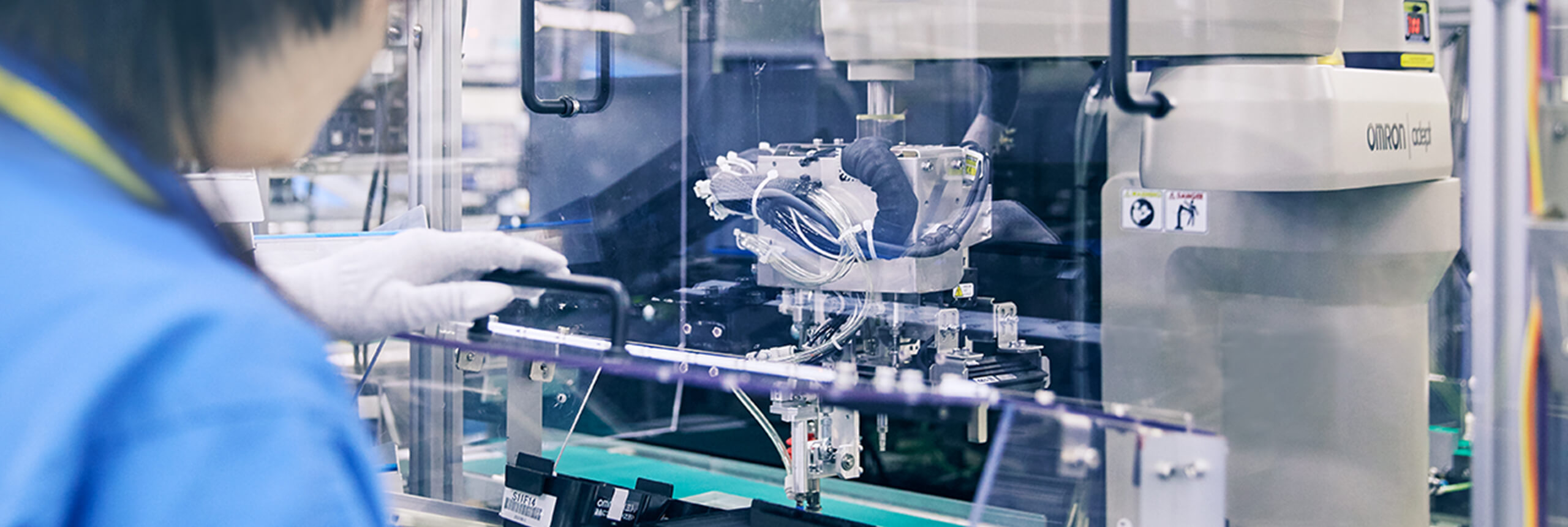
課題
需要変動に応じた、
タイムリーかつ高効率な生産
オムロン草津工場で生産している制御関連製品は、利用される環境や顧客ニーズによって製品の仕様も多様化しています。1台からの受注生産など、生産形態は典型的な多品種少量と言えます。
莫大な設備投資によって工程の大部分を自動化・機械化すれば、需要変動への迅速な対応と生産性向上を実現できるかもしれません。しかし、顧客ニーズに応え続けるためには採算が取れる投資でなければなりません。
自動化・機械化によって生産性が高まる工程、生産品目の変化に柔軟に対処できるよう人手を残しておいたほうがよい工程を合理的に見極めた生産ラインが求められていました。
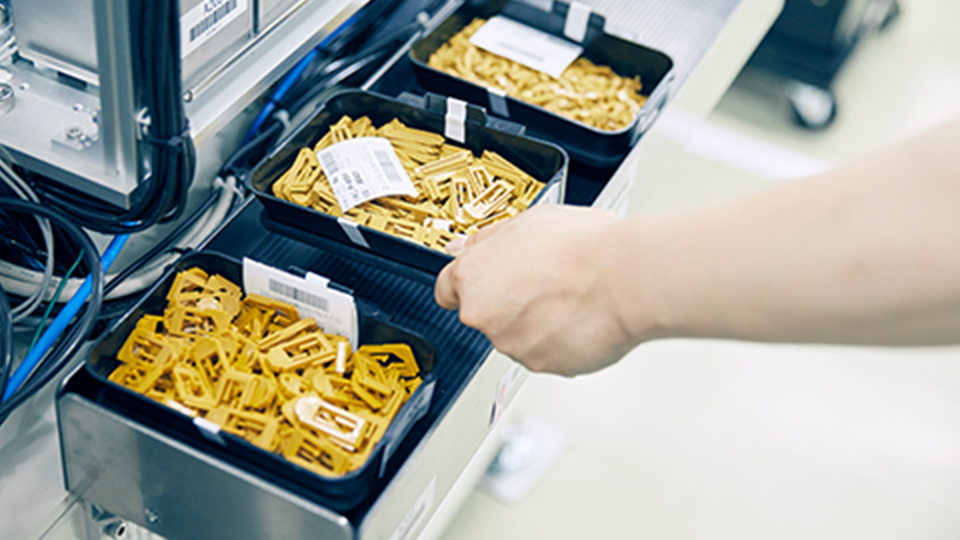
解決策
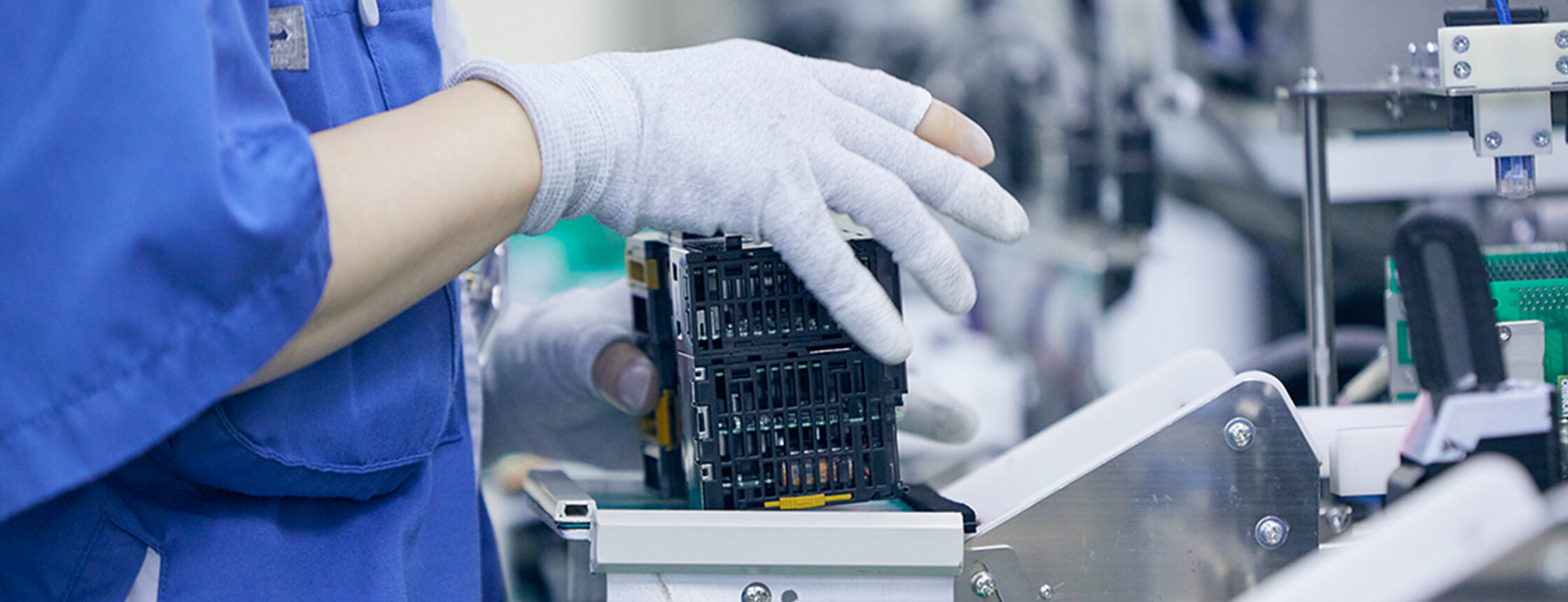
