カーボンニュートラルテクノロジーフェア 2024 春 メディア記事
時間 空間 距離 在庫、
「All in half」で現場の生産性向上と省エネが実現
転載元:MONOist
MONOist 2024年7月8日掲載記事より転載
本記事はMONOistより許諾を得て掲載しています。
記事URL:https://monoist.itmedia.co.jp/mn/articles/2407/03/news130.html
アイティメディアにおける産業向けメディアのMONOist、EE Times Japan、EDN Japan、スマートジャパンは2024年6月3、4日の2日間にわたりライブ配信セミナー「カーボンニュートラルテクノロジーフェア 2024 春 技術革新と持続可能な未来の共存」を開催した。
本稿ではその中から、オムロンヘルスケア 生産統轄部 松阪工場 工場長の曽根直樹氏とオムロン インダストリアルオートメーションビジネスカンパニー アドバンスドソリューション事業本部 ビジネスデザイン部 GXチーフコンサルタントの高市隆一郎氏による「『すべてを半分に。』製造現場のエネルギー削減と生産性向上を両立」をテーマとした基調講演の一部を紹介する。
セミナー動画はこちら
エネルギー削減と事業成長を両立する「エネルギー生産性」という考え方
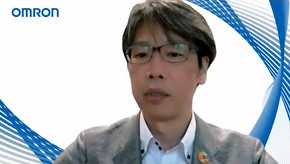
講演ではまず高市氏が脱炭素に向けた同社の基本的な考え方とアプローチの方法を説明した。オムロンでは2030年までの長期ビジョンとして「SF(Shaping The Future)2030」を掲げている。そこでは社会的インパクトが大きく、企業としての強みが生かせる「カーボンニュートラルの実現」「デジタル社会の実現」「健康寿命の延伸」の3つを社会的課題として設定した。これらの課題を解決することが、同社が成長する機会として捉え、事業部門を超えた取り組みを展開している。
このうちカーボンニュートラルの実現に向けてオムロンでは、消費するエネルギーを減らしながら事業成長を続けるという、製造業における矛盾ともいえる2つの目標の実現を目指している。その取り組みの中で、試行錯誤を繰り返しながらたどり着いたのが「エネルギー生産性」という考え方だ。
これは、分母に消費エネルギーを、分子に売上高や付加価値を置く数式で表した指標である。省エネは消費エネルギーに重点に置き進めてきたが、生産性向上に注目することで、製造現場が主役となり大きくエネルギーが減らせることになる。
「それまでエネルギー削減は環境担当、施設担当分野の仕事であり、製造現場には直接関係がないとの考えが支配的だった。それに対して、製造現場がエネルギー削減を自分事として捉えて、具体的な行動変容を起こすための指針として『All in half』(全てを半分に)というコンセプトを打ち出した。そして時間、空間、距離、在庫の4項目の半減を目指して、現場改善アイデアを引き出す取り組みをスタートさせた」(高市氏)
基板実装ラインにおける「All in half」の取り組み
その具体的な取り組みである松阪事業所(三重県松阪市)の事例を曽根氏が紹介した。松阪事業所は電子血圧計、体温計、超音波式ネブライザーなどの製品を3棟の工場棟で生産している。製造設備としてSMTライン、簡易クリーンルーム、手組工程ライン、自動加工/組立ラインなどを備える。
事業所ではカーボンニュートラルの取り組みを進めるにあたり、同社の現場データ活用サービス「i-BELT」を活用し、まず工場全体、施設設備、生産ラインの3つの階層で見える化を行い、「GHG(温室効果ガス)排出量」と「エネルギー生産性」を可視化した。そこから、エネルギーの使用箇所や設備稼働率の状況などを把握した。
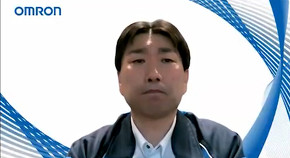
エネルギーの見える化では、分かりやすくグラフにまとめ、そこから特に生産活動を行っていないときの無駄な使用エネルギーについて注目した。エネルギー制御や運用改善により、生産に寄与していない待機電力などを抑えることで、「これ以上無理と考えていたところからさらにエネルギーを削減することができた」(曽根氏)としている。
ただ、この取り組みだけでは、エネルギー削減と既存の省エネ活動の延長線にしかすぎないことから、スローガンである「All in half」に基づき、工場が常に実施している生産性改善活動をエネルギー削減につなげることとした。
その取り組み策の1つに、最もエネルギー消費の大きい基板実装ラインの稼働率の改善がある。基板実装ラインでは高温でハンダを溶かす際に大量のエネルギーを消費するが、製品が流れていないときも一定のエネルギーを使っていたことが、見える化を通して判明した。
非生産時間の状況を現場で正しく把握し、基板の流し方などを改善することで非生産時間を短縮。生産量は1.4倍にまで拡大することができた。一方でオムロンの制御機器や技術を導入し、エネルギー制御を行うことで、非生産時間のエネルギー消費量を減らし、約20%のエネルギー削減を実現した。
これらの結果、分母、分子の両方で改善が進み、エネルギー生産性は約1.75倍、また、基板1枚当たりのGHG排出量は42.9%削減できることが分かった。
部品調達は国内近隣メーカー活用でGHG排出量や梱包資材減
さらに、血圧計の組立ラインでは省スペース化による生産性向上とGHG削減にも取り組んだ。省スペース化においては、空調電力がポイントとなった。松阪事業所では2023年実績で空調エネルギーの使用量が工場全体の4分の1にあたる500MWhを記録している。
空調を使用するスペースの延べ面積は3棟合わせて8200m2であり、1平方メートル当たり約60kWhとなる。この空調が必要な空間を削減することができればエネルギーを減らすことができることから、工場ではそれまで42m2あった血圧計組み立てラインの空間距離を半分にするなどの取り組みを同社のFA技術を駆使することなどで実施した。
その結果、ラインの長さは30m2に短縮し、省スペース化が図れ、空調エネルギーの30%削減に成功した。また、省スペース化した生産ラインは作業者の無駄な動きがなくなり、生産量は1.3倍向上した。この取り組みでエネルギー生産性は1.85倍、製品1台あたりのGHG排出量も45.9%減となっている。
さらに松阪事業所では「All in half」の考え方を部品調達にもあてはめた。これまで海外から調達していた部品を国内移管、さらに近隣のメーカーに依頼することで、海上輸送や国内輸送の距離を短縮し、部品調達に関するGHG排出量を3.4t(トン)削減するという。
この取り組みは梱包資材の削減にもつながった。例えば、血圧計の筐体を海外から調達する際は、耐久性の高い段ボールに厳重な緩衝材とともに入れて運ぶ。輸送先で開梱された段ボールは最終的にごみとして処分されるが、その量は年間90tに及んでいた。そこには一時保管するスペースや処分するコストも必要になる。
そこで松阪事業所では近隣メーカーだからこそ可能な通い箱を使った輸送を開始。さらに通い箱を現場まで持ち込むダイレクト配当を実施することで荷降ろしのための空間、時間、停滞する部品在庫を減らしエネルギー生産性が向上した上、90tの段ボール使用をなくすことに成功した。「これまで国内調達は高いという固定概念があったが、GHG排出量や廃棄物の削減、エネルギー生産性の向上に連結できる結果となった」(曽根氏)。
松阪事業所では、こうした成功事例を生かし工場全体を最適化する方針だ。また、オムロンでは幅広い製品ラインアップと高い技術力により、成功事例を積み上げて企業の生産性向上およびエネルギーの消費削減に貢献していく。