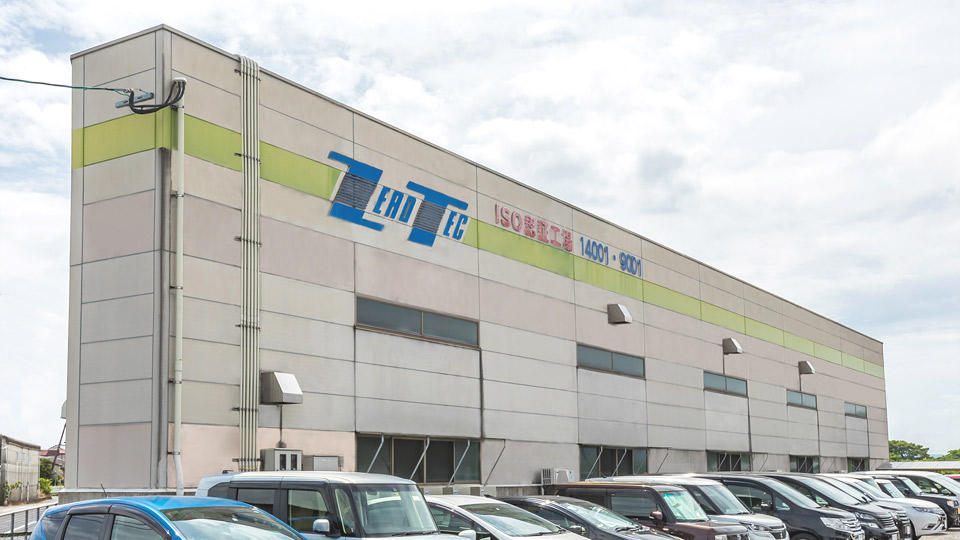
「無駄ゼロ」「不満ゼロ」「停滞ゼロ」に挑み、
従業員の満足度と意識を向上
聖徳ゼロテック株式会社様(以下、聖徳ゼロテック)は1975年、佐賀県での創業以来45年間で積み上げてきた高度な金型製作の技術とノウハウを基に、金型の製作・販売、プレス生産、単品部品加工などを請け負われています。同社の強みは、設計から試作・量産までスピーディに対応する、顧客満足度の高い加工サービスです。
さらに、企業価値の源泉である従業員の満足度と意識を高める現場改善にも積極的に取り組まれています。“まずはやってみる”というチャレンジ精神のもと、人手不足の解消や社員幸福度の向上、地域社会への貢献へ、社名を体現すべく「無駄ゼロ」「不満ゼロ」「停滞ゼロ」の実現に挑まれています。
課題
社員の“つらい”を解消!
現場の安全確保と、品質の安定化を目指す
以前、聖徳ゼロテック社内で“自分たちの仕事で一番つらい作業は何か?”と社員に問いかけたところ、満場一致で挙がったのが、今回の自動化の対象となった、製品のプレス加工だったそうです。プレス機の稼働部に作業員が何度も手を入れて行う作業は、すべて手作業であり事故の危険を伴う上、単調で心身に大きな負荷がかかります。
さらに作業精度が作業員のスキルに左右され、品質が安定しにくいという問題もありました。同社に限らず、今後、人手不足が進み、スキルの高い作業員が現場から減っていく可能性があります。こうした変化も見据え、同社はロボットの導入を検討していましたが産業用ロボットでは、プレス機1台に対して専用ロボット1台が必要なため、コスト面が見合いません。そこで、複数作業が可能で、他のプレス機との連結も可能な協調ロボットなら、コスト面もクリアできる可能性があると考え、導入へ踏み切りました。
