
i-Automation!で生み出す、
新たな“食のオートメーション”で食品製造業界の
課題を解決
2018年6月12日〜15日、食品機械の総合展示会「FOOMA JAPAN 2018(2018国際食品工業展)」が東京ビッグサイトで開催されました。オムロンは、“品質と生産性を両立できる姿がここにある 〜ロボットとIoTで人を支援〜”をテーマに出展。i-Automation!のコンセプトの下、 IoT、AI、ロボティクス、省人化 を切り口に食品の製造現場が抱える様々な課題へ、7つのソリューションを提案しました。


品質と生産性の向上を両立するソリューション
形状や材質が不揃いな原料を扱い、品種変更も頻繁に起こる食品の製造ラインには、熟練作業員の高度なスキルがなければこなせない、自動化が困難な工程が数多くあります。ところが、他業界と同様に、多くの熟練作業員が退職の時期を迎える一方で新たな作業員の確保も難しく、深刻な人手不足が顕在化してきました。さらに、“食”に対する消費者の意識は年々高まり、より安全で高品質な食品の提供が求められています。
リソースを有効に活かしながら、品質や安全性、さらには生産性をも向上させていくためには、製造ライン全体の抜本的な改善が欠かせません。オムロンは、i-Automation!にもとづく新たな“食のオートメーション”が、食品業界が抱える課題の解決に大きく貢献すると確信しています。
「FOOMA JAPAN 2018」では、上流の原料受入から下流の出荷検査まで、製造ライン全体を革新するオムロンのトータルソリューションを、具体的なデモンストレーションを交えて披露しました。
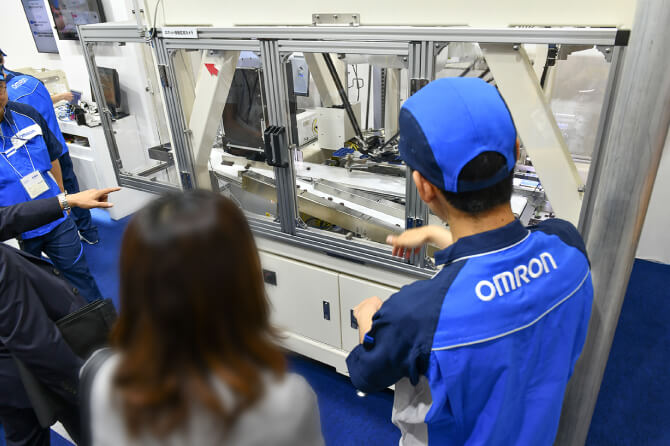

お客様の声
“オムロンはセンサのメーカというイメージが強かったが、先進的な自動化技術を持っていることを知って驚いた。食品の製造現場に即した様々なソリューションの展示は、課題解決のヒントになると感じた”
IoT
IoTを駆使して、作業ミス撲滅と
品質トレーサビリティ向上を実現
モノや人の状態・動きをありのままに知ることができるIoTは、様々な品目の製品を工程やレシピを変えながら作る食品製造ラインの高効率化に極めて効果的な手段だと考えています。そこで、ブースでは、食品業界に向けたIoTソリューションの例として、原料受入後の計量・配合工程での作業ミス防止とトレーサビリティ向上のためのソリューション*を紹介しました。
