品質改善のデジタル化
工程内の無調整率99.9%実現へ、
不良ゼロを目指した車載部品メーカーの挑戦
提供 :アイティメディア株式会社 掲載メディア :TechFactory
この記事は、2020年10月01日 10時00分に記載されたTechFactoryからの転載記事です。
製造現場にとって目指すべき目標である「不良ゼロ」だが、実際に実現するには非常に難しい。こうした中でメカニカルリレーを製造するオムロン リレーアンドデバイスでは新たに「不良ゼロ」に向けた品質改善への取り組みを開始した。同社の取り組みを紹介する。
「ゼロディフェクト」への挑戦
オムロン リレーアンドデバイス(熊本県山鹿市)は1971年に山鹿立石電機として設立されたオムロンのグループ企業である。現在は、オムロンエレクトロニック&メカニカルコンポーネンツビジネスカンパニー(EMC)の子会社として、産業機器や家電、自動車に搭載するメカニカルリレーを生産している。従業員数は国内715人、海外約4100人(2020年4月1日現在)で2019年度の売上高(単体)は268億円だという。
メカニカルリレーは、外部から電気信号を受け取り、電気回路のオン/オフや切り替えを行う部品である。汎用部品であるため、これまで生産は自動車、家電などの完成品メーカーに向け「大量に生産し、大量に納めるというプロダクトアウト型の発想で進めていました」とオムロンEMC 生産技術センタ長の木村祐之氏は語る。
ただここ数年、顧客からのリレーに対する品質要求が大きく変化してきた。約5年前まではPPM管理(100万分の1個単位の管理)の要求基準に対応し、100万個に1~2個不良が発生し得ることを前提に、その流出防止管理を徹底してきていた。しかし、それが車載業界を中心に「ゼロディフェクト(不良ゼロ)」という要求が強まり、最近では家電や産業機器の業界でもこの傾向が強まってきたという。
