オムロンのデバイス&モジュールソリューションズカンパニーに属するオムロンオートモーティブエレクトロニクスイタリア(以下、A.E.I.)は、イタリアおよび欧州におけるオムロンの唯一の自動車部品製造拠点です。車載用リレーとモジュールの製造に特化するA.E.I.の事業は、設計、製品開発、樹脂・金属製部品から最終製品までの製造、加工用機械(組立・試験)の設計・自動化、販売、カスタマーサービス、倉庫保管、物流など様々な分野に及びます。A.E.I.は、2004年にイタリアのアラトリに拠点を設立し、2018年にフロジノーネに移転しました。従業員は約150名で、欧州と北アフリカの主要自動車メーカー向けに部品を製造しています。
動画でみる オムロンオートモーティブエレクトロニクスイタリアのデータ活用事例
課題
不良ゼロへ、データ分析を活用したリアルタイムでの品質管理の実現
自動車業界の高い品質標準を満たすには、生産効率とプロセス再現性に、より重点を置いて部品生産に適した技術を選択する必要があります。欠陥率を100万分の1(ppm)から10億分の1(ppb)に抑えるよう、自動車メーカーからの要求は年々高まってきています。
これに対応していくためには、品質管理の方法を、サンプリングから100%保証(全数検査)に切り替える必要があります。各工程で100%保証を行うには各機械からすべてのデータを収集しなければなりません。全世界の自動車市場向けに年間約3000万個の部品を製造するA.E.I.は、その製造戦略を改め、重要工程で発生する欠陥をスマートに、そしてリアルタイムに管理していくためにデータ分析の活用が課題でした。
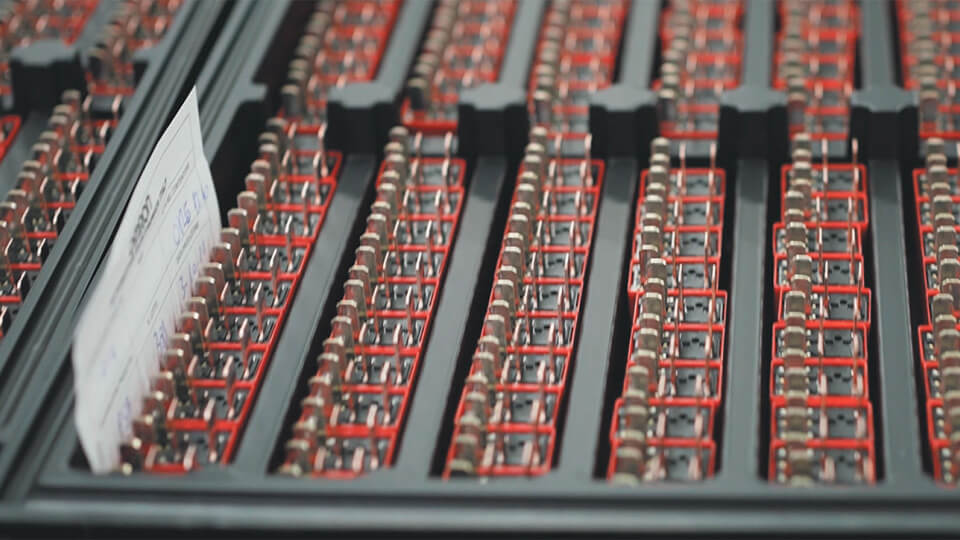
解決策
リアルタイム分析で、オペレーターの主観に左右されない新しい品質管理モデルを構築
