オムロン野洲工場の半導体生産ラインでは、半導体・MEMSセンサ*製品のコスト競争力を維持しながら新たな機能をもつ製品を次々と生みだすために、既存の設備をフル活用することで多品種少量生産を実現してきました。これらの背景から、できる限り投資を抑えながら、設備の老朽化で増加する突発故障を未然に防ぐ取り組みにチャレンジしました。従来は熟練保全員による定期診断と早めの定期メンテナンスで決定していた真空ポンプのメンテナンス時期を、データを活用することで故障の予兆をとらえ、最適なタイミングでのメンテナンス実現に取り組みました。
きっかけは「現場データ活用サービス i-BELT」の診断を受けたこと。“製品廃棄につながる設備の突発故障は避けたいが、投資は最小限にしたい”、そんな願いが、現場ノウハウとセンシングによるデータ化、振動解析技術により実現しました。
*MEMS:Micro Electro Mechanical Systems 半導体のシリコン基板・ガラス基板などに、機械要素部品のセンサ・アクチュエータ・電子回路などを集積したミクロンレベル構造を持つデバイスで、「マイクロマシン」とも呼ばれる
課題
装置保守は“定期的”から“必要な時”へ。
熟練保全員の減少する中、CBM*によるメンテナンス時期の最適化実現