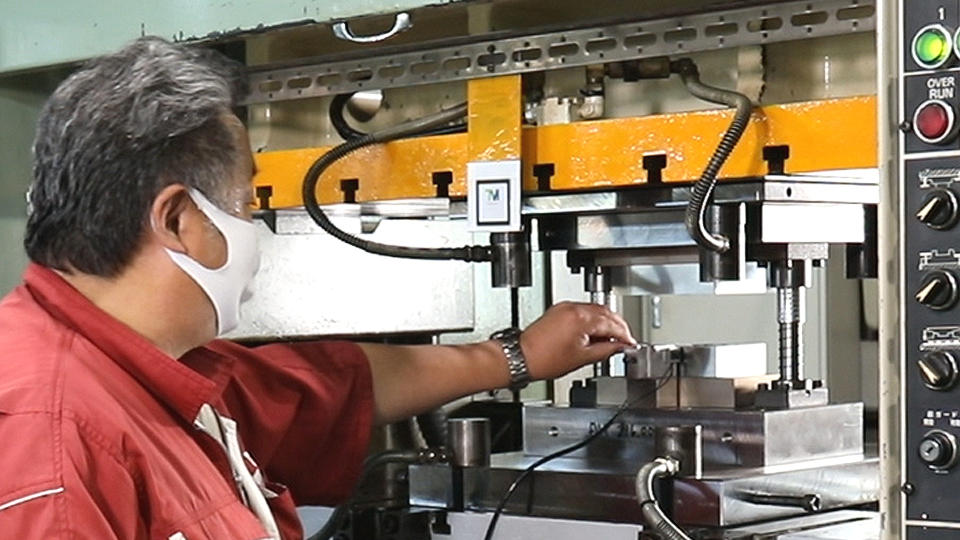
解決策
協調ロボットで製品のセットと取り出しの作業を自動化。
今後の展開を見据え、複数の工程や製品にも迅速に対応可能
可動式の協調ロボットを導入することにより、プレス機への製品のセットと取り出しの作業を自動化しました。作業精度も一定化でき、品質のバラつきもなくすことができます。また、製品や作業場所の変更などによる移設・再配置の際にも、オムロンの協調ロボットは、短時間で設定することが可能です。アームへ搭載したカメラ(画像照明付きビルトインビジョン)に参照点の認識用プレート「TMランドマーク」を読み取らせることで、アームと製品の間の相対的な関係が変更され、協調ロボットの動きを規定するすべてのポイントを再生成できるからです。複数の工程や異なるワークに対し、1台の協調ロボットで迅速・フレキシブルに対応することが可能になり、多品種少量生産にも対応できます。
そしてオムロンなら、協調ロボット本体だけでなくコントローラやセーフティセンサなど、効率的で安全なマシンテンディング(機械への製品の出し入れ)のシステムを構築するために必要なすべての要素を最適に統合したソリューションとして提供できます。システムを構成する機材間の確実な接続が実現し、お問い合わせ窓口も一本化できます。これにより、実務担当者の負担を軽減し、立上げ工数の削減にも貢献します。
成果