オムロングループでは2017年に中期経営計画「VG2.0」を発表し「顧客価値創造」を基軸に置いた取り組みを進めている。その中で「リレー製造についても『顧客価値創造』や逆に『顧客価値を損なう』というのはどういうことなのか、ものづくりの原点に戻ってあらためて考え直し、最大の顧客価値損失は不良品を供給し顧客製品で不具合を起こすことだという結論になった。「われわれが何をなすべきかを考え、『工場から不良品を1個も出さない』ということを目指す姿に設定した」と木村氏は語る。そこで2017年から「不良ゼロ」に向けて取り組みが始まったという。
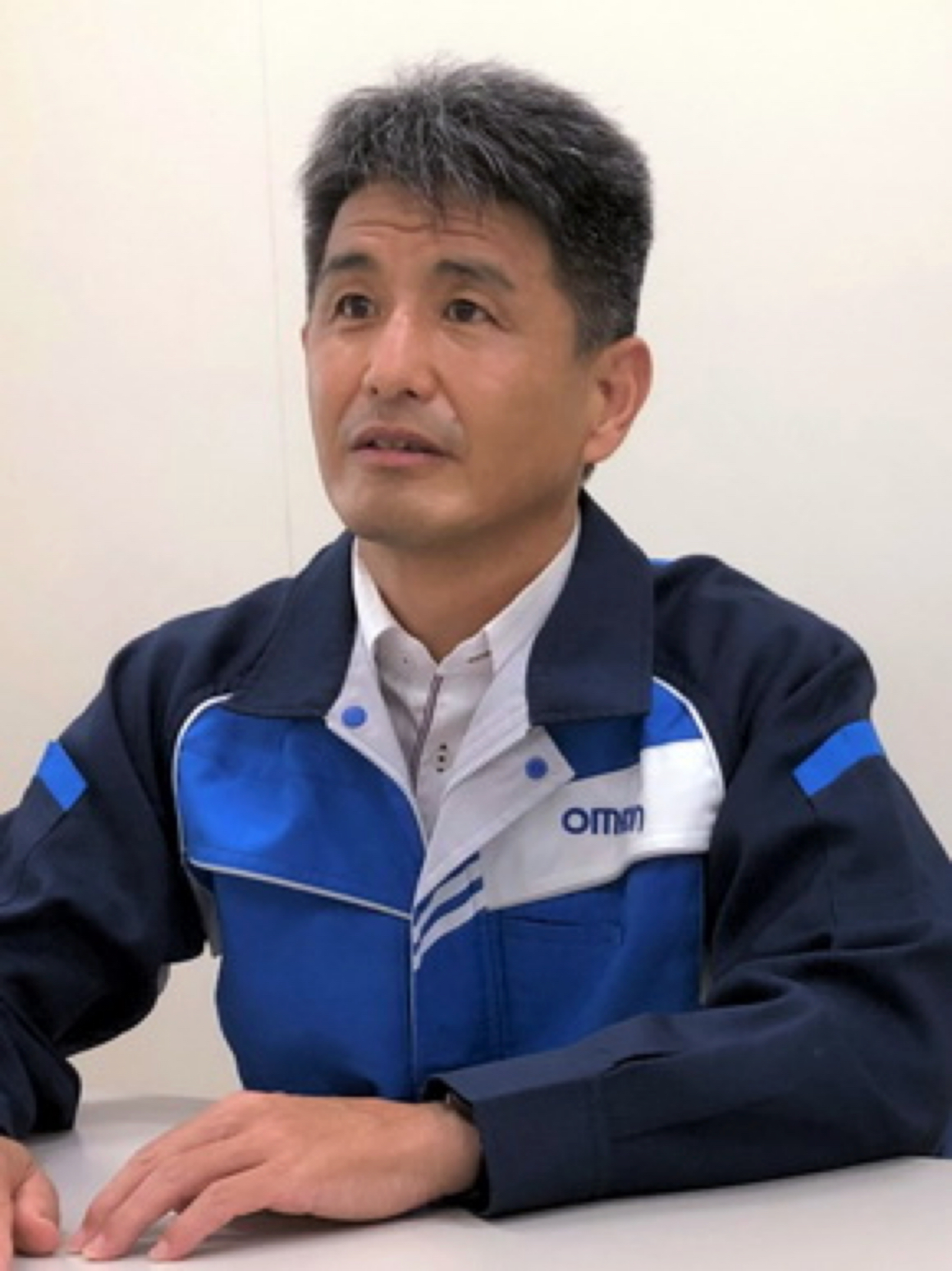
メカニカルリレーでの「ゼロディフェクト」への道
メカニカルリレーは部品と部品の組み合わせで最適チューニングを行い、最後に全数検査を行うことで、品質を保証して出荷していた。この方式では、最終出荷製品に不良品が入ることは防げるものの、生産工程での不良品発生を抑えることはできず、ものづくり工程全体として「本当の意味での不良品ゼロ」は実現できていなかった。「ゼロディフェクト」を実現するためには、生産プロセス段階から品質を把握し、不良を生み出さない取り組みが必要になる。品質がばらつく因果関係を分析し、特定された要因を監視・制御することで、工程内から不良品を生み出さないようにすることを目指した。