同系機種の大量生産から多品種少量生産への移行が進み、過去に設定したメンテナンス周期が最適とは言えなくなっていました。また装置の異常をとらえるスキルを持った熟練保全員が減少する中で、過剰なメンテナンスによるコストの無駄と突発故障リスクは増していきます。これらに対し、データを活用して故障予兆を捉え、最適なタイミングでメンテナンスを実施するCBM化の実現が課題でした。
*CBM:Condition Based Maintenance 必要と判断した時のみメンテナンスを実施すること
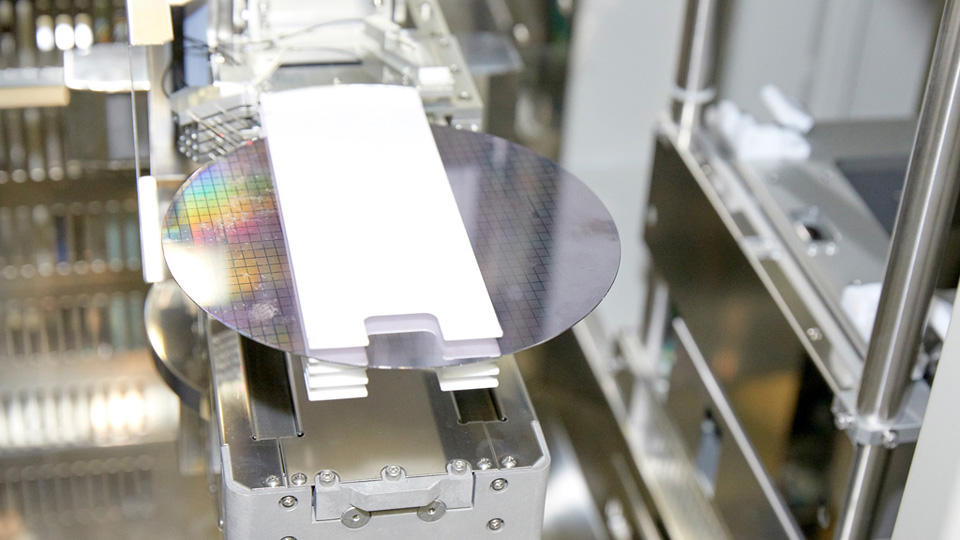
解決策
振動データ活用による真空ポンプのCBM化
半導体の生産ラインで多用されている成膜装置の真空ポンプは、反応性ガスが流入し生成物が増えていくことで突発的に停止し、多数のウエハーが廃棄となるリスクがあるため、メンテナンス頻度を上げています。そのため、成膜装置用真空ポンプは、CBM化が成功すれば効果が高いと考え、振動センサを取付けることにより、振動データの常時監視を開始しました。振動センサからのデータと振動解析技術を使い、いくつもの特徴量にリアルタイムで変換・監視します。センサの取り付け位置の最適化、有効な特徴量の抽出、しきい値設定の最適化が成功の鍵となります。熟練保全員の知見とオムロンの振動解析機器・技術を組み合わせ、機器固有の個体差を微調整し、確実性を高めていく取り組みをしました。