まず、受入れた原料を製品別のレシピに沿って計量・配合し、製造ラインに投入します。これまでこのような作業は、手書きのチェック票と照合しながら人手で行っていましたが、原料の入れ忘れや入れ間違いなどのミスが起きることがありました。
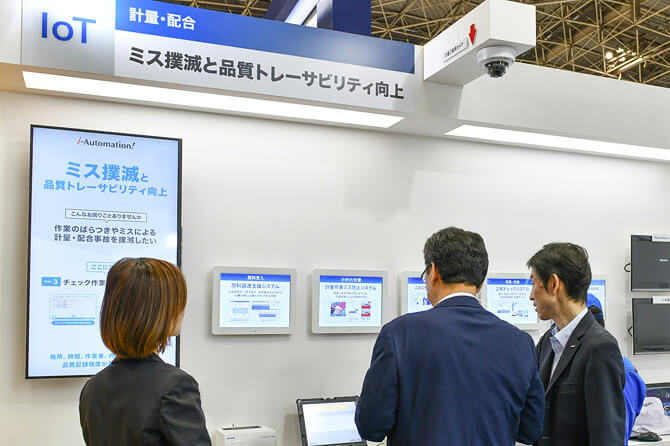
このソリューションでは、原料が入った袋に、原料の種類や量、賞味期限などの情報を予めQRコード*に記録したラベルを貼り付けて管理します。計量時には、QRコードを読み取り、正しい原料がレシピ通りの分量で計量されていないと、次の配合工程に移れない仕組みになっています。これによって、ミスの発生を撲滅するとともに、原料から製品までの流れを原料ロット、製品ごとに追跡でき、トレーサビリティを向上します。
万一、不良品が出てしまった時にも、モニタリングシステムを併せて使えば、製造現場に設置したカメラの映像記録から、該当品を生産した時の様子を再生し、いつ、どこで、誰が、どう対処して出来上がったのかが追跡できます。また、帽子に個人を判別する2次元カラーバーコードを付けることで、モノの動きだけではなく、人の動きも管理できるようになります。熟練作業員の動線を記録して、現場のスキルアップにも活用できます。
*このソリューションは、オムロンフィールドエンジニアリング株式会社による展示です
*QRコードは株式会社デンソーウェーブの登録商標です
お客様の声
“IoTという最新のIT技術のすごさを強調しているだけではなく、間違った作業ができない工夫がされている点など、ソリューションの作りが現場に即してよく練られていると感じた”
IoTで製造現場の設備の状態を監視、
点検作業の負担軽減
また、IoTを活用して、モータなどの設備の状態を監視し、突発的な設備の停止を未然に防ぐソリューションも提案しました。
突発的な設備停止は、修理部品や代替品の取り寄せなどに時間が掛かるだけではなく、鮮度が重要な食品を扱う現場では停止時の仕掛品を廃棄しなければならず、事業損失につながります。いかに定期点検を確実にしても、稼働状況によっては、点検と点検の間に故障してしまう可能性があります。モータの動作音や振動から故障の予兆を察知できる熟練保全員がいる現場もありますが、ここでも人材不足が深刻です。点検のノウハウを数値化し、誰でも設備の状態を監視できるシステムの登場が待たれています。
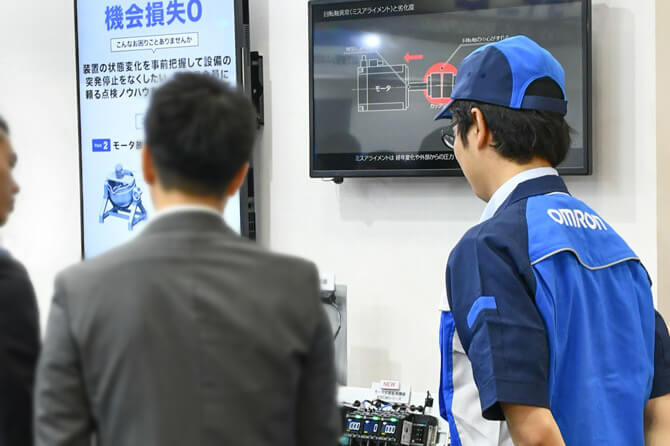