戦略的な工程見直しの第一歩は、パワーリレー生産ラインの改良で、オムロンの制御機器事業部が提供する、機械上のデータの取得・処理に関するすべてに対応する「現場データ活用サービス i-BELT」による取り組みでした。
かしめ力のリアルタイム測定
A.E.I.がリレー生産ラインの改良を決定するに至った主な目的は、バッチに欠陥品が発生しその結果として経済的損失や顧客に欠陥部品が届くリスクを高める非効率性を取り除くことです。「i-BELT」のデータサービスチームによる支援のもと、A.E.I.は、プロセスの最終段階で検査を行うオペレーターの主観的な判断に左右されない、新しい品質管理モデルを開発しました。このモデルはAIシステムによるリアルタイム分析に基づくもので、人的ミスや欠陥品が顧客へ届くリスクを排除します。
リレー生産ラインの改良に参加したエンジニアは、リレーを構成する樹脂製部品と金属製部品の機械的接合、つまり「かしめ」に注目しました。かしめは組立工程において最も重要な作業であり、また欠陥品が顧客に届く原因となることが最も多い作業です。これまで、細心の注意が必要なこのかしめ作業の品質検査はオペレータが行っており、管理計画書に示される統計データに基づいて目視点検を行い、部品が規定の形状であるかを検証していました。
しかし、欠陥が確認された場合、欠陥部品だけを回収するのではなく、製造バッチごと隔離し、2度目の検査を行います。検査には費用と時間がかかる上に、製造バッチが廃棄される場合がほとんどです。そのため、A.E.I.はかしめ力をリアルタイムで測定できる、新しい管理システムを考案しました。