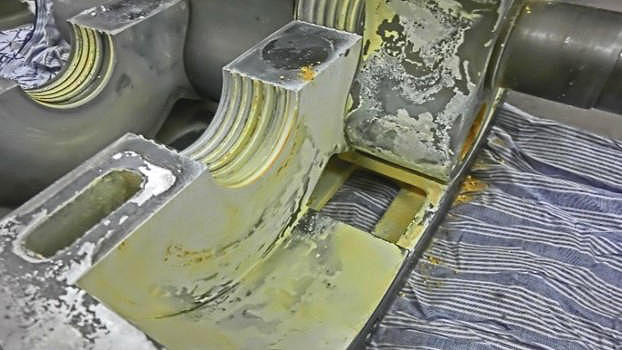
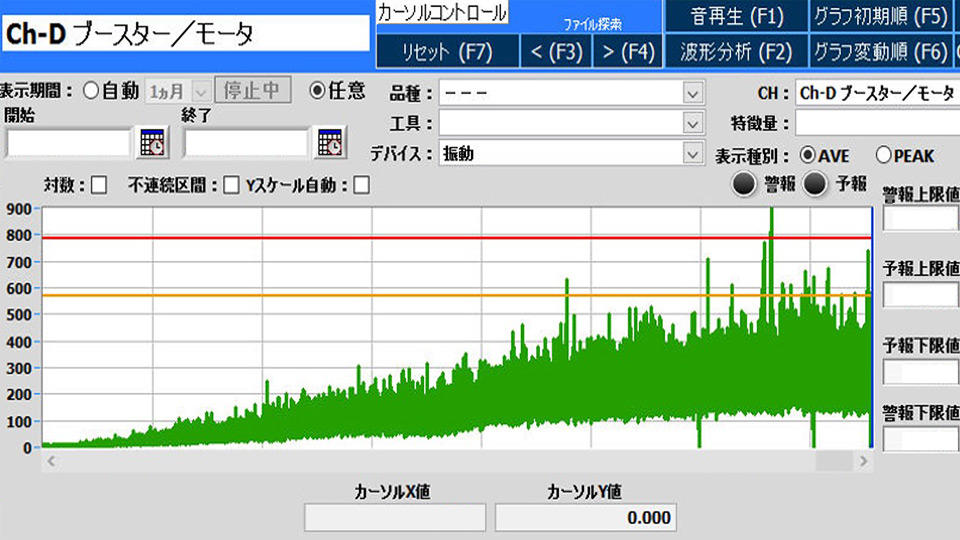
成果
突発故障の発生ゼロ、メンテナンスコスト15%削減
振動データからの予知により、真空ポンプのメンテナンス周期を30%以上延長することに成功しました。突発故障を起こさずメンテナンス周期を延ばすことで、オーバーホールの費用が抑制できるため、メンテナンスコストとしても15%以上の削減効果を得ることができました。リスク低減とコスト削減を両立させ、装置保全部門の長年の夢であったCBM化の完全実現に向け、大きく前進することができました。
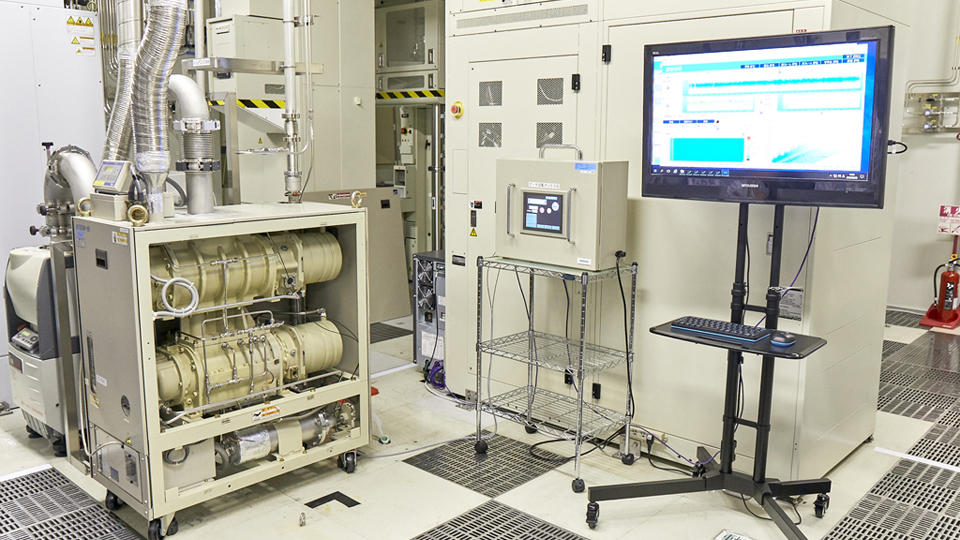
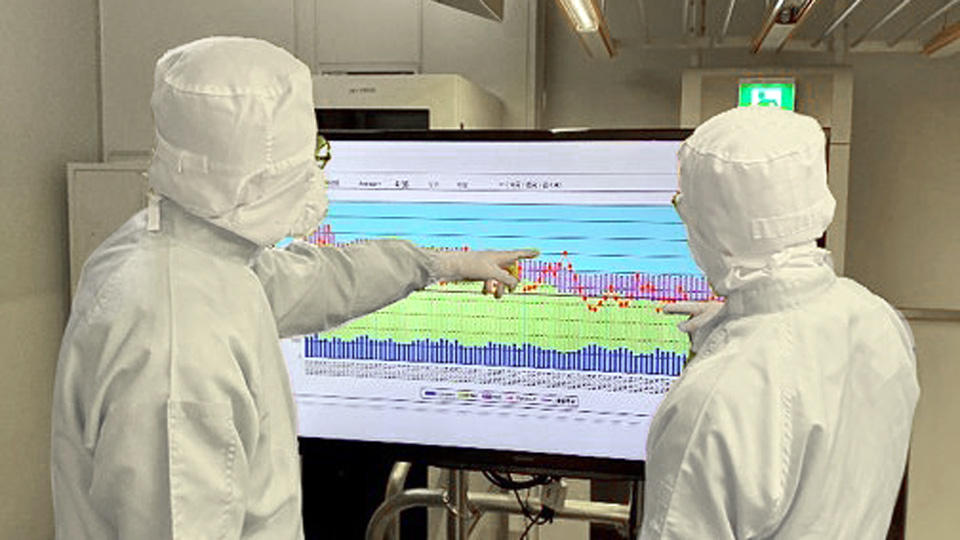
取り組みポイント
Point.1
現場課題の洗い出しと取り組み箇所の決定CBM化は保全分野の理想ですがなかなか実用化には至らず、これまで経験に基づいた熟練保全員の判断に任せ、装置の間欠的な監視や定期メンテナンスで対応してきました。