このソリューションでは、モータの絶縁抵抗値や駆動電流の波形、温度、振動などの変化を、「モータ状態監視機器K6CM」を活用して遠隔地から常時監視。モータ内部の劣化状況を把握して、設備の状態変化を探り出します。モータの劣化度が、予め設定したしきい値を超えた場合には信号を出します。工場内に数多くあるモータを一元監視することで、現場の装置・設備点検作業の負担を軽減できます。
AI
熟練工に頼っていた加工条件の
調整をAIで自動化
AIは、熟練工の技術を自動化するための極めて有効な手段です。ブースでは、包装工程にAIを活用することで、これまで熟練工の経験に頼っていた作業を自動化するソリューションを提案しました。
食品の包装では、包材を熱圧着して製品を封止する方法がよく使われています。こうした包装の工程では、包装の高速化や包材の薄肉化など、難易度の高い加工が求められるようになりました。ところが、熱圧着によるシールは加工条件の設定がデリケートで、包材の厚さや装置の温まり具合、その日の気温によって、シールの品質が大きく変わってしまいます。安定したシール品質で高速化や薄肉化に対応するには、熟練工による加工条件の微調整が欠かせませんでした。
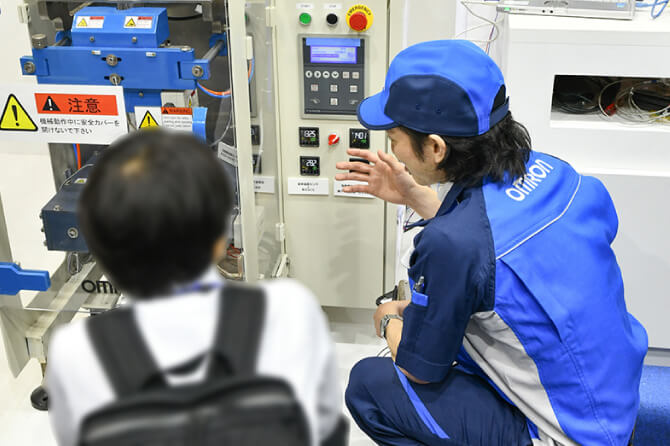
このソリューションでは、シール温度の立上り状況の推移をセンサで検知しながら、業界初*の適応制御技術によってPID値を自動調整し、安定したシール品質を実現できる温度に制御します。また、シール部近くに設置して装置温度を正確に計測する包装機用温度センサ、取得した温度データの中からノイズとなる揺れを取り除く、自動フィルタ調節機能の技術も投入されています。こうした、入力からデータ処理、制御までの構成要素をきめ細かく最適化したからこそ実現できた、オムロンの総合力を結集したソリューションです。
*FA用の汎用温度調節器として、2017年3月現在当社調べ
お客様の声
“食品業界でAIを利用する具体的イメージがなかったが、とても身近な部分に応用できることが分かった。製造現場には細かな動作条件の調整が必要な装置は多く、AIの活用効果が期待できるところは意外と多いかもしれない”
ロボティクス
工場内の単純作業を
ロボットにまかせて活人化
貴重なリソースを生産へ集中させるためには、汎用的に活用できるロボットを使った、単純作業の自動化が効果的です。食品製造ラインでは、生産品目や装置レイアウトの変更が多く、コンベアのような固定化した自動搬送装置を設置できない現場の場合は、資材の搬送作業を人手で行わなければなりません。
