この事例の詳しい商品情報はこちら
ヒータ状態監視機器 K7TM
商品情報ページへ
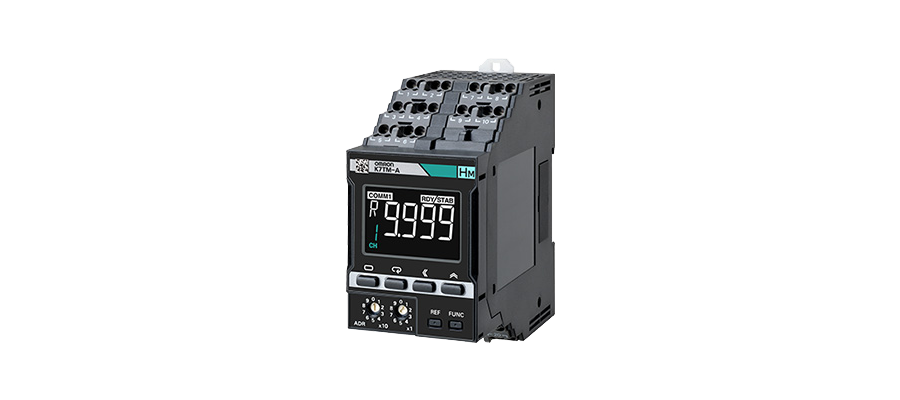
樹脂成型機は、ヒータ機器の点数が多く装置構造が複雑、加えて機器の劣化によるヒータ断線で設備停止の発生頻度が高い装置である。そのため一度の設備停止から復旧時間が長くなる傾向にあり、大型設備になるとさらに復旧に時間を要する。
停止時間を最小化するためには定期的なメンテナンスが重要であるが、工数を要する保全時間を定期的かつ十分に確保することは非常に難しい。
メンテナンスの難しさから事後保全で対応することが多い設備のため、保全効率と稼働効率を両立させるために、ヒータの予知保全化のニーズが高い設備のひとつである。
稼働中の既存設備のひとつに状態監視機器を設置し、データ取得と分析を実施。モデル装置として稼働する。モデル装置の結果から、まずは同工場の同ラインに横展開予定で着手。
工場保全全体のCBM (Condition Based Maintenance)化の構想の下、ヒータの状態監視にオムロンの状態監視機器K7TMの採用を決定。また、他工場においても同監視手法で展開を予定。
データから保全タイミングの判断が可能となり、設備の保全活動の判断指標を定量化することに成功。事後対応がなくなり保全効率が向上した。
既存設備への後付けが可能なため、効果が得られた装置に対して予算を確保しながら横展開が可能。
設備の定期点検にかかる稼働停止や事後保全による復旧時間を削減することで、稼働率が向上。さらに生産効率が上がったことにより設備の使用電力の削減にも貢献。
特にヒータ設備は電力消費量が多い傾向にあり、電力使用量削減の期待効果は大きい。
定期的な絶縁抵抗計測などの点検は行うも、故障の兆候を見つけるには不十分で事後保全が現場で発生。
点検スキルは個人にも依るため属人的な保全活動となっていた。
ヒータの状態を定量化することで、保全判断のバラツキがなくなり、属人的な保全活動を改善。
閾値を超えたタイミングでの保全 (CBM)を実現。