ただ、工程内で品質保証を行うには大きな課題があった。工程内で品質保証を行うには少なくとも3つのデータが一元的に管理できるようになっていなければならない。1つ目が入ってくる部品の情報(インプット)、2つ目がこれらを加工したり組み立てたりする設備や人の情報(プロセス)、そして3つ目が組み立てられた製品の品質情報(アウトプット)である。
過去からそれぞれの情報については個別管理できていたものの、他のデータとひも付けられた形では蓄積や管理が行われていなかった。そこで、不良ゼロを目指した取り組みとして最初にインプットの計測(入荷される部品の計測)を開始した。ただ、大量の部品データを短時間で取得し、それを統計的処理に基づき蓄積する仕組みを単独で実現するのは難しかった。そこで、対応策について社内外で情報を集めたという。調査を重ねると「同じオムロン社内で、FA製品などを扱うインダストリアルオートメーションビジネスカンパニー(IAB)が、こうしたニーズに合致する計測装置を開発していると聞き、相談した結果、計測できることが分かり検証する流れとなった」(木村氏)。
こうしてインプット情報を取得できるようになり、設備や人の情報(プロセス)を取得する取り組みへと進んだ。設備状態(プロセスデータ)の計測については既に導入していたPLC(Programmable Logic Controller)からの位置情報や、新たに設置したトルクセンサの情報を組み合わせることで加工のプロセスデータが取れることが判明した。こうして、インプット、プロセス、アウトプットのデータがそろうことになったが、実はここからが苦難の連続となったという。
