課題
安全で稼働率の高い生産ラインの早期構築
人・装置・製品の安全を確保するため、人手による作業の際には装置の動力を遮断する必要があり、生産ライン全体の稼働率が低下していました。また、より安全な生産ラインを構築するには、システムの冗長化によって信頼性を高める必要もありました。そのため、システムの複雑化、部品点数の増加、安全制御設計工数の増加などが設備設計者を悩ませています。
安全性をより一層高めて、稼働率の高い生産ラインを構築することに加えて、エンジニアの負担を軽減できる設計環境を整備する事が求められています。
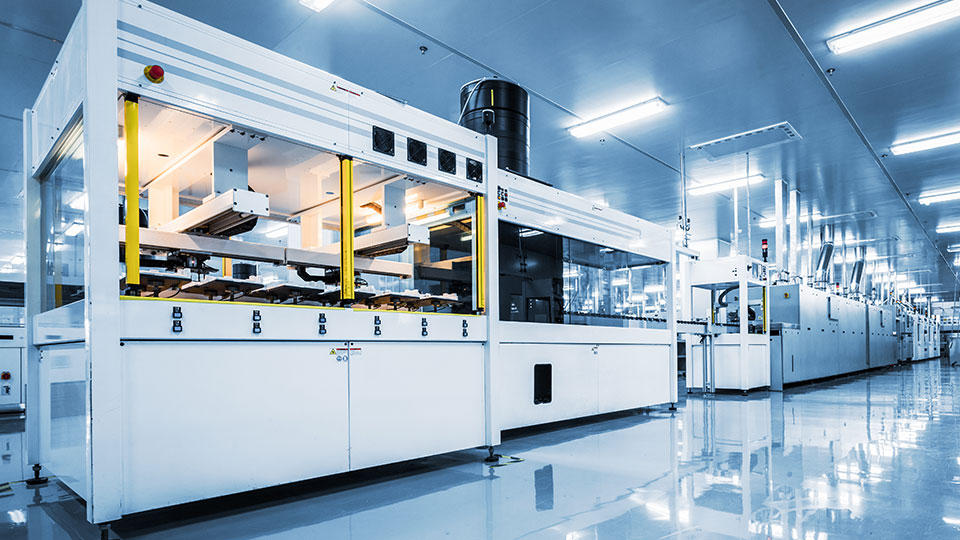
解決策
機械安全に適応できる制御システムで
加工機の稼働率向上と設計工数削減を実現
IEC 61800-5-2に準拠した1Sサーボシステムは、安全性を確認した上で、低速運転させながら人手による段取り替え作業を実現します。かつ、安全制御システムの安全機器や配線数を削減、プログラム設計も安全制御と標準制御を同じツールで対応可能なため、エンジニアの設計工数を削減できます。
装置を止めない段取り替え作業で
稼働率を向上
段取り替え作業では、運転・停止(動力遮断)を繰り返す必要がありました。作業者に負担がかかると共に、ダウンタイムが長くなっていました。
リスクアセスメントにより安全性を確認した上で、安全関連部の妥当性を担保し、低速運転させながら人手作業を可能とする運用が実現できます。モータ速度を監視する機能を使用することにより、各種調整にかかる作業の効率が高まります。
安全機器や配線の削減で
シンプルな安全制御システムを実現
機械安全に対応するには、安全専用機器や配線の二重化が必要でした。製造装置の進化と共に安全システムは複雑化の一途をたどっており、部品点数・配線数は倍増していました。
安全機能対応の1Sサーボシステムで構築された装置では、モータ速度や位置の監視機能、EtherCAT®をベースとした安全と標準のリアルタイム通信に対応したケーブルで、安全専用機器や配線数を削減できます。
安全制御と標準制御の統合プログラミングで
エンジニアの設計工数を削減
安全制御と標準制御のプログラムを作成する際には、操作感が異なる複数のツールを使用していたため、設計工数は増大していました。
オムロンでは安全プログラムの状態に合わせた標準プログラムでの変数設定が可能で、専用プログラムは不要です。エンジニアは1つのツールの操作を習得するだけでよいので、設計にかかる負担は軽減、専門性の高いエンジニアに依存した設計〜立上げ業務から脱却できます。