危険を伴う人手作業から、作業員を解放
協調ロボットを導入し、プレス加工での人手作業を自動化することによって、危険で単調な作業から作業員を解放できました。聖徳ゼロテックからは「作業員の負荷の軽減が実現し、最も“つらい”と感じる作業をなくせたことが最大の成果だ」と評価されました。
品質面においても、繊細な製品も正確に扱えるロボットハンドにより、熟練作業員と同等の作業精度を実現し、品質を安定化することができました。
また、可動式の協調ロボットは、同社内で危険な作業が発生する工程を選んで自在に配置できます。このため、高いスキルが求められる作業が同時に複数発生して、作業員が足りなくなった場合にも、協調ロボットに代替させることで工程を止めることなく、操業を継続することが可能になりました。
取り組みポイント
Point.1
聖徳ゼロテック自ら要件策定~プロジェクト管理。コストを抑え、ノウハウも蓄積聖徳ゼロテックでは、今後のモノづくりにはロボットの活用が必要不可欠と考えられていました。ただ同時に「コスト面で採算が合わないのでは?」という懸念もお持ちでした。より多くの工程、製品への作業をロボットによって自動化していくことを見据えれば、今回の導入だけ成功したら良いわけではありません。投資する以上、継続的に自動化の適用範囲を広げていくための道筋を明確にしておく必要がありました。このため、同社ではロボットの導入・運用において“できる限り自分たちで”を目標に掲げて、知見とスキルを蓄積することにこだわりました。