「インプットやプロセス、アウトプットなどで日々膨大なデータが蓄積できるようになったが、これらのビッグデータを活用し、どんな関係性を持った価値ある情報なのかをデータ分析したが、有効な要因を特定することまでには至らなかった。モーター挙動などをはじめとする設備状態(プロセス)からは最大で1秒間に2万~3万項目のデータが取得できる。1カ月に100万個以上造る製品でこれらのデータを収集・保管管理し続けることは非現実的となる。また、出てくるデータの形式が機器によって多種多様で、これらを整理するだけで膨大な時間が必要になり、社内だけで実現するのは不可能だと考えた」そこで、あらためて社内外で情報収集を進めた中で「再びオムロン IABカンパニーで製造現場データ活用サービス『i-BELT』を展開している情報を入手、共に課題解決に向けた取り組みを開始した」と木村氏は語る。
データ分析から真因特定へのアプローチ
オムロンの「i-BELT」は、製造現場のデータを活用し、その収集から見える化・分析・制御まで、顧客課題に寄り添い共に解決する共創型のサービスである。一般的なデータの見える化や分析だけでなく、オムロンが長年培ったFA現場の制御の知見と最先端の技術を組み合わせ、顧客の製造現場の課題解決までを最適に支援できる特徴がある。サービスとしては、生産管理、品質管理、設備効率、省エネの4つのメニューに、それぞれ見える化(現場課題の特定)、分析(課題真因と予兆の発見)、制御(最適制御の実現)の3つのステージを設け、合計12の体系を用意している。
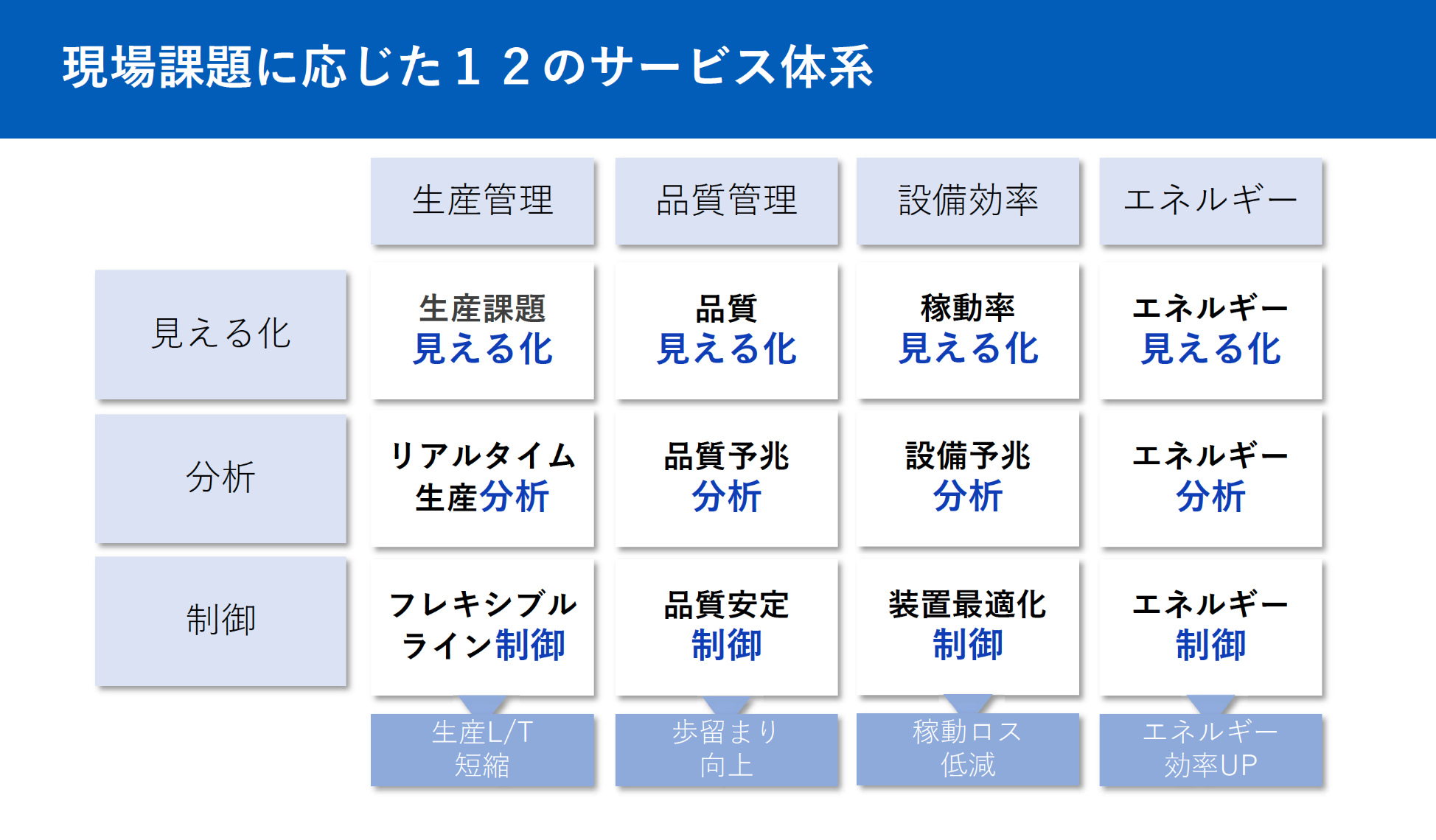
今回は、「製品歩留まりの向上」「工程内品質保証」に向けた共創となる。具体的にはデータの活用により「組立加工バラつきの最小化」と「異常判定ロジックによる流出防止」を実現する。これにより品質コストの低減、生産性の向上に貢献する。