しかし、生産量の変動や品種の変化により、最適なメンテナンス時期も大きく変動し、メンテナンス周期の最適化と突発故障リスクのバランスが取りづらくなります。加えて、熟練保全員も減少していることが大きな問題となり、メンテナンス時期を最適化するCBM化の実現が急務となりました。
中でも、突発停止によるウエハー廃棄のリスクが高い成膜装置用真空ポンプは、メンテナンス頻度を上げているため、CBM化が成功すれば効果が高いと考えました。

Point.2
データの収集聴診棒をご存知でしょうか?熟練保全員は聴診棒を使って音を聴くことで、ポンプの中の堆積物による振動の変化を聞き分けることができます。この技をデジタル化し、確度の高い判定アルゴリズムを確立できれば、CBM化が実現できます。こうして、匠の技をもとに振動センサの取り付け位置・方法を決定し、データの収集を開始しました。
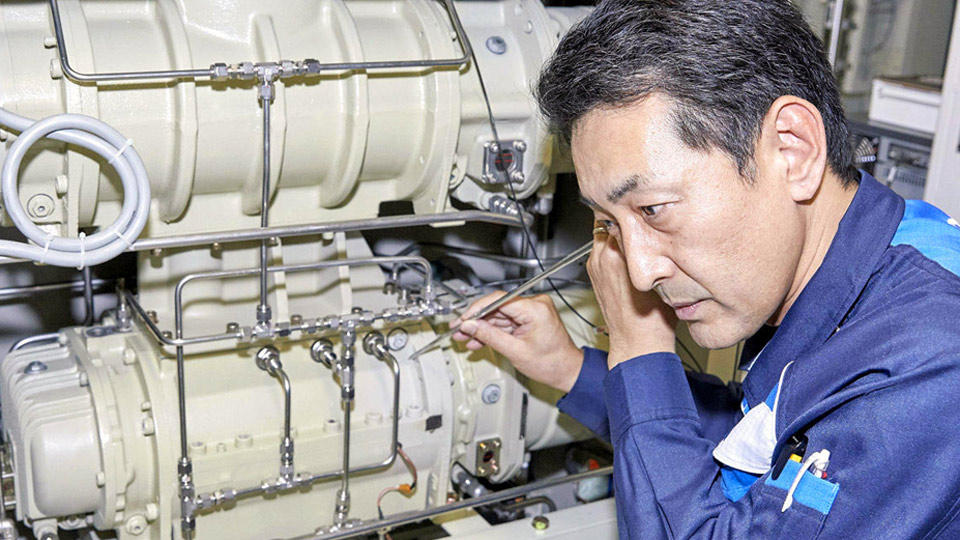
Point.3
見える化・分析真空ポンプの振動データをリアルタイムで解析して様々な特徴量に変換し、見える化しました。実験的に稼働期間の異なるポンプでデータを取得・分析することで、監視に使える特徴量の特定を行いました。センサ取り付けの最適な位置・方法の調整を行い、より確実に変化を捉えることを目指しました。
