- ビッグデータから見える製造現場
オムロン草津工場事例
後編 予防保全/稼働率管理
予防保全の取り組み
次の画面はリフロー炉のヒータ制御電流データのグラフです。リフロー炉内に8か所くらいヒータで加熱するエリアがあります。それぞれ温度設定を変えることで炉全体の温度を調節しています。
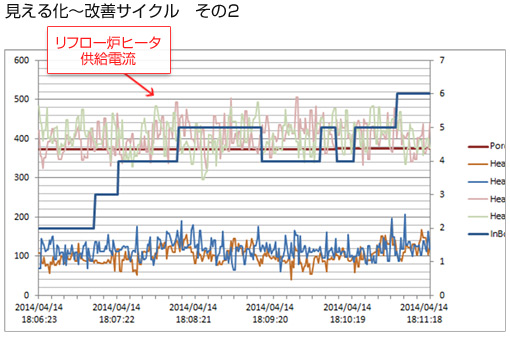
ヒータはご存じの通り消耗品です。「運転時間が耐用期間を経過。交換時期です」などのメッセージが出て交換するのが普通です。この電流値の積算値でみたらヒータ寿命がもっと正確にわかるのではと考えています。
グラフを見ていると、ときどき異常に高い値が出ていることがあります。これはヒータが弱っているため、もっと温度を上げようとして余計に電流を流しているのではと推測できます。
このデータをさっきのNJコントローラが自動でデータベースに貯め込んでいますので、これを保全に役立てられないか分析中です。
導入の成果
- 製造現場の稼働状態と設備の状態を示すパラメータを可視化することで、
製品の流れ(=停滞状況)及び設備の運転状態が見える様になった。 - 改善課題の絞込みが容易で、経験と勘による想定が不要となり、
現場主導での改善のPDCAサイクルを最適化できるようになった。
最初は生産性の向上に使えないかと考えていましたが、いろんなデータを組み合わせれば品質改善にも効くと思うようになりました。そして、もっとデータ貯めたら、設備の予防保全にも使えると感じながら取り組みをしています。
課題の絞り込みに役に立ったり、今までわからなかった別々のトラブルがつながったりと、現場の自分達が主導してPDCAサイクルを回していくことができるようになりました。ちみなに、フロントエンド(分析結果)にはエクセルが使われます。エクセルなら現場の人たちでも触れますから、こういう軽さみたいなのが現場には大事です。
一日のデータからわかること
下図は、あるプリント基板実装ラインの一日のチャート図です。生産現場では設計通りに製品を流すのはすごく難しいです。その日によって機械の調子が良かったり悪かったりして、いろんなことが起きます。それがこのチャート見ると、その日に何があったかもすぐに分かります。
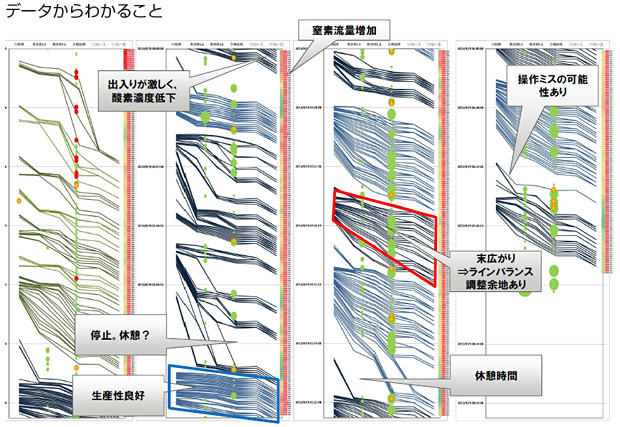
まずチャートのところどころに白い余白に目が行きます。段取り替えを一日に28回も繰り返しているので当然なのですが、場所によっては最終工程に行くと2倍くらいに時間に広がっている部分もあります。
また3工程目にバブルのアラートが多く見られます。これは先ほどお話しした部品のピック・アンド・プレイスを行うノズルでチャックミスが多発していたのでした。
ロットの先頭の一個目を見ると一工程は早いのだけど、2工程から出てくるすごく遅いのがわかると思います。しばらく待ってやっと出てきたていう状態です。これは、一個目で、現場の作業者が確認する作業があるからなのです。ロットの全数を間違えてしまうと大変なので、一個目でちゃんとできているか確認します。熟練者がやるとこんなに時間はかからないのですが、この日のこの時間帯は、熟練してない人がやったのが原因でした。
ラインバランス・ロスという問題もあります。4つの工程のうち、一つ遅い工程があると、必ずその遅い工程に全体が引っ張られます。そのためチョコ停が起きたときは、遅い工程を最初に復旧させる必要があります。
稼働率管理に貢献
