IoTやAIの進化で、製造現場におけるデータ活用に関心が高まっています。
草津工場の金型加工では、多品種少量生産の効率化が求められる一方で、加工条件の設定をしている熟練者不足という課題がありました。
これらの背景から、データ活用により、従来、作業者の五感で判断していた小径工具の加工条件設定の最適化を行うことに取り組みました。
課題
「もっと加工速度を上げられないか」
多品種少量生産が当たり前となる中での生産性向上
オムロンの制御関連製品は20万種を超えており、使われる環境や顧客によって仕様が全て変わるので、多品種少量生産の効率化が求められます。金型製造についても同様のことが求められていましたが、ワークの送り速度を上げるなど、加工条件を厳しくしすぎると、工具の折損によって機械が破損し、ダウンタイムにつながります。そのため、最適な加工条件の設定が難しく、熟練技術者の経験や勘が不可欠でしたが、近年の人手不足に伴い、技術者がなかなか育たないという課題もありました。
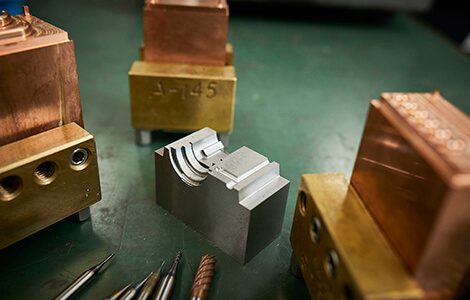
解決策
切削加工を行うマシニングセンタでのデータ活用に挑戦
マシニングセンタ*に振動センサを取り付け、データをマシンオートメーションコントローラに取り込むことで、熟練技術者の“匠の技”の数値化し、データ活用による制御の自動化に挑戦しました。現場での試行錯誤を繰り返し、振動データの特徴量を分析、結果を制御にフィードバックすることで加工条件を最適化するという仕組みを構築することができました。
*マシニングセンタ:金具等の金属部品を加工する工作機械
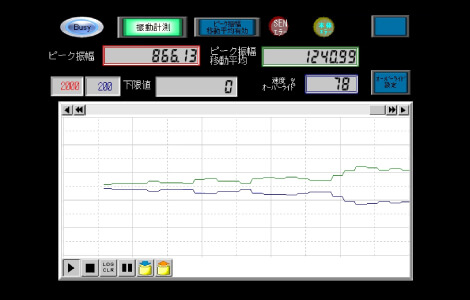
成果
加工時間40%削減、工具の寿命は2倍
今回のシステムを導入することで、ワークの送り速度を工具メーカ推奨値の3~5倍まで引き上げることができました。これにより、加工時間は従来比40%も短縮*。また、工具の状況を常に把握でき、故障予知ができるようになったため、摩耗量は20%削減、工具寿命を約2倍に伸ばすことができました。
*当社装置における銅の切削の場合
取り組みポイント
Point.1