この管理システムは、既存の工程にAIコントローラ(NYシリーズ)とコンポーネントを組み込み、ラインに取り付けた力覚センサと連動させることで実現しました。この改良によって、しきい値を設定し接合不良の発生時に工程を即時に停止させることに成功しました。その結果、オペレーターがすばやく工程に必要な対策を講じることができるようになり、A.E.I.は100%のクオリティゲートを達成しました。
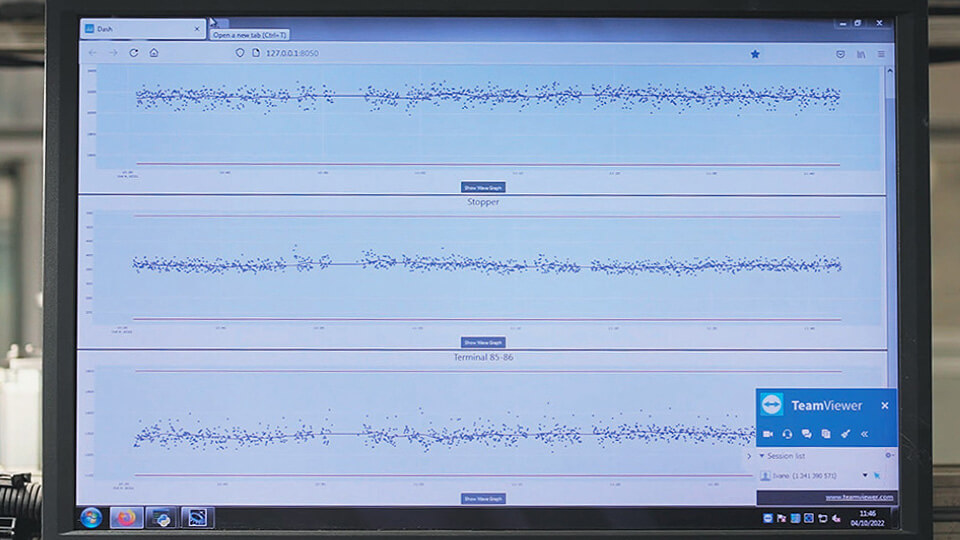
データ主導の工程
A.E.I.の目標は、「i-BELT」により、オムロンのAIコントローラ(NYシリーズ)を工程に組み込んで品質基準のしきい値を満たし、製造過程のデータを保存して部品の生産履歴を管理することでした。
準備段階で設定した目標の達成には、データ分析が不可欠であることが分かりました。オランダに拠点を置く「i-BELT」のデータサービスのチームは、各センサからすべてのデータをリモートで収集しました。センサには既に機械に取り付けられているものと、重要な製造工程を監視する目的で取り付けられたものがあり、かしめ部分の先端にある、接合部に加わる力の測定に必要な力覚センサも含まれていました。A.E.I.は、AIコントローラにロードセルを接続することでリアルタイムでかしめ力の様々な時間的な変化を検出し、100%のクオリティゲートを確保できる力のレベルや数値を判断できるようになりました。AIコントローラの最大の利点の一つは、機械と同期してデータをミリ秒の精度で取得できることです。これは、AIコントローラが異常を高い精度で検出し、直ちにフィードバックできることを意味します。この結果、製造工程を細部まで把握することが可能となりました。
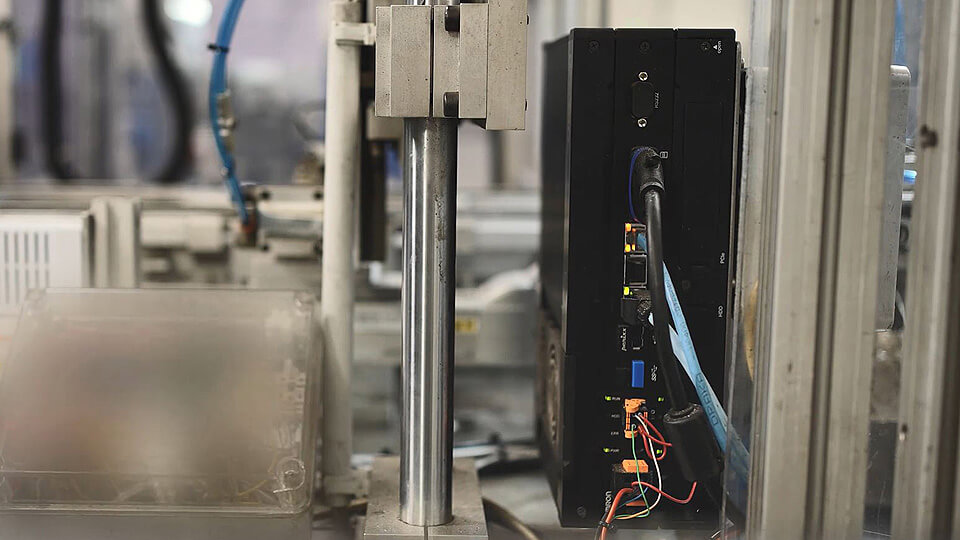
成果
組立部品に対する100%のクオリティゲートを達成。
