- ビッグデータから見える製造現場
オムロン草津工場事例
前編 製造現場でのビッグデータ活用
ITによる分析に懐疑的だった現場のベテラン技術者が絶賛
オムロンの製造工程でビッグデータ活用した品質データ収集の事例を生産技術のベテラン自らが紹介します。
課題、導入後の成果、これからの製造現場などについて具体的な数字を交えて解説。従来の導入事例と違った現場の技術者ならではの視点で語ったレポートです。
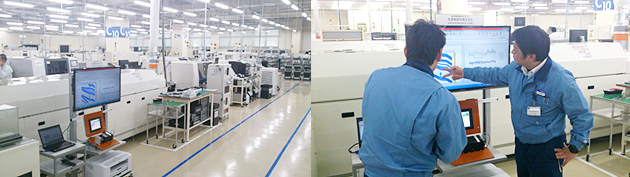
製造現場でのビッグデータ活用
日本の産業の中で、第2次産業は依然2割以上を占めています。新興国もまず製造業を中心に発展していくでしょう。そのため、日本の製造業として改善し続けて行こうという機運は依然強く残っています。
その改善の一つが、今回ご紹介する「ビッグデータの活用」です。
工場のビッグデータ活用は大きなポテンシャルがあります。工場の製造装置・設備の中にはすでに多くのセンサが使われているからです。例えば、チップマウンタという装置の中には200個近くのセンサが設置されており、絶えず検知・計測しています。これらのセンサのデータを装置の制御だけでなく、改善にも活用できれば、さらにいろんなことが分かってくるはずです。
一方で課題もあります。データを収集する仕組みを構築するのはなかなか難しいのです。収集に手間がかかったら現場の人は絶対導入しません。従って、これからご紹介するようなSysmacデータベース直結ソリューションのような形で自動的に実行できることがとても重要です。
また収集ができたとしても、どうアクションを起こさせるかも重要です。そのためには、現場がアクションを起こす気になる分析と見える化も大切になってきます。
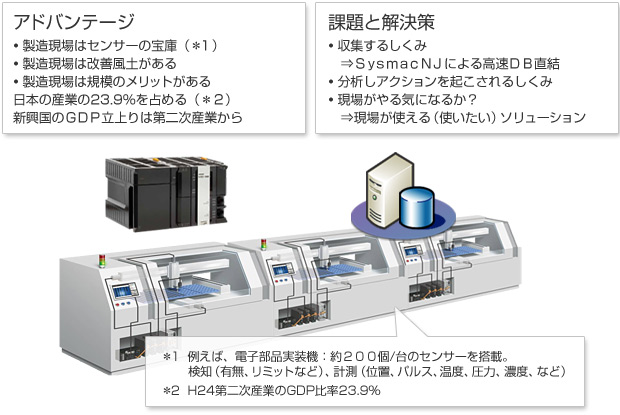
製造現場には非常に高いアドバンテージがある。FAとITの融合は現場起点が成功のカギ
オムロン草津工場のご紹介
当社の草津工場を簡単にご説明します。
草津工場ではFA用のコントローラを生産しています。プリント基板が入っている製品が主ですので、アセンブリ型の組み立て工場です。その特徴は多品種少量生産で、約4000品目の製品のうち、最小では1ロット1台での生産もしています。
そのため、機種切り替え、段取り替えが頻繁に起きます。例えば、実装工程の段取り替えが一ライン当たり一日平均28回も行っています。
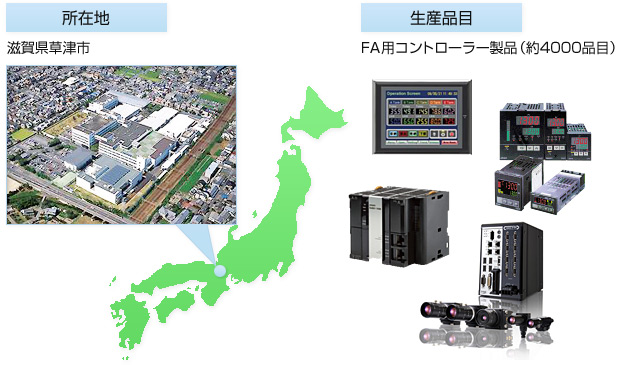
多品種少量生産の場合、品質や生産性の改善をするときに、数少ない生産機会を見計らって何が課題なのかをつかまなくてはいけません。
実は、これは大量生産の場合でも同じことが言えます。あるインクプリンタのトナー生産工程では、カートリッジは大量生産だが、一個一個の加工時間は何ミリ秒であり、その挙動をつかむのが大変に難しくなっているとのことです。
草津工場は2010年比でエネルギーを半減させる取り組みをしています。そのため、品質データや生産データに加えて、エネルギーデータを収集しています。さらに人の働くデータなどいろんな情報が生産現場でも活用されるようになっています。
このように大量生産でも多品種少量生産でも、今まで以上に生産現場の改善を行おうとすると、さらに細かいデータや取りにくいデータを取ることが必要になっているのです。
草津工場での事例
プリント基板の生産ラインは、下図の通りです。簡単に説明すると、配線がなされたプリント基板上に、電子部品、LSI、メモリを載せていって、最後にはんだ付けしていくラインです。
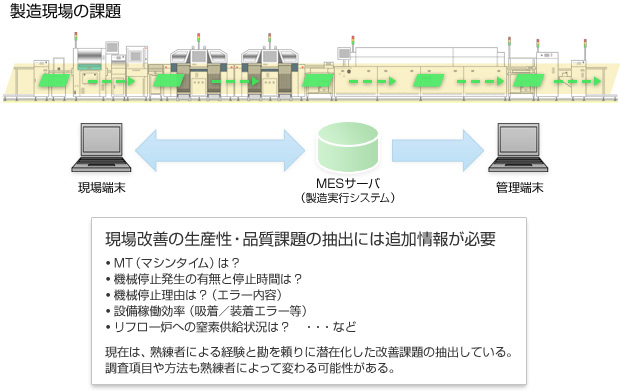
製造現場の稼働状態が見えない。従来は、潜在化した改善課題を熟練者の経験と勘で発掘していた。