課題の共有生産性を上げるには送り速度を高めるなど加工条件を厳しくしなければなりません。その一方で、金型製造は微細加工が必要で、使用する工具も最小0.2mm径と小径のものが多く、余裕を持たせないと工具が折損しダウンタイムにつながってしまいます。そのため、最適な加工条件の設定が難しく、熟練技術者による経験と勘で加工速度を追求し続けていました。
しかし、人手不足や技能承継の課題もあり、最適な加工条件を限界まで追求するべく、熟練技術者の技能を効率的に再現する新たな仕組みが必要な状況でした。
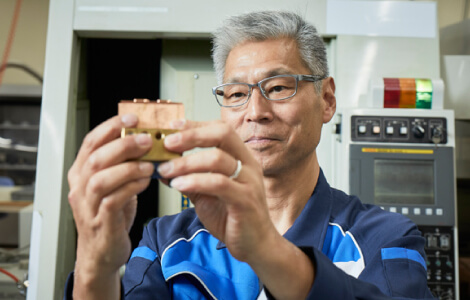
Point.2
データの収集金型開発メンバは、“匠の技”の数値化に挑戦。マシニングセンタの心臓部ともいえる切削加工が行われるすぐ側に、微小な加工抵抗を見える化する振動センサを設置しました。加工する金型を固定する治具から直接振動データを取ることで正確なデータが取得できるようになりました。
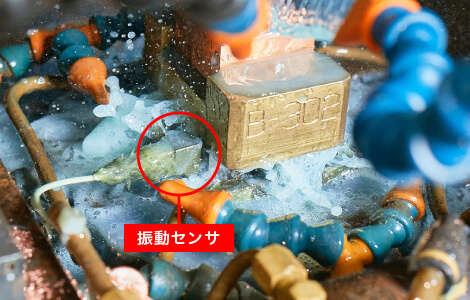
Point.3
見える化・分析振動データをマシンオートメーションコントローラ(NJシリーズ)に取り込み、加工抵抗値のしきい値や最適な加工条件の設定といった、加工における“いい状態”と“そうじゃない状態”を、振動の値をもとに1つ1つ定義しました。また、継続的にデータ分析することで制御へつながるヒントを見出しました。
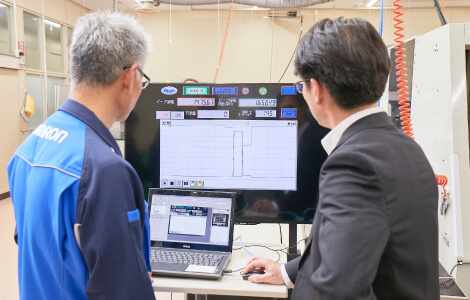
Point.4
最適な自動制御振動センサからリアルタイムにデータを取得し、制御プログラムを定期的に更新。最適な送り速度を自動で制御し続けることで、加工時間40%削減という飛躍的な生産性向上を実現しました。
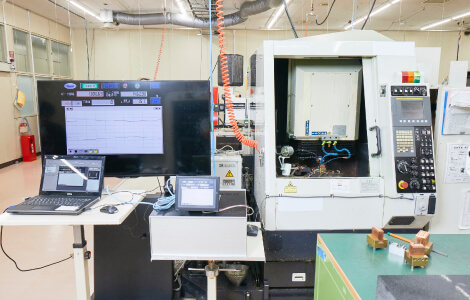
担当者の声
やっと、永遠の課題を解決することができました
もともと工具メーカ推奨値の1.3倍まで送り速度を引き上げて加工していましたが、今回のシステムを用いることで3~5倍まで高めることができました。ここまで送り速度を上げられるとは、思ってもいませんでした。やっと、経験と勘ではなくデータを活用することで、加工速度を上げるという、永遠の課題を解決することができました。上司から、1.3倍で限界と言っていたのはウソだったのかと、チクリと言われたことも余談として紹介しておきます。