徹底的なIE*による
作業分析で“半自動化”。
手組みと自動化、
人と機械の最適な協調を実現
*IE: インダストリアル・エンジニアリング
(Industrial Engineering)
生産現場の工程や作業を
科学的に分析・評価し、
ロス・無駄のない最善の方法を生み出す手法
作業分析にもとづく自動化への見極め
今回の生産ラインで自動化すべき工程を見極めるにあたり、以下の観点で人の作業内容を徹底的に分析しました。
- ・人には簡単、機械が苦手なことは無理に自動化しない(コツ・感覚の要る作業の自動化は、設備投資の高額化を招く)
- ・人の動きや作業を、機械でサポートし、高品質を実現する(単純な繰返し・つらい姿勢・モレの出やすい複数箇所の照合検査など)
作業分析の結果、全10工程の内、6工程を自動化することにしました。
中でも「部品供給」と「機能検査」の2工程が特に自動化の投資効果が高いことが分かりました。
全てを自動化することにこだわらず、経済的な面も含め、人と機械が最適に協調する“半自動化”を選択しました。
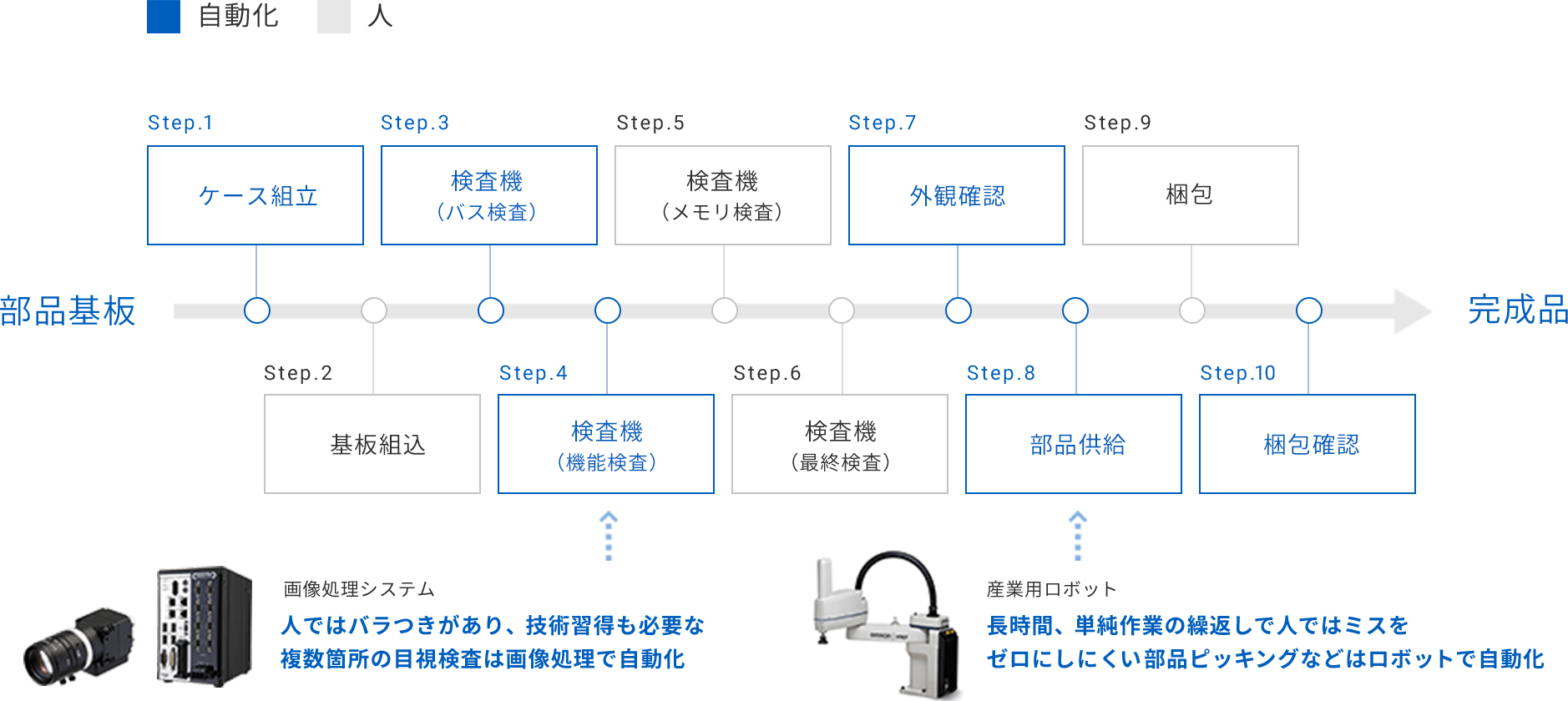
不良品を作れなくする自動化
部品供給
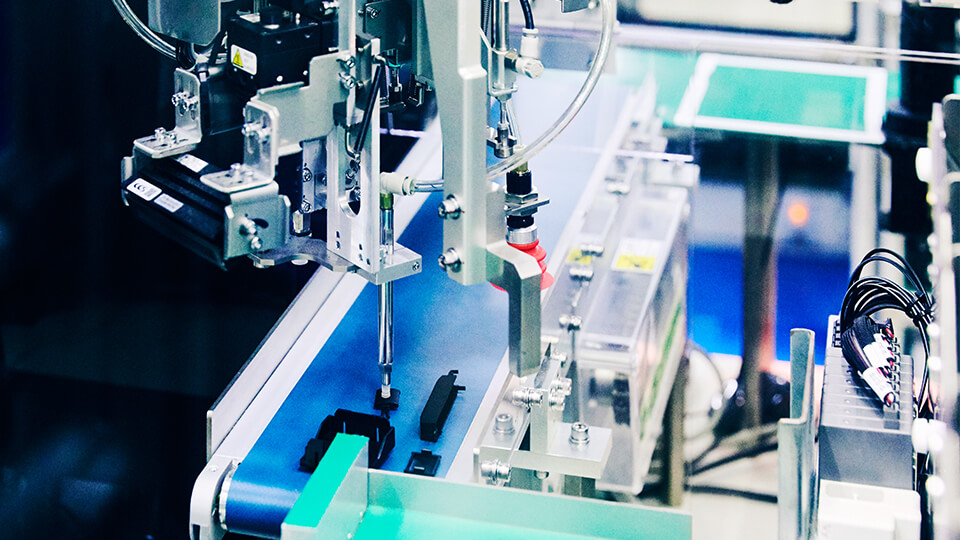
多品種少量で頻繁に切り替わる生産品目への部品のピッキングミスリスク撲滅へ、ロボットで自動化。生産品目ごとにロボットが確実に必要な部品・付属品をピッキング。カメラでの検査後、コンベアで作業者の手元へ供給。透明なアクリル壁で作業者とロボットを隔て、過接近を防止しています。
機能検査
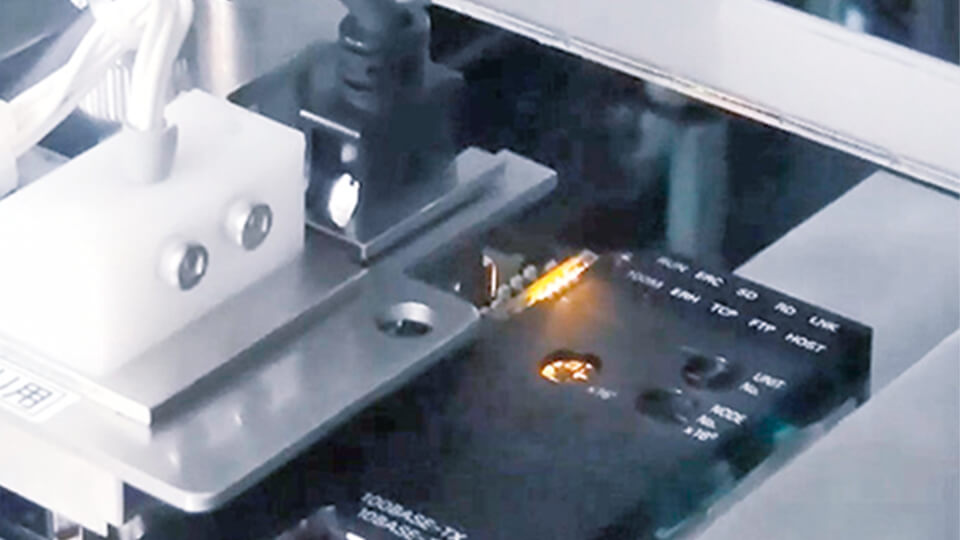
技術の習熟が必要だった検査工程を自動化しました。作業者による目視検査を行っていたLEDの点灯状態と色の確認を画像認識装置で検査。検査途中のスイッチの切り替え確認も自動化し、品質を安定化させました。
エラープルーフ化で、