i-BELTサービスプロセスは、お客さまへのヒアリング、現場診断・課題の共有、取り組みゴールを設定するところから始まる。その後「見える化」「分析」「制御」のプロセスを実行し、成果が出るまで仮説検証のサイクルを回し続けるという。
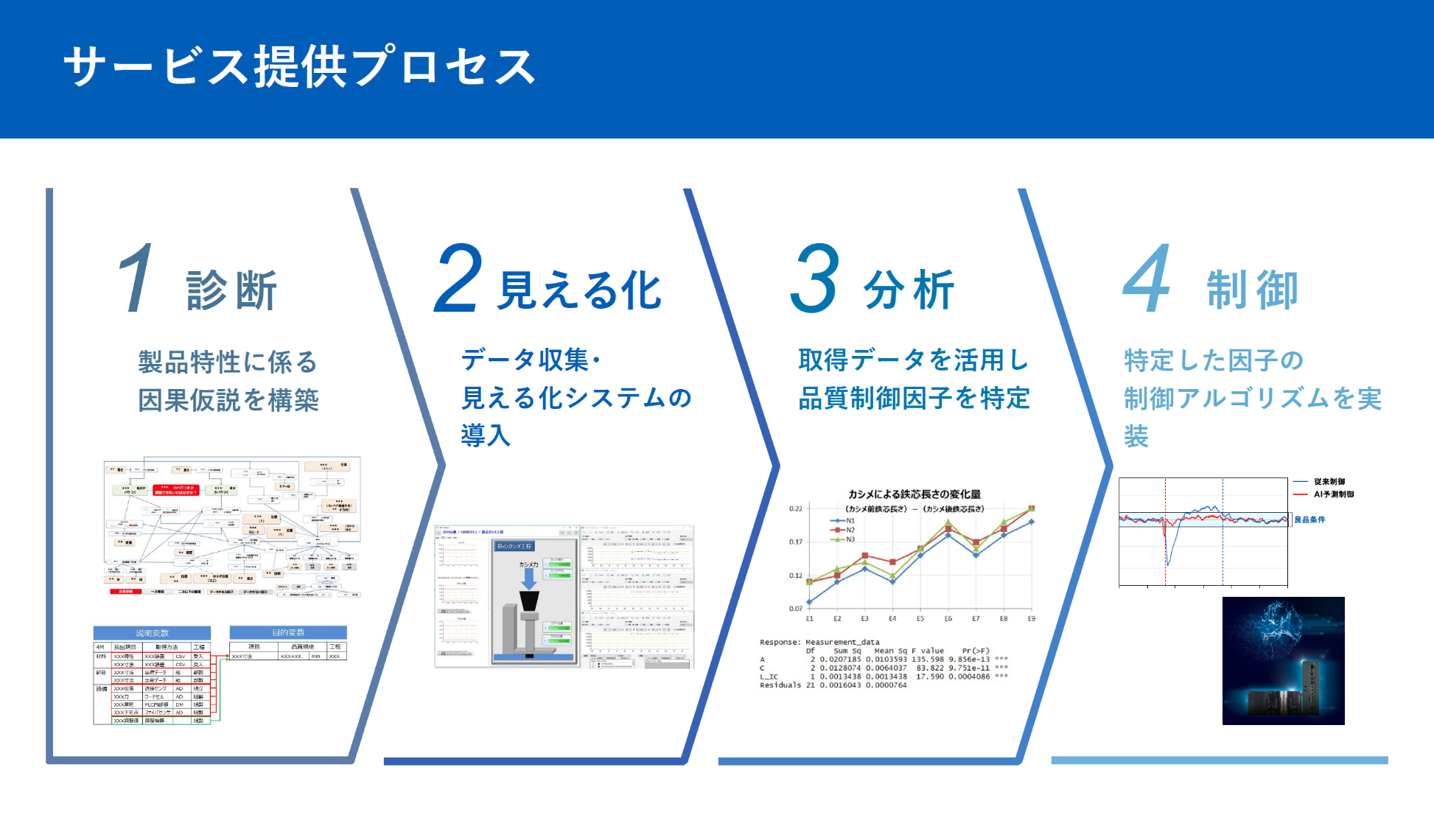
今回の取り組みの「見える化」のプロセスでは、QC工程図をベースに顧客の製造、生産技術、商品などさまざまな分野のノウハウを共有しながら課題真因候補の仮説を立てた。
分析プロセスでは、2ステップに分けて実行、まず「見える化」で蓄積したデータを用いて、課題真因候補に対する影響度を分析し、課題真因候補の絞り込みを行う。次に課題真因候補に対して、品質工学などを使って具体的に検証して因子を特定する。制御のプロセスでは特定した因子に対して実際に装置にフィーバックする条件、ロジックを構築するなど制御アルゴリズムを実装するところまでを行った。
「i-BELT」を推進するオムロン IAB企画室の阿瀬井宏治氏は「データ分析はあくまでも一定条件下での相関であり、条件が変化すると日常現場で発生する4M(Man、Machine、Method、Material)に対してコントロールできずに品質が安定しないことがあります。因果を特定できれば、事象の真因が明らかになるため、4Mの変動があっても品質をコントロールすることが可能になります」とその意義について語る。