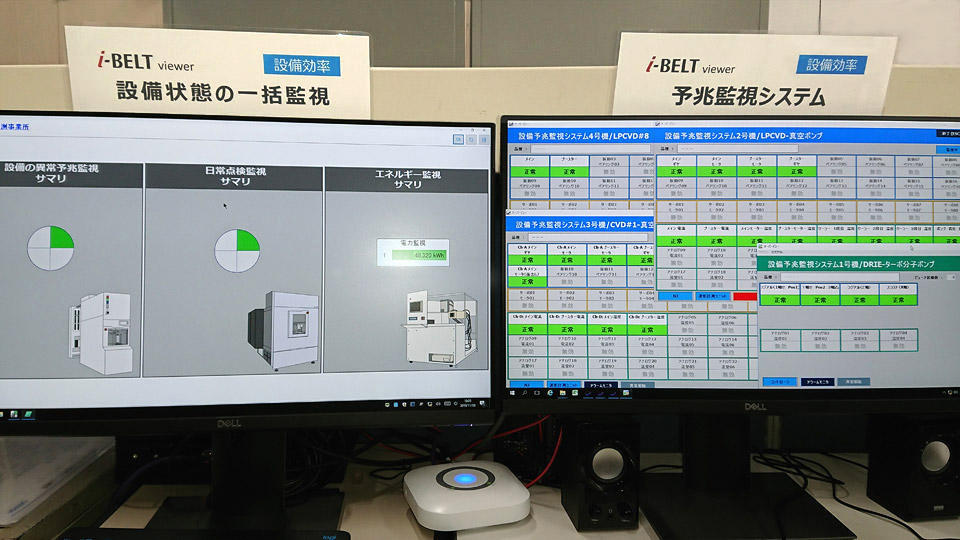
Point.4
完全CBM化を目指した取り組み完全CBM化に向け、まず監視しながらのメンテナンス間隔30%延長を実施しました。ここで得られたデータの解析から、より確度の高い予兆を技術者と現場が共創しています。
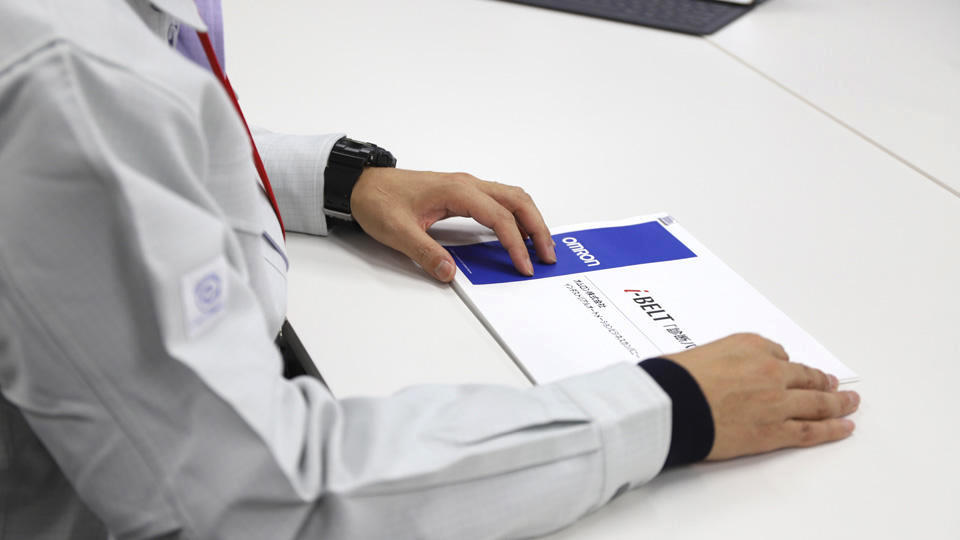
担当者の声
CBM化は長年の夢でした
とくに半導体は装置産業と言われるように、野洲工場のような比較的小規模な工場でも真空ポンプだけで200台以上あり、これらが突発停止すると、大量の製品廃棄につながるものも多数あります。突発故障を避けるためにメンテナンス間隔を短くすると、メンテナンスの費用も手間もかかります。
また、最近は製品の種類や量の変動が激しく以前設定したメンテナンス時期では長すぎて突発故障を起こす事態も発生しています。今後も振動に限らず、各種センサからのデータを活用し、CBM化の技術を高めていきたいと考えています。
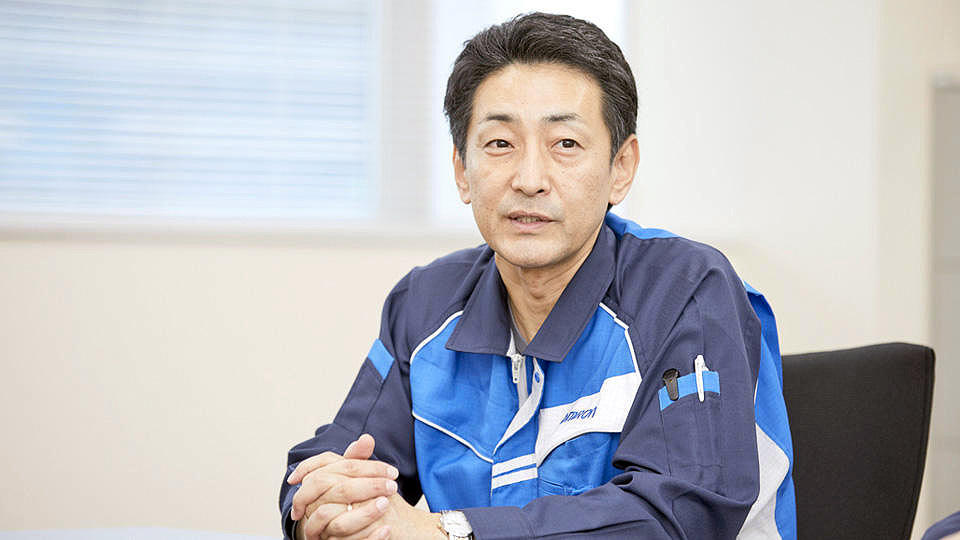
生産部 生産1課
特級機械保全技能士 後藤 則和
これまで積み上げた装置保全の知識と経験と技術を“見える化”し、継承したい