習熟の浅い作業者のミスを防止
ケース組立
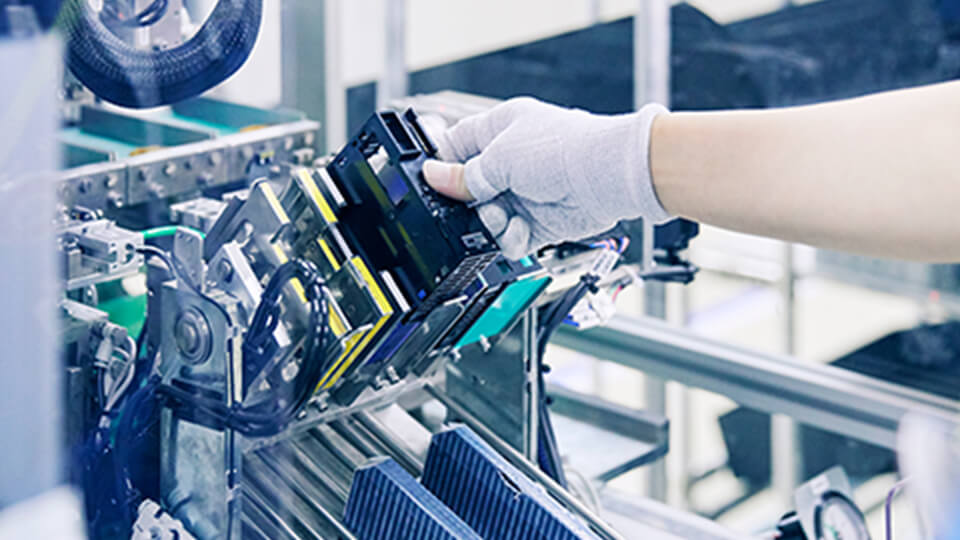
作業者が部品をセットする工程では、生産品目に合わせて治具の幅を自動調整。間違った部品をセットできないよう、作業を支援します。
最終検査
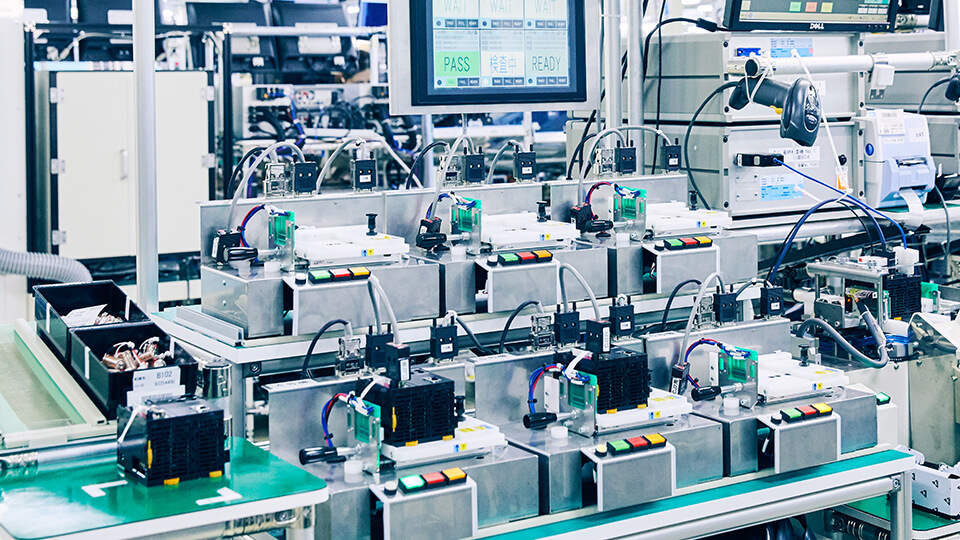
全ての検査機の治具に光電センサを設置しました。これにより、製品の着座位置確認と、どこをいつ通過したか検知し、検査忘れや追い越しを防止します。
成果
全自動化比1/10のコストで、
全作業工数の50%を自動化。
製品1台の組立時間を半減、
生産性200%へ改善
全てを自動化する場合に比べて1/10のコストで、全作業工数の50%にあたる6つの工程を自動化しました。
この自動化の一例として、組立工程における製品1台あたりの組立時間は5分→2.5分へ半減。
加えて、機械化による効果で、製造不良も削減できました。これにより、生産性は取組み前と比べて200%以上へ改善しました。