導入・運用へのプロジェクトは、同社の生産技術部門のメンバを中心に、ハンド部などメカ設計は設計パートナー(Ken‘s Factory)、架台部は部材メーカ(SUS株式会社)、調達管理・プロジェクト支援を商社(創ネット株式会社)、そしてオムロンのサービス(仕様策定・立上支援)も活用し、システムの構築に取り組みました。これにより、コストを抑えたロボット導入の実現とともに、導入・運用に関わるノウハウが同社に蓄積され、今後の展開への道が拓けました。
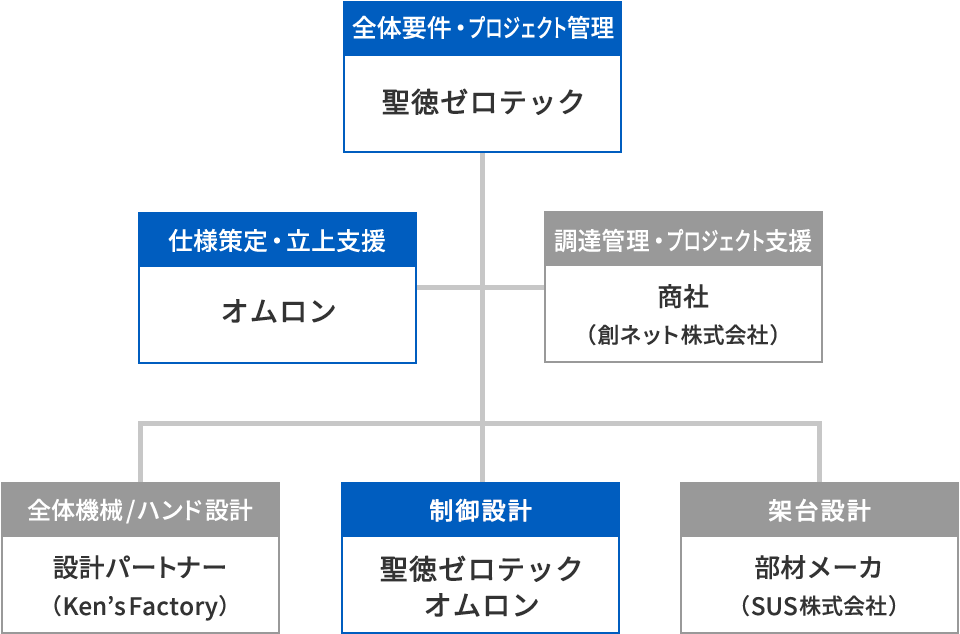
Point.2
メンテナンス性や移設時の利便性にこだわった、専用のオプション品を用意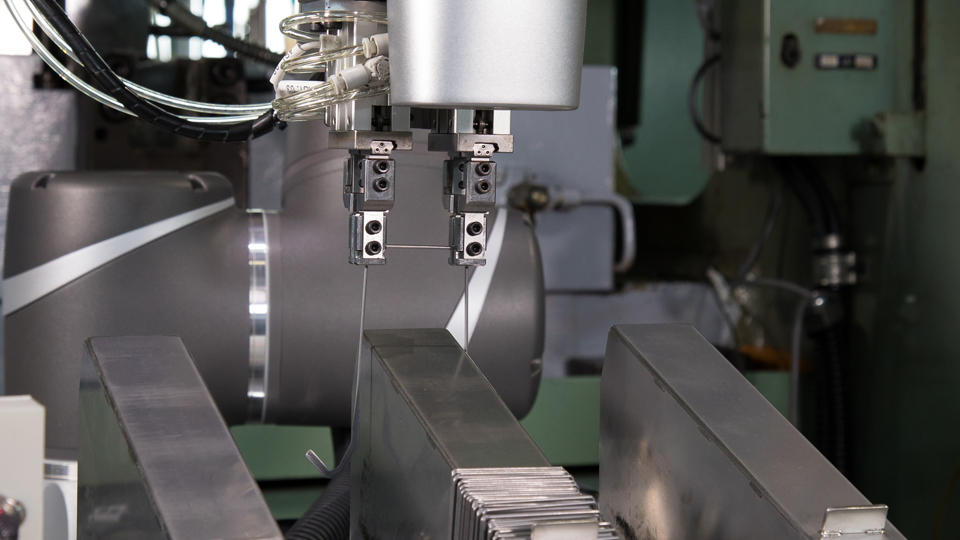
専用ハンド
導入対象の工程で扱う製品は細い針金を曲げたような形状の繊細なもので、これをしっかりとキャッチできるよう、ロボットのハンドには緻密な設計が求められました。また、ハンドを動かすアクチュエータには堅牢性が高く、かつ安価で故障時にも予備品が入手しやすいものを採用し、低コストでの運用を可能にしました。さらにハンドの先端部は、消耗しても先端部のみを交換できる構造にし、メンテナンス性や使い勝手のよさを実現しました。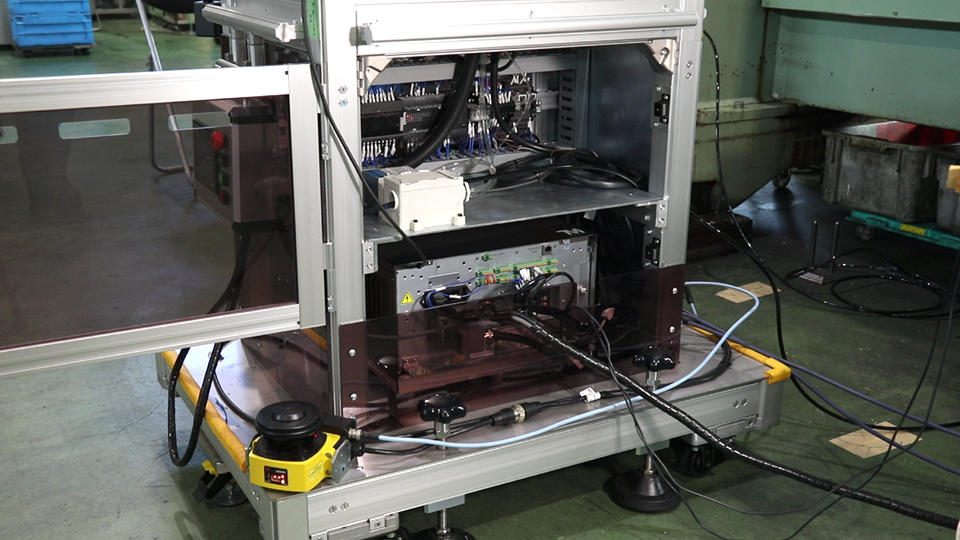
専用架台
プレス工程だけではなく、今後、移設して複数の作業を対象に運用していくことを見据えて、移動しやすく、移動先でのセッティングが容易な専用架台を製作しました。高剛性アルミフレームを使用し、強度や拡張性を向上。架台の中にコントローラなど必要な機材を収納できるように仕上げました。お客様の声
継続的な自動化の展開に大切なのは
“自分たちでやっていけること”