ブースでは、包材の搬送工程で自律走行するモバイルロボットを紹介。「モバイルロボット LDシリーズ」は、内蔵したレーザスキャナで周辺環境の情報を収集し、搬送ルートマップを自動作成。工場内のレイアウトCADデータがなくても、レイアウト変更から最短半日で自動搬送ができます。
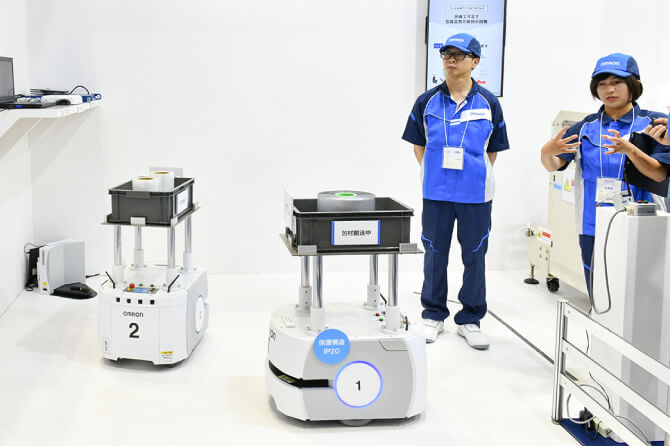
産業用ロボットの導入コストを
50%削減
また、出来上がった製品の中から良品だけを選び、箱の中に並べて詰める作業を自動化する、画像検査と産業用ロボットの組合せによるソリューションも提案しました。
食品工場へのロボットの導入では、限られたスペースに、いかに能力の高いロボットを導入できるかが、とても重要になります。ブースでは、コンベアで流れてくる製品を、「画像処理システムFHシリーズ」を活用したリアルタイム画像認識で良品だけを見分けてピッキングし、1分間に最大170個箱詰めするデモを紹介。ロボット用プログラミングソフトウェアは、ロボット制御プログラミングだけでなく、ロボットとカメラの設定を含めた動作シミュレーションも可能。ウィザード方式で、カメラまで使ったコンベアトラッキングも約10分で設定が完了します。このため、製造品目が変わっても、簡単かつ迅速に対応できます。「パラレルロボットQuattro 650」を活用し、高速化やマルチハンドで搬送能力が2倍となる場合、従来のロボット台数と設置スペースを50%削減することができます。
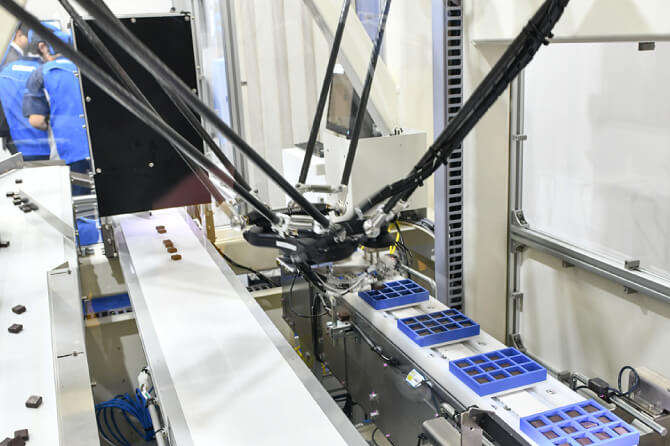
お客様の声
“ロボットの導入検討は進めているが、社内稟議を通す段階で止まってしまう。特に、ROIを明確にすることが難しく、導入効果が明確なソリューションは魅力的だ”
“ロボットハンドメーカときめ細かな連携をしながら実現したソリューションとのことで、その点を評価している。箱詰め工程、複雑な整列アプリケーションとして使えないか、相談していきたい”
省人化
全製品のトレーサビリティを確保して、
クレームの影響を最小限に
製造現場では、機械の調整や材料の仕込みのような製造に直接関わる作業だけでなく、作業の記録や報告などに手間と時間がかかっています。万一、製造した製品にクレームがあった場合は、原因究明や改善といった事後対応の作業が発生します。こうした作業も含めての省人化は、事業を円滑に進めるうえで重要な課題になっています。