-
組立時間の短縮
例:組立工程における1台あたりの組立時間 5分→2.5分
(当社調べ・従来比) -
作業の熟練が不要
混流する多品種少量の製品への
複数箇所の目視検査など、
習熟が
必要な作業を自動化 -
製造不良を削減
人による思い込みや作業ミスを、
作業の自動化で削減
3つの手組み混流セル生産ラインを、
“半自動化”で1ラインへ集約
以前は3つの手組みセル生産ラインで、合計45品目以上の製品を分担して組立てていました。ただ、この方法では、需要変動によっては1日に2~3時間程度しか稼働しないラインが出てきてしまいます。このため、稼働率とスペース効率の改善が求められていました。
そこで、工程編成・作業工数を根本的に見直し、人と機械を最適に協調させることで、1ラインで45品目以上を柔軟かつ高効率で生産できる“半自動化”混流セル生産ラインへ集約する取組みを進めました。ラインを集約したことによって、組立に要する人員やスペースも効率化できました。
担当者の声
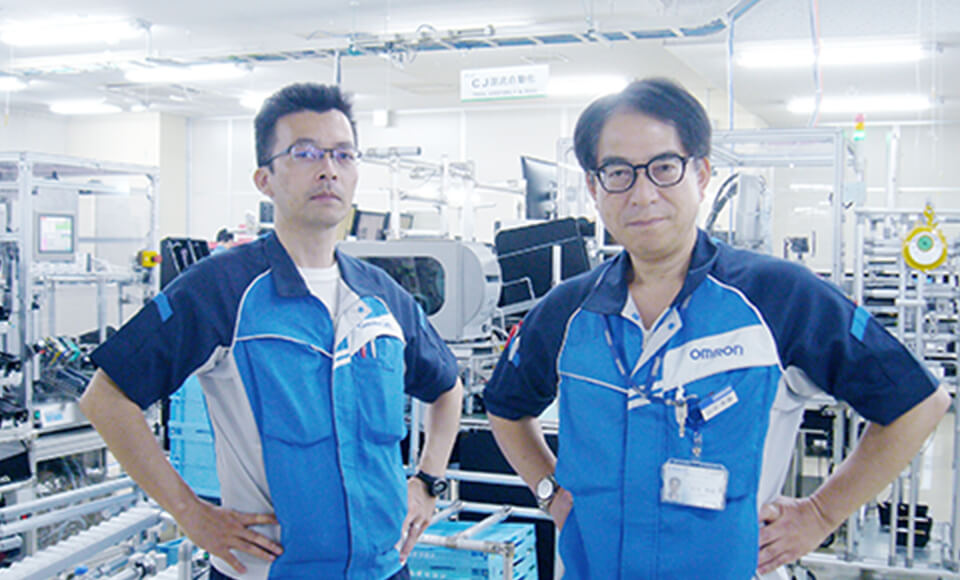
インダストリアルオートメーションビジネスカンパニー
商品事業本部
草津工場 生産管理部 生産技術課
齊藤 聡(左) 臼井 秀樹(右)
手術室の執刀医と助手の関係を
イメージしたライン
手術は時間との戦い。1秒も無駄にしないため、助手はすばやく確実に手術用具(ハサミやピンセット)を執刀医の手中に渡していく。
生産ラインでもこのような助手がいれば、無駄な動きや判断がなくなり生産性と品質が格段に高まると考えました。その助手を担ってくれているのがこのラインの自動化設備です。
このラインの主役は人です。機械は人の能力を最大化するための一つの手段であり、人の作業を機械に置き換えることとは異なります。
今後はコスト的に断念した作業への自動化にも取り組み、作業者の負担を減らしてさらに生産性と品質を高めたいと考えます。