「ロボットを導入して実感したのは、“ロボット単品だけでは何もできない”ということでした。ロボットと周辺機器を組み合わせて、どのようにシステムを構築していけばよいのか、プロジェクト開始当時は知らないことばかり。全体を見渡してデザインする役割を担う人の必要性を感じました。
一方で、知識がない中でもロボットによる自動化を継続的に進めていくには“できる限り自分たちでやっていけること”が何より大切な要件でした。今回は、ロボットハンドや架台の製作には設計パートナーや部材メーカにも加わっていただき、それらを取りまとめる商社、全体をコーディネートしてくれるオムロンの各社が協力し合えたからこそ、実現できたと思います。“プレス以外の作業や、金型の製造にも使えないか?”など、今後このロボットをどう活用していけるか、次のプロジェクトの構想を描き始めています」
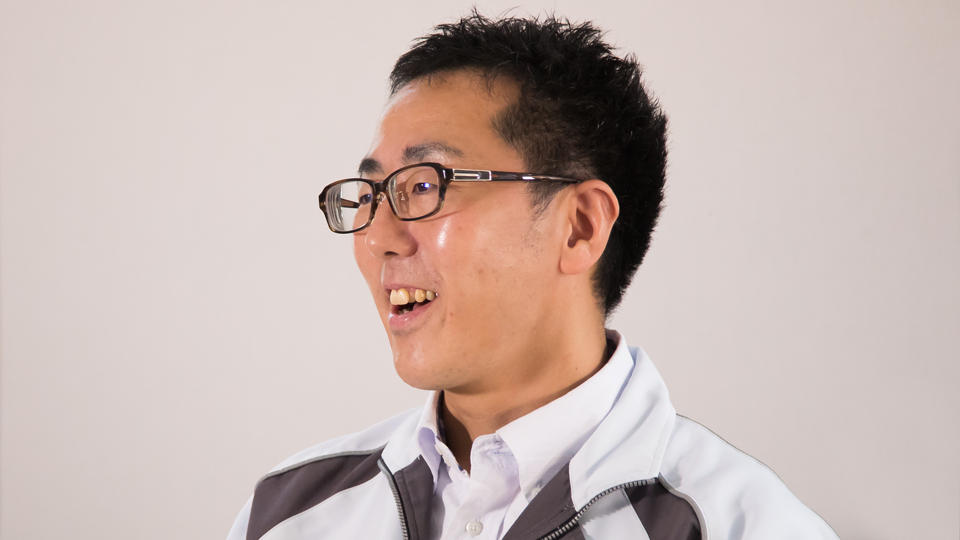
古賀 忠輔様
不明点もオムロンへすぐに問い合わせでき
スムーズな導入を実現
「元々、電気設計の担当だったのでコントローラなどの使い方は理解した上でプロジェクトに参加しました。
それでも、プログラムの仕様など分からないこともあり、この機会を通じて習得していきました。その際に不明点があっても、オムロンの技術メンバとはすぐに連絡・連携し、迅速に解消できました。このため、比較的簡単に導入することができました。問い合わせ窓口を統一化いただけたことなど、現場担当としては助かりました」
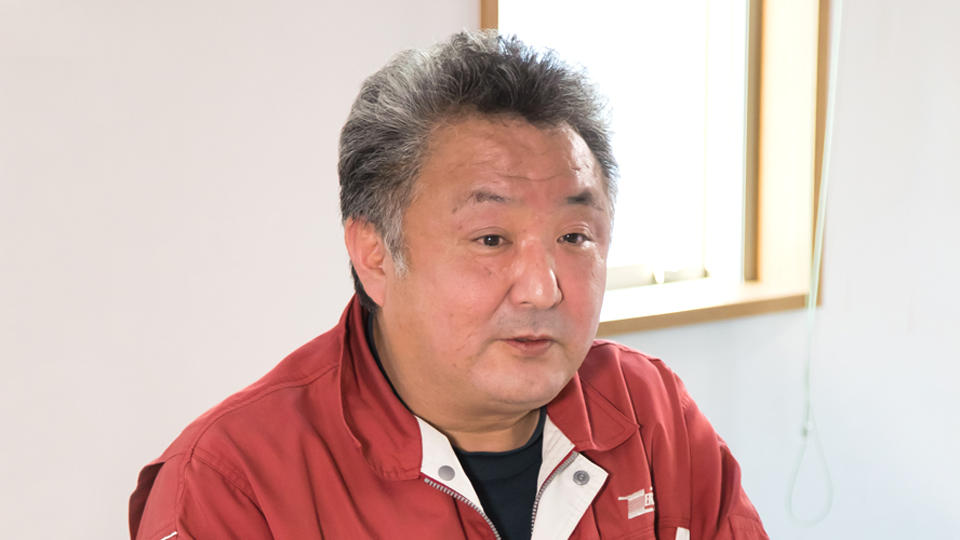
三浦 武久様