今後は、切削加工以外の加工方法にもアプリケーションのバリエーションを増やしていく他、センサ数を増やした場合どんな相関が取れるかという点など、実証のパターンを広げていきたいです。
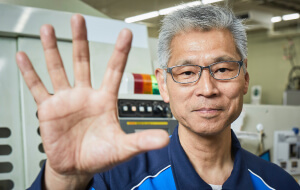
金型・材料センタ 金型開発課
技術士 山崎 雄司
加工機やプレス機にも展開し、現場の進化に貢献したい
もっとも苦労したところは、テスト計測時の工具の直径0.5mmのもので切削する状態をセンシングするところです。このような繊細な加工の状態は、マシニングセンタの強力なモータに何の影響も与えないので、トルク変動を計測するという方法が使えず、何でセンシングするかを探す作業に時間がかかりました。振動と加工状態の相関がわかったときは思わず拍手をしていました。
現在、世の中で使用されている加工機はすでに完成されており、改善の余地がないと考えていたのですが、今回の事例のように加工状態をセンシングし、アルゴリズムを組み合わせることで現場の課題解決できることがいっぱいあると改めて思いました。
加工機やプレス機などにもこの考えを適用し、現場の進化に貢献したいと考えています。
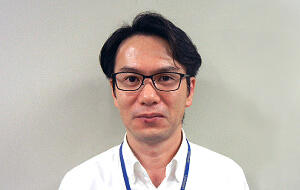
営業本部 オートメーションセンタ
竹下 勝治
導入ソリューション
「現場データ活用サービス i-BELT」
オムロンの幅広い製品ラインナップ、自社生産現場のノウハウやデバイスパートナー様のノウハウを集結した、「現場データ活用サービス i-BELT」。
お客様の現状課題共有から、どのデータに着目すべきかを検証し、データを収集・見える化します。
蓄積されたデータを独自のノウハウで分析し、得られた分析結果を制御アルゴリズムに変えて現場を最適化。システム導入後も、お客様と共に継続的にデータ活用し、経営と現場が一体となった課題解決への挑戦に貢献します。
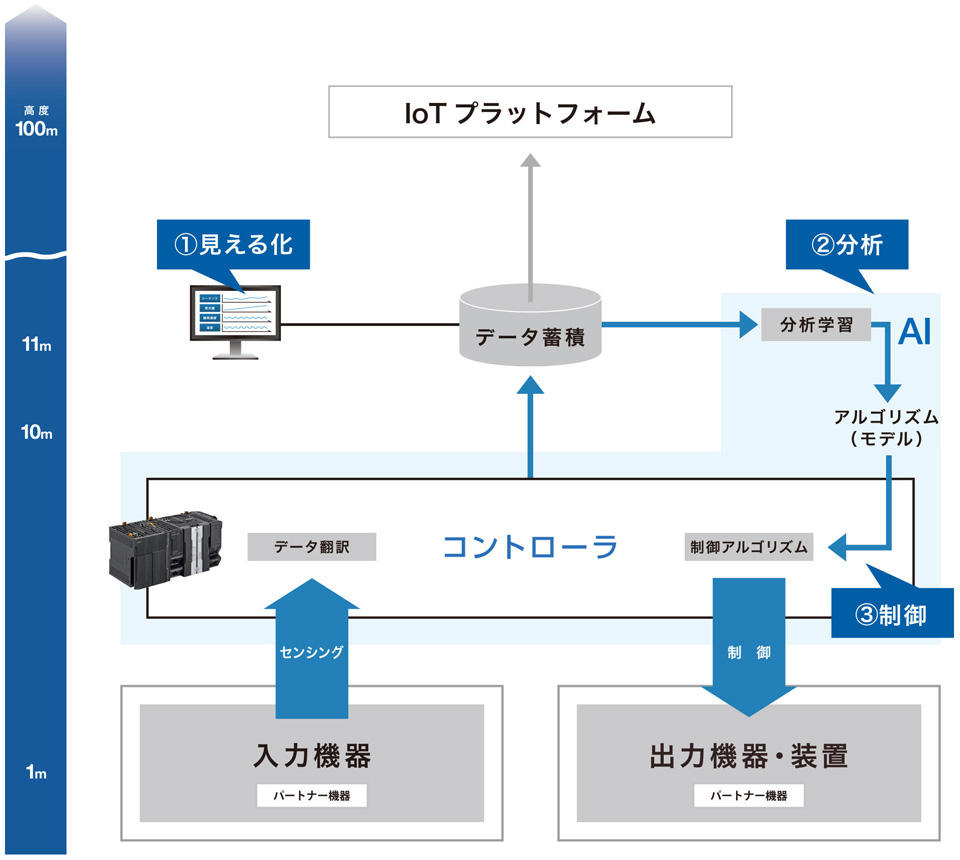