オムロンには20年以上に渡る保全記録の蓄積と、保全を実行してきたメンバの貴重な知識、経験、保全技術があります。これらを失うことは当社のみでなく半導体業界にとっても大きな損失だと思います。
今回、振動・真空ポンプからCBM化のシステムを構築しました。このシステムに他の装置ごとに持っているメンテナンス情報を蓄積し、デジタル化・見える化を自部門で取り組んでいます。継承すべき技術として「現場データ活用サービス i-BELT」というサービスを通じてお客様にも展開されることを願っています。
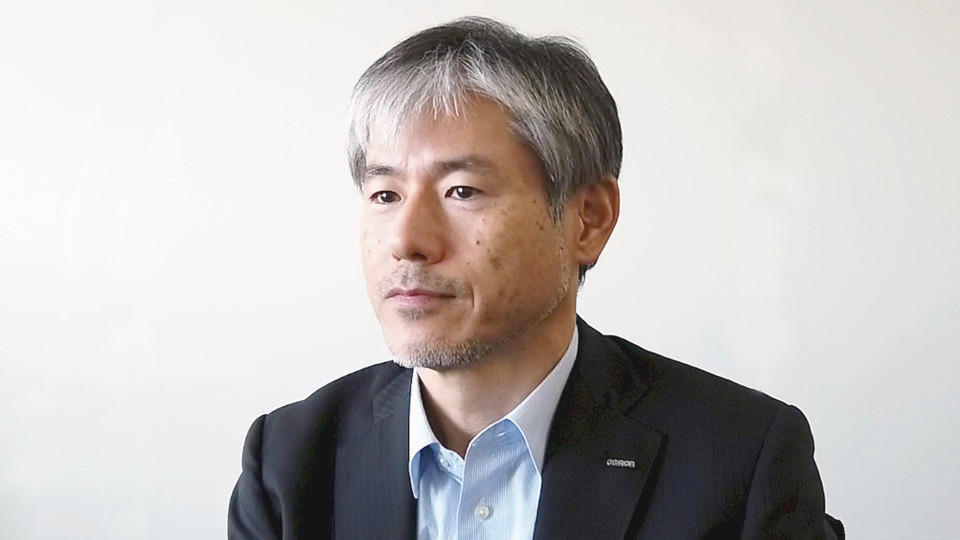
生産部 生産1課
課長 中村 智史
導入ソリューション
「現場データ活用サービス i-BELT」
オムロンの幅広い製品ラインナップ、自社生産現場のノウハウやデバイスパートナー様のノウハウを集結した、「現場データ活用サービス i-BELT」。
お客様の現状課題共有から、どのデータに着目すべきかを検証し、データを収集・見える化します。
蓄積されたデータを独自のノウハウで分析し、得られた分析結果を制御アルゴリズムに変えて現場を最適化。システム導入後も、お客様と共に継続的にデータ活用し、経営と現場が一体となった課題解決への挑戦に貢献します。
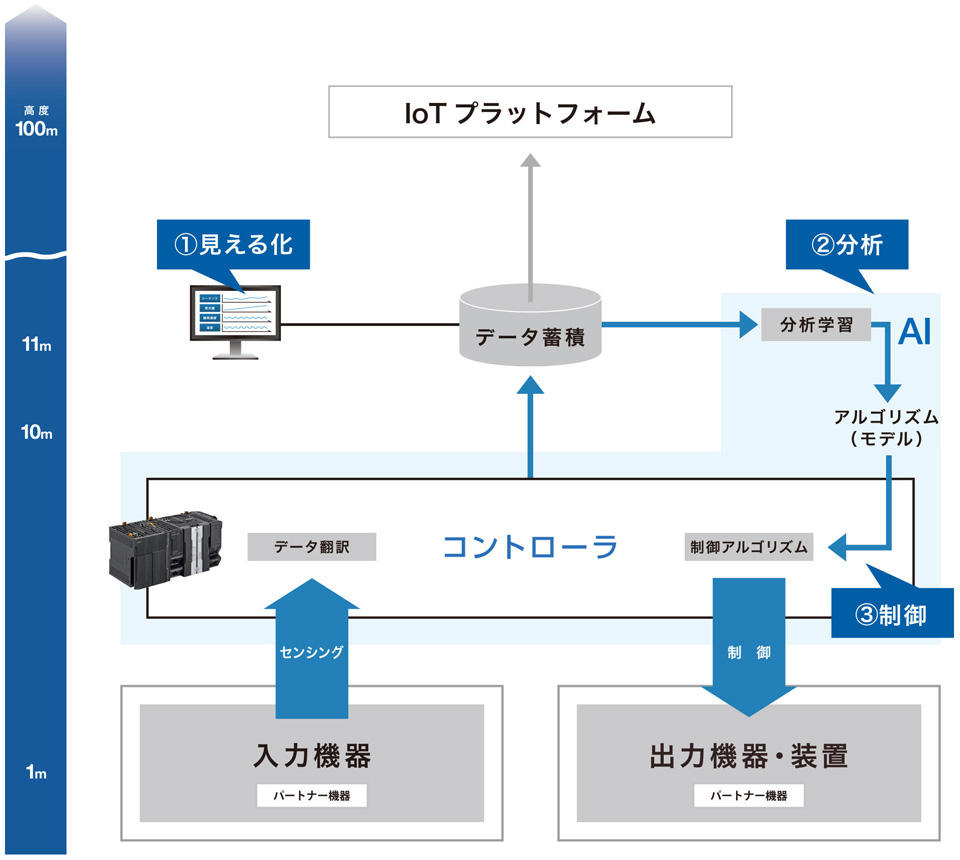