生産現場でよく使われる指標に稼働率がありますが、実は稼働率っていう言葉が結構やっかいです。稼働率の分母・分子に何を置くかで数字が変わってしまいます。極端な例だと、電源が入っている時間を分母に置いて、シグナルタワーのグリーンランプが付いている時間を分子にすると稼働率は99%になってしまいます。
本当に付加価値を付けている稼働時間はどのくらいでしょうか。溶接の機械で言えば、溶接を実際に行っている瞬間以外は付加価値を付けていません。ハンドリングしている時間なんか無駄な時間と考えた場合、ある先生によれば、日本の大手自動車会社様でも10%だそうです。それに比べたら、当社は2%から3%ではないかと思います。
同じ稼働率90%といったときに、余白が多い部分の90%と、余白が少ないけどアラートが出ている部分の90%では数字は一緒でも意味がまったく違います。チャートでビジュアル化できたことで、数字ではなくて視覚で、何が悪いか、何をしなくてはいけないかが一目で分かるようになりました。この効果は非常に大きいと感じています。
今後の取組み(ノンストップ未然防止)
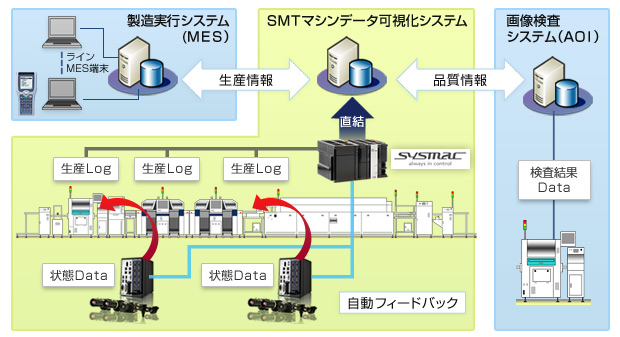
- 既存QCDデータに、ビッグ(マシン)データを個体連動させ
改善すべき要因をマシンパラメータレベルで見つける。 - 自動フィードバックによるノンストップ不良未然防止ラインを構築し、展開する。
前述したようにカメラでの状態監視を考えています。製品の出来上がり検査ではなく工程毎に加工状態を検査する仕組みです。例えば、加工状態を見ながら自動フィードバックを行い、印刷のスピードや圧力を変えたり、設備が故障しそうな場合は事前にフラグを挙げたり。そんなラインを止めないで不良を未然に防いでくれるノンストップのラインがこれからの取組みです。
まとめ
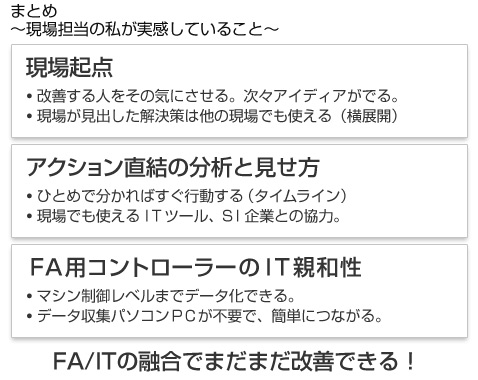
ビッグデータ分析を導入するメリットは次の3点です。
まず現場起点。現場で改善する人をその気にさせることが大事です。現場が見つけだした解決策は、他の現場でも少し変えてあげれば使えます。
次にアクション直結の分析と見える化。課題が一目でわかれば必ず現場の人は必ず行動します。現場でも使えるExcelのようなITツールを使うのがポイントです。
そして、FAコントローラのIT親和性。工場の人間はPLCなどのコントローラ使えますが、データベースに書き込むSQL文はなじみがありません。そんな私でも使えるというメリットは大きいです。
マシン制御レベルにおいてミリ秒単位でセンサのデータを全部残すことができるようになりました。将来的には、不良品のデータしか残せなかった画像データも、各個体の加工条件と一緒に残すことがNJコントローラであればできるとこまで来ているのです。FAとITが融合すれば現場の改善はまだまだ期待できるでしょう。
(この記事はオムロン株式会社 草津工場 製造部製造1課・水野伸二が2014年7月に「富士通フォーラム2014大阪」にて講演した内容の要旨です。記載された内容は当時のものです。)
ビッグデータ活用の現場を見学しませんか?
オムロン草津工場及びオートメーションセンタでは、随時見学を受け付けています。
見学の申込みに関しては、当社販売員までお問い合わせください。
最寄りの支店・営業所はオムロン営業拠点一覧をご覧ください。
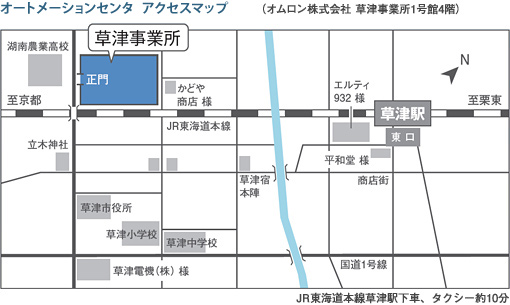
所在地
〒525-0035 滋賀県草津市西草津2-2-1
交通アクセス
JR東海道本線 草津駅より南へ800m(徒歩約15分 車で約10分)
※来客者用駐車場は台数に限りがあります。できるだけ公共交通機関をご利用ください。