ムダや追加検査へのコストを削減しながら、1年で投資資金の回収に成功
品質管理による経費削減
「i-BELT」が提供するインダストリー4.0やAI技術を、工程の監視、分析、検証、妥当性の確認に使用し、A.E.I.は評価フェーズにおける目標を全て達成しました。特に、自動車業界では必須である、組立部品に対して100%のクオリティゲートを達成しました。また、A.E.I.における追加のバッチ検査や廃品に関わるすべての費用を削減し、12ヵ月以内の投資回収も果たしました。
さらにビッグデータに関しては、A.E.I.はすべての測定値をデータベース内に保管し、いつでも再処理できるようになりました。今後、A.E.I.では同様の工程で製造する他の製品に対しても同じ方法を展開していく予定です。
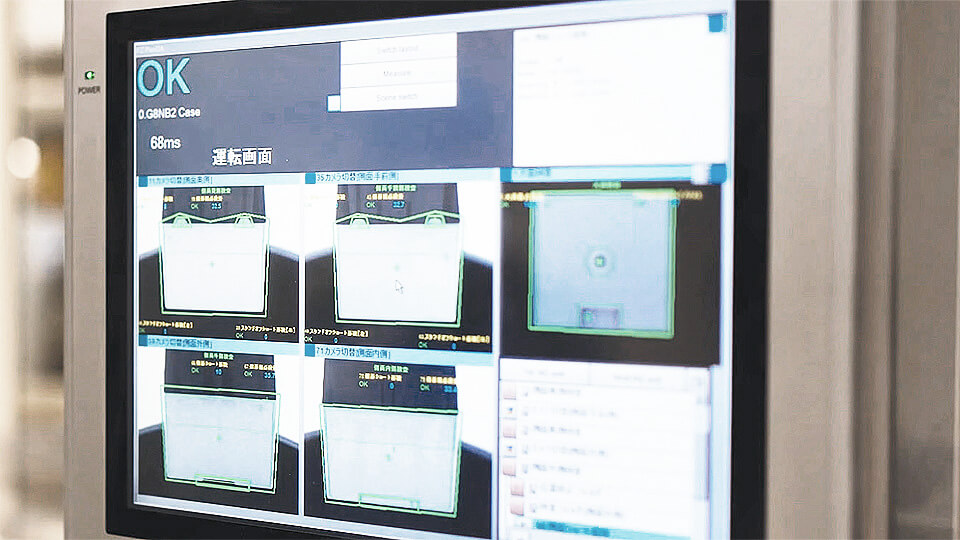
サステナブルな製造で、エネルギーのムダを削減
今回の改善により、エネルギー消費(電気、水、ガス)の削減、労働時間の短縮、廃棄部品や貴金属(銅、銀、真鍮)の利用など、持続的な利益も生まれます。
これらの結果はオムロンのグリーンなビジョンを実現し、新しいハードウェア設備に多額な投資を行うのではなく、データ分析に重点を置くことで製造工程の改善を目指す企業にとってのよい例となるでしょう。
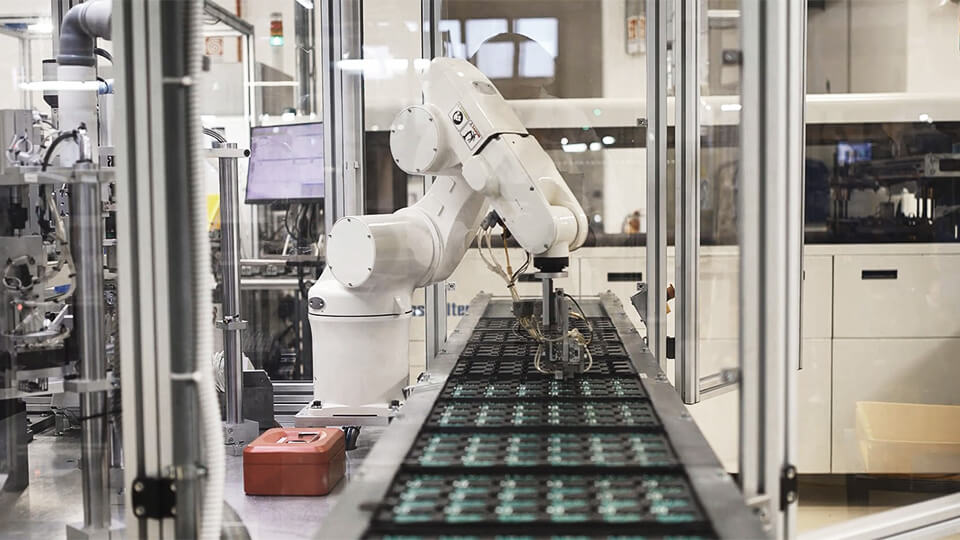
担当者の声
機械の状態の正確な把握で、
不良発生時の適切な対策が見つかるように
今回、工程内にAIコントローラを導入し、新しい品質管理モデルを構築したことで、機械内で何が起こっているかを正確に把握することができるようになりました。医者が患者を診察するように、コントローラによってかしめ力の様々な時間的な変化を検出し、不良発生時の問題解決に必要な対策を見つけることが可能になりました。