基準となる製造オーダーのIDをベースに、加工プロセスに必要なアクチュエーター、サーボモーターなどからのデータをひもづける方法を設計し「実際にどのようなデータを蓄積するか」「因果特定だけでなく、ライン全体を対象としたトレサビリティーが構築できるか」などを考えてシステム構築を行ったという。「実際にシステムの導入時には、部品による加工のバラつき、装置によるバラつきが見えてきた際に、仮説として立てた事象が発生しているのかの検証を行います。こうした取り組みで必要なデータを特定し、それをリアルタイムで活用することが可能になります」と阿瀬井氏は述べる。
また、因果の特定については「顧客の設計、品質、生産技術などの各部門から知見を集めて、徹底的に原因を追究する。さらにQC七つ道具などの品質手法を用いて検証することで、見えなかった因果を特定していくことができます。これを基に特定した因子に対して手を加えるもの、そうでないものを判断するという流れです」と阿瀬井氏は取り組みについて述べている。
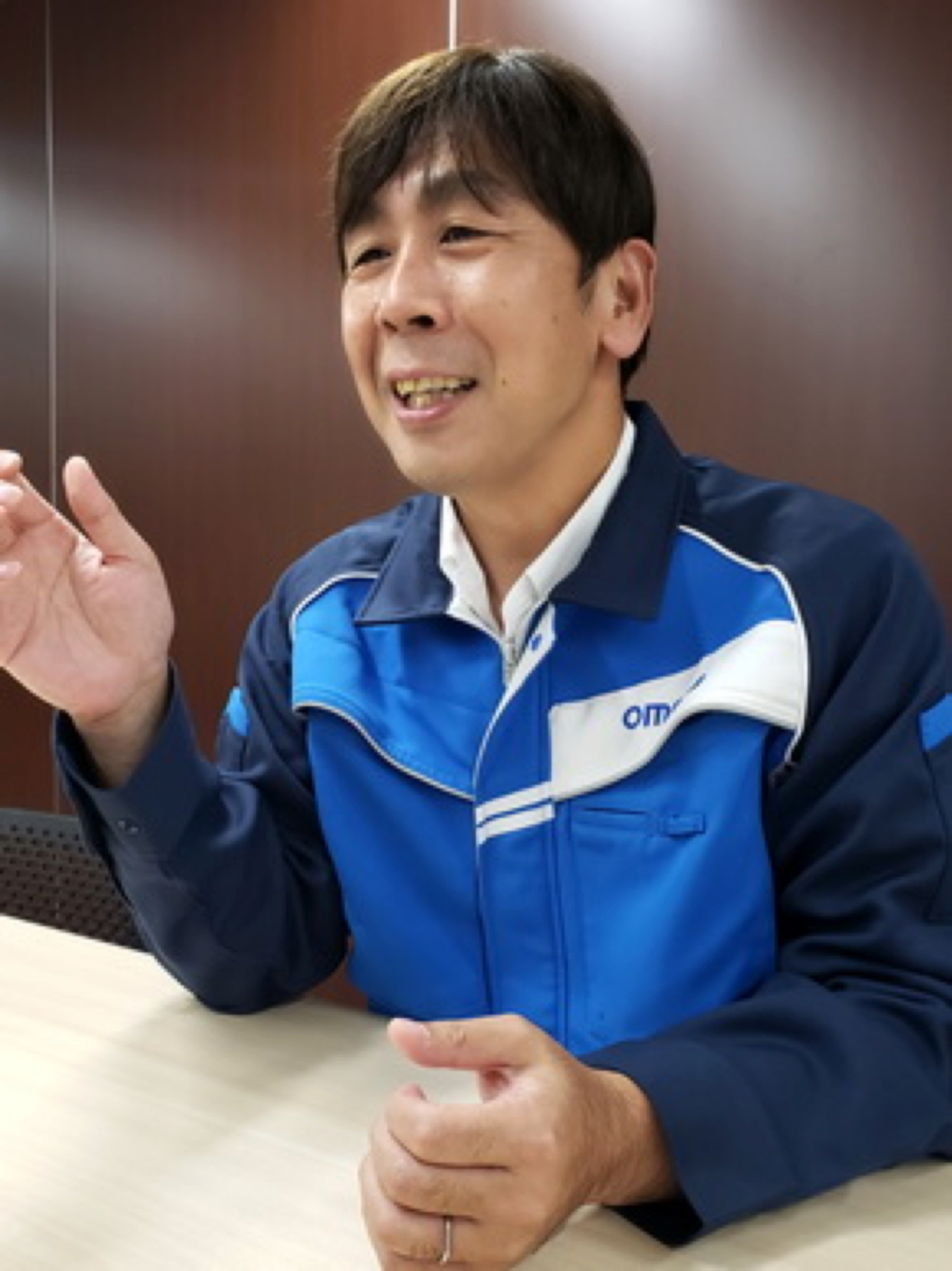
無調整率99.9%で廃棄ロスを5分の1に
「i-BELT」サービスの導入により、インプット、プロセス、アウトプットのデータを基に、品質に関連していた4Mの因果が徐々に解き明かすことができてきた。そして、それが成果にも結び付き始めているという。
具体的には、中間検査工程での無調整率をこれまでの99.5~99.7%だったものを、ワンランク高い99.9%以上に高めるめどが立ちつつある。また、これを実現することで、再調整工数と廃棄ロスを従来の5分の1に引き下げられ、リレー1機種当たり500万円のコスト削減につながる試算もあるという。