ブースでは、全製品の外観検査などのデータと画像データを全数保存し、トレーサビリティを確保することで、市場からのクレームが発生した場合の影響を最小限に抑えるソリューションを提案しました。良品と不良品の違いを判別できる証拠となる生産情報が十分記録されていないと、市場に出回っている製品を全て回収しなければならない例もあります。このため、抜き取り検査の情報にとどまらず、全製品の情報を記録・保存することが重要になります。これまでは、製造スピードの速さや、記録媒体の容量が十分でなかったことから、全数の情報を保存することは困難でした。
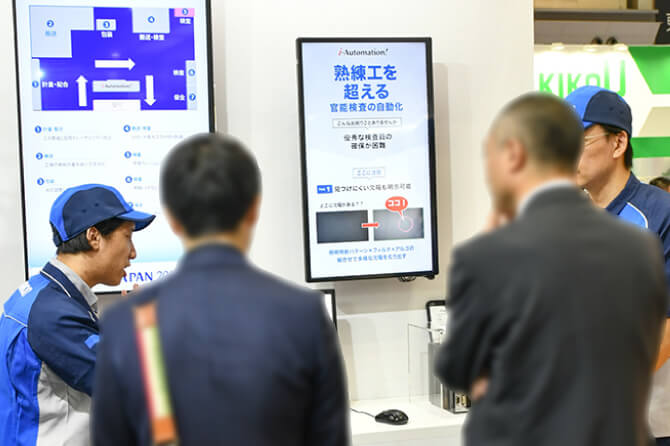
このソリューションでは、製造時の検査データやカメラで撮影した現場の画像といった、製造時の情報を紐付けて、全製品分をサーバなどへリアルタイム保存します。ロボットの制御データは「マシンオートメーションコントローラNX102データベース接続CPUユニット」、負荷が重い画像データおよび検査結果データは「画像処理システムFHシリーズ」でそれぞれ並列処理するため、画像の全数保存によるロボット動作のタクトタイムへの影響はありません*。さらに、カメラで撮影した製造時の様子や外観検査などのデータを紐付け、万一クレームが発生した時に、該当製品の情報を検索し、不良発生の可能性がある範囲を迅速に特定できます。保存した情報は、品質や製造効率をさらに高めるための知見の抽出にも活用できます。
*詳しい条件は、当社営業員までご確認ください
サーボ制御と画像検査の擦り合わせで
良品の廃棄ロスを実現
また、検査速度を高めても良品を誤って不良判定しない、廃棄ロスを最小化できるソリューションも提案しました。高速搬送される製品を画像で検査する場合、画像認識処理が追いつかず、良品でも不良と判定してしまうケースが出てきます。しかし、製造効率の観点から搬送速度を下げることもできません。
これまでは、製品をカメラの下で一時停止させ、製品の揺れが収まるのを待ってから検査をしていましたが、高速搬送時の揺れや振動を抑える制振制御と、コンベアを一時停止することなく移動しながらでも安定した検査を実現するフライングトリガ機能により、タクト短縮と安定検査を両立させました。また、視野の狭いカメラを使っても、高速搬送時の撮像ズレがなくなるため、安価な設備で高精度な検査が可能になる利点も生まれています。
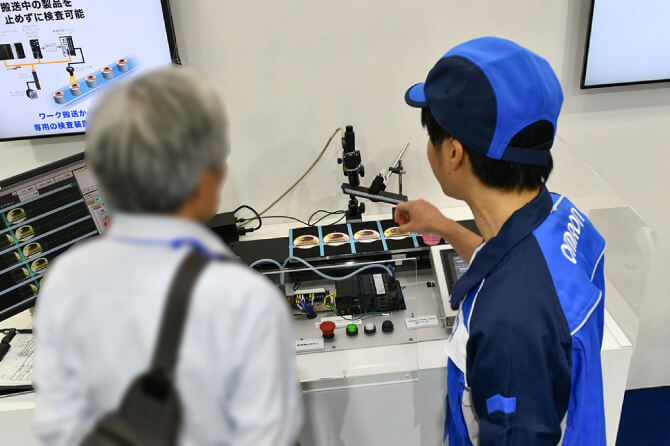
お客様の声
“ペットボトルの外観検査で、水滴や搬送中のズレで生まれる影の除去ができるかもしれないので、前向きに導入検討したい”