上位のMES(製造実行システム)から、30~50以上ある全生産工程の一本一本に対して、オーダ単位で作業指示が出てきます。管理端末では生産開始、終了、異常、メンテなどデータは全部残しています。つまり、ある生産ラインで、あるオーダが何月何日に流れて、どんな条件で流れて、どんな部品を使ったのかなどが全部トレースできているのです。
しかし、これで改善ができるかというと話は別です。実際に機械が動作した時間を調べたり、チョコ停の原因を探ったり、部品の吸着エラーが起きてないかなどを個別に調べなくてはなりません。
これらを現場のベテランが全部調べて、いろんな原因を考えて、その対策や改善を試行錯誤しているのが現状です。しかも改善を続けてきた現場だと改善のネタもなくてってきています。ですから、これからはロット単位でなくて個体単位で改善する必要があり、一段も二段も細かいメッシュで見て行かなければならないのです。
下図は、今回導入したシステムの概略構成です。
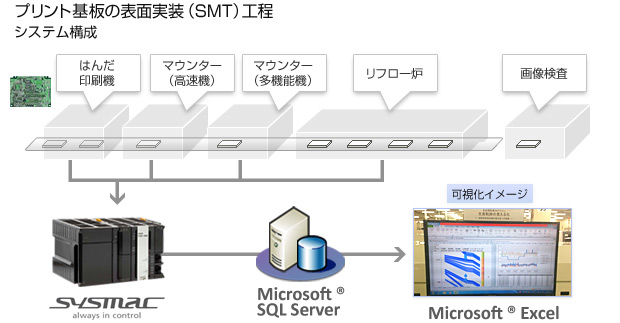
生産設備の色々なセンシング・データやイベントログを、うまく取ってきて、NJコントローラがデータをまとめて、直接データベースに送る仕組みです。
従来はFAコントローラの上位にパソコンを置いて、ログ・ファイルを定期的に作成してデータベースへ送っていました。それが、NJコントローラのデータベース直結モデルであれば、簡単なプログラムを追加するだけで、マイクロソフトのSQLサーバーといったデータベースにダイレクトに書きこむことができます。しかも機械のセンサ・データをダイレクトにミリ秒単位でどんどんデータベースに送ることができるのです。
取り組み内容(見える化~改善サイクル)
生産性の向上
下図プロット画面左側のチャートがタイムラインです。上から下へ時間が流れています。横軸は4つの機械に入った時間、出た時間などがプロットしています。
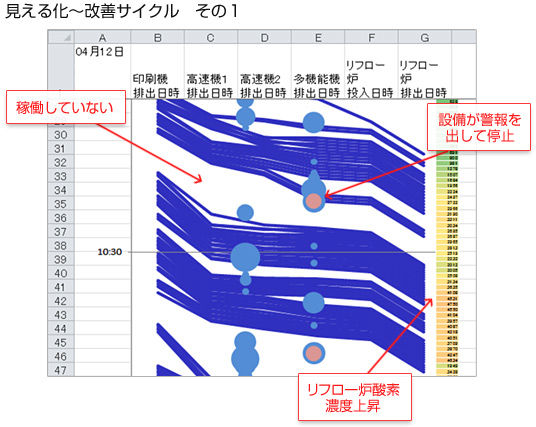
一本一本の線がプリント基板を現しています。線をたどると、何時何分に第1工程に基板が入って、何分後に第2工程、第3工程に移っていくのが分かると思います。
線が浅い角度で密になっているほど加工時間が短いということです。逆に角度が大きいものは加工時間が長くかかったことを意味し、チャートの白いところは無駄な部分と言えます。
線の途中のバブル・チャートは高速機のワーニング(警告)のデータです。青いバブルは機械が止まらなかったワーニング。赤いバブルは止まったワーニングです。バブルの大きさはワーニングの回数を示しています。
機械は動きながらもいろんなワーニングを出しています。部品の吸着ミスなどは、機械が自分でリトライしているため、機械自体は止まりませんが、実際にはロスが起きているのが分かります。例えば、20個以上ある吸着ノズルのノズルNo.15がエラーを何回も出しているから、交換時期だとわかるといった具合です。
この様に、生産性を向上させるための情報が従来よりも細かくわかるようになりました。
品質情報の進歩
チャート図の右端のバーはリフロー炉の酸素濃度の変化を表わしています。はんだがうまくつくように、炉内は窒素を充満させて酸素濃度を下げています。
オレンジから赤になっているところは、管理範囲内にありますが酸素濃度が高いという意味です。検査工程ではんだ不良が出たときに、この個体が流れたときの酸素濃度がちょっと高くなっていたこと、機械トラブルではんだ塗布後に5分も止まっていたことがわかります。ここから、クリームはんだが乾いてしまって部品がうまく載らなかったのではと推測することができます。
さらに、リフロー炉に入る時にプリント基板がずれてなかったかをカメラで撮影して、センサのデータにリンクすることができれば、品質改善のレベルが一段上がって行くでしょう。