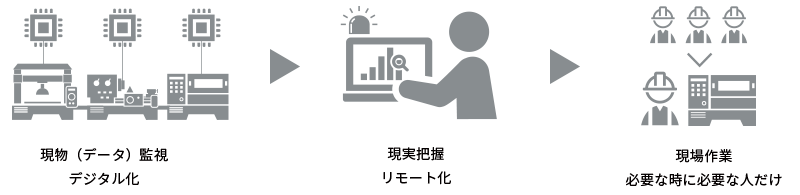
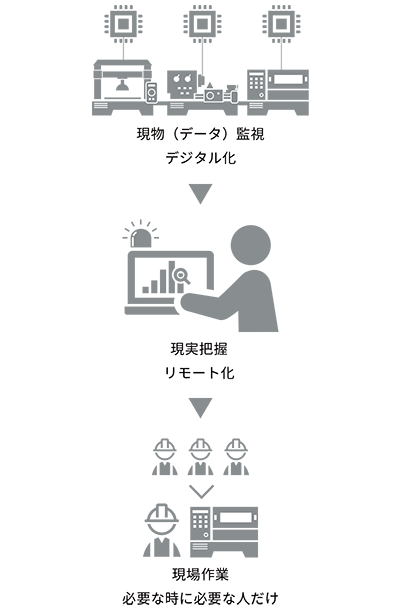
今後設備の予知保全化がさらに進む中で重要となる設備の状態監視。それらを実現する3つの価値として"匠の保全の再現"、"レトロフィット"、"簡単リモート監視"をコンポーネント機器に埋め込むことで実現を加速し、保全現場の革新に貢献していきます。
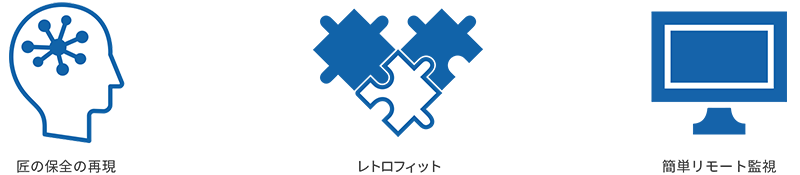
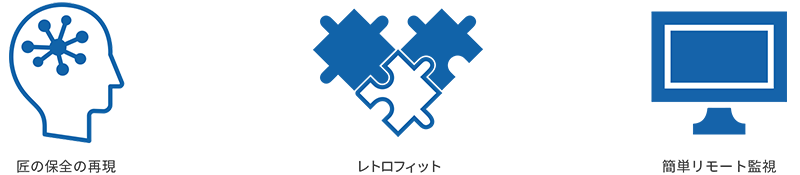
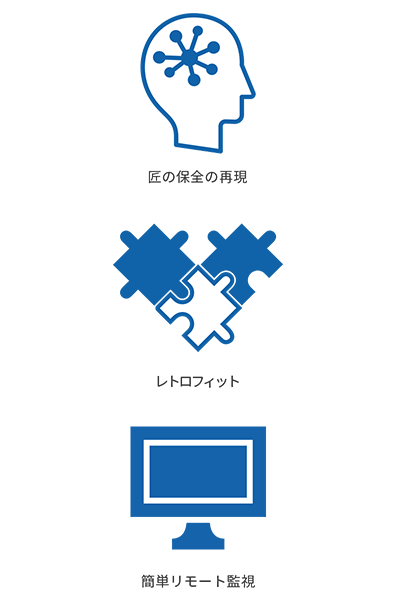