また、今回の改良では、経済的メリットとして1年で投資コストを回収できた点が挙げられます。加えて、エネルギーの無駄な消費を回避でき、グリーンな取り組みという観点からも利益をもたらし、オムロンの企業ビジョンを実現します。
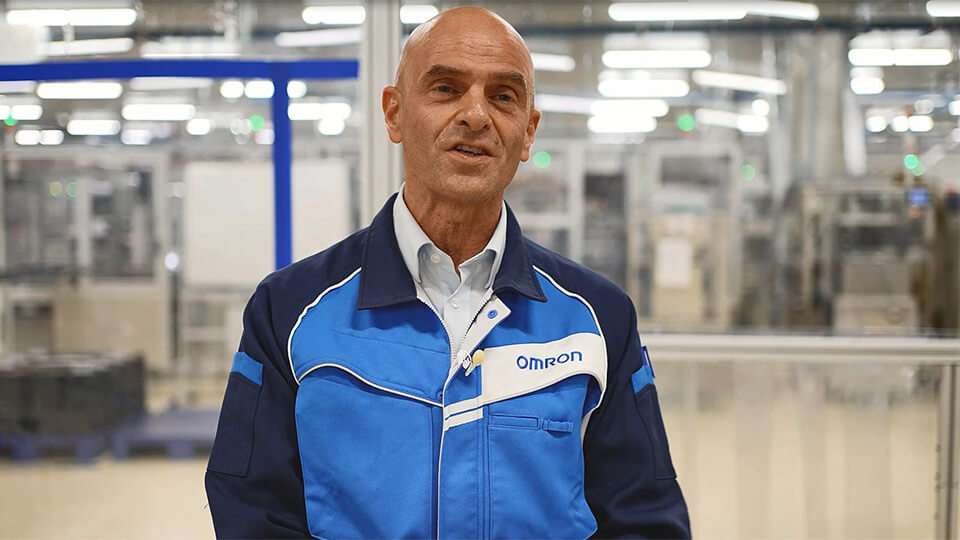
エンジニア兼ITマネージャー IVANO ADIUTORI
データ活用による改善で新設備の投資コストを削減。他の製品へも展開していきたい
自動車メーカーからの要求は年々高まっており、品質に関する要求は特に厳しいものと言えます。今回データ活用により、新しい機械に投資することなく品質管理の方法を改善でき、機械入れ替えのための設備投資が不要になりました。これは、データ分析に重点を置くことで製造工程の改善を目指す企業にとって、よい例となるでしょう。
今後は、同様の工程で製造する他の製品に対しても同じ方法を展開していく予定です。
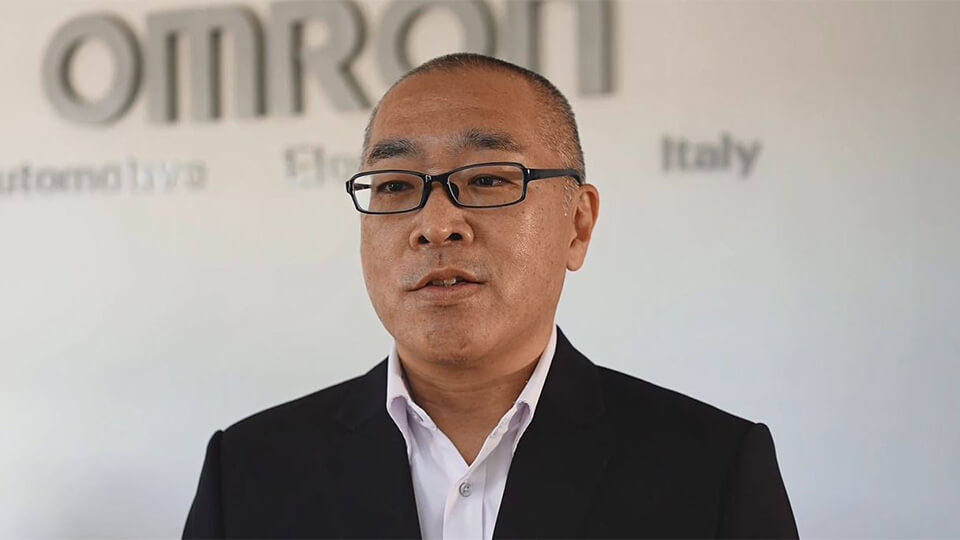
社長 大東 博之
導入ソリューション
「現場データ活用サービス i-BELT」
オムロンの幅広い製品ラインナップ、自社生産現場のノウハウやデバイスパートナー様のノウハウを集結した、「現場データ活用サービス i-BELT」。
お客様の現状課題共有から、どのデータに着目すべきかを検証し、データを収集・見える化します。
蓄積されたデータを独自のノウハウで分析し、得られた分析結果を制御アルゴリズムに変えて現場を最適化。システム導入後も、お客様と共に継続的にデータ活用し、経営と現場が一体となった課題解決への挑戦に貢献します。
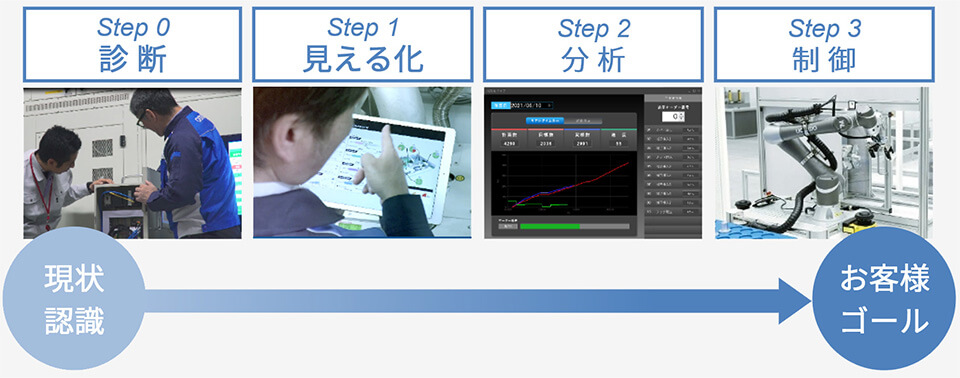