また、インプットからアウトプットまで一連の因果関係が見えてきたことで、従来はひもとけなかった因子の特定が行えた例などもあったという。「従来は製品不良の要因がこれにありそうだと思っていても特定できなかった問題が、今回設備情報とセンシングしたデータを分析することで、部品起因なのか設備起因なのかを明確に分けて評価できるようになった」(木村氏)。
さらに「水平展開するためには因果を特定した重要なデータに絞り込み、海外を含めた他工場や他ラインに展開できるようにしていきたい」と木村氏は述べている。
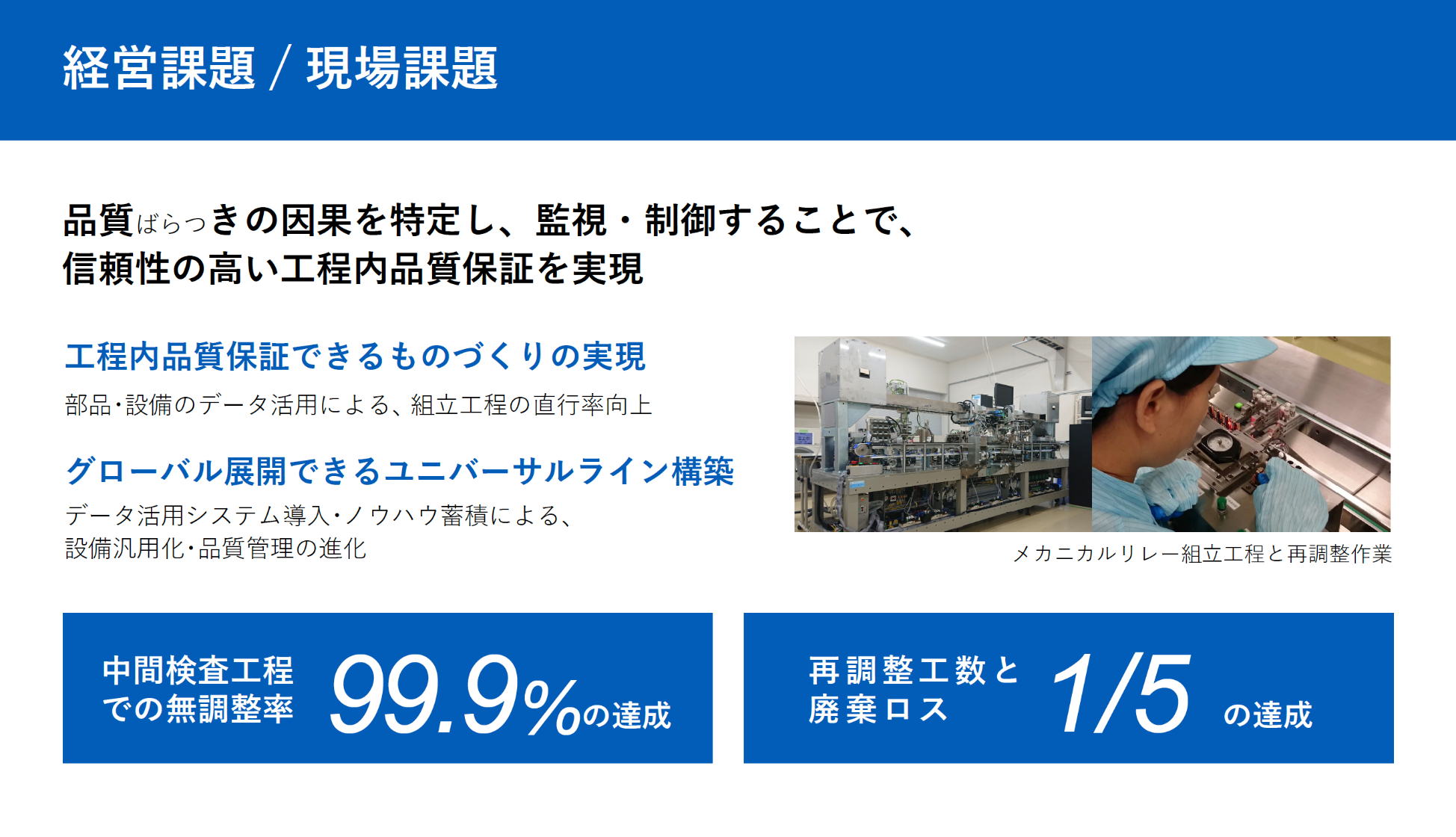
データだけでなく、現場ノウハウや幅広い制御機器の知見も
今後の展開として、世界中で使っている生産設備の品質向上に向けて、あらゆる設備情報を一元的に管理するグローバルスマートファクトリー構想の実現を目指しているという。また、これらを実現できれば、新商品に対する生産ライン立ち上げのスピードアップも可能となる。「こうした取り組みはデータを分析するだけでは実現はできない。製造現場のノウハウやセンサー、コントローラーなど幅広い制御機器の知見や、それらの知見に基づいたデータ活用のノウハウも必要となる。自社グループ内で早期に『i-BELT』による共創ができたのは非常に幸運であった」と木村氏は述べている。
「不良ゼロ」へのニーズが高まる中、同じような品質問題で悩みを抱える製造現場は多い。製造現場のデータ活用や機器の使いこなしのノウハウまでサポートしてくれるオムロンの、「i-BELT」は大きな力になってくれることだろう。
提供:オムロン株式会社
アイティメディア営業企画/制作:TechFactory 編集部