オムロン綾部工場の高精度センサ生産ラインでの、工程管理トレーサビリティ導入による生産性・品質改善と、
作業者の判断作業の負担削減による現場改善への取り組みをご紹介します。
課題
作業者の習熟度と正確な判断が支える
注文通り間違いのない、
2万品種を超える生産の維持
オムロン綾部工場では全体で2万機種を超える、高精度かつ高速な安定計測のためのセンサを製造しています。高い性能の製品をお客様に提供するために、部品や組み立てのバラつきを考慮した調整作業を生産工程の中で行うことで、品質や性能を作り込んでいます。
一部の高精度センサの生産ラインにおいては、76品種を作り分けるために最大825回/日(該当生産ラインの合計)の判断作業が必要とされ、機種ごとに組み合わせの作業指示書と製品(現物)を目視で照合確認することは作業者へ常時、緊張感を伴い、高い習熟度が要求されていました。
もしも判断ミスが発生した場合は工程の後戻りや手直しが発生し、場合によっては不良品の市場流出にもつながる恐れがあります。
また、高精度センサには厳格な輸出管理が必要な機種もあり、お客様からの注文通りの機種を100%間違いなく生産し続けることが求められていました。
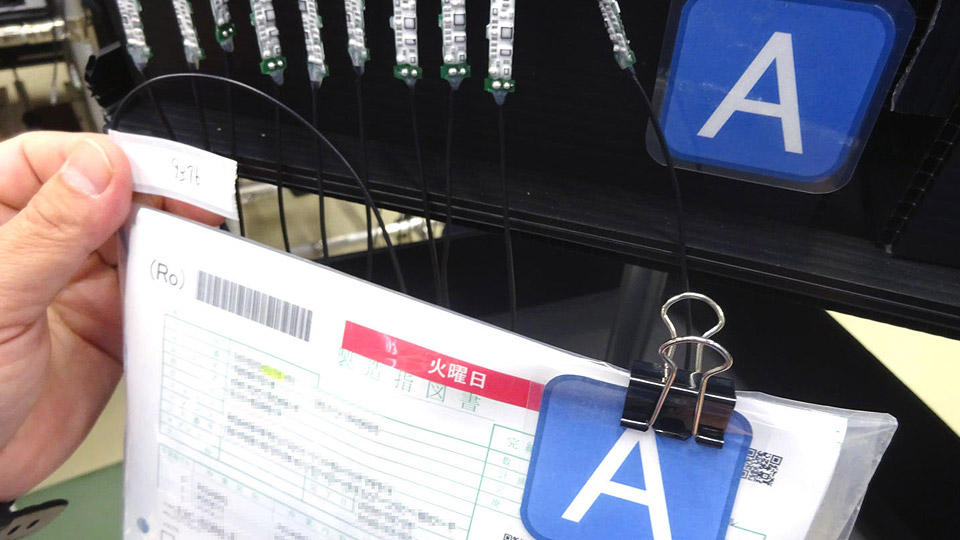
解決策
多品種少量生産での個体管理を実現
高精度センサの品質・性能の作り込みにおける課題を、トレーサビリティの導入により解決をめざしました。
製品本体と、本体に搭載するキーパーツに2次元コードを付与することでシリアル管理するシステム(2次元コードをもとにした個体管理)を導入。2次元コードを通じて製品と製造情報を瞬時に照合した結果が記録されることで、4M変動による不良流出のリスクを最小化することができます。
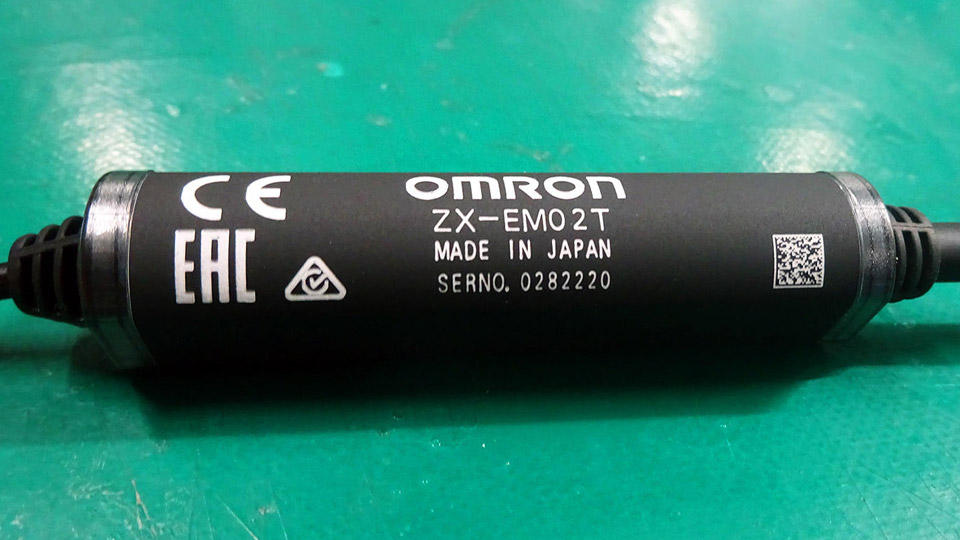
作業者の習熟を支援するデジタル作業指示
また、IoTセンサの設置により、各工程の現場データの収集・蓄積を可能にするセルラインコントロールシステム(既導入)と合わせて、不良が流出しない仕組み(不具合を残したままでは次工程に進めない)や、不具合が発生した場合には作業者へ注意喚起し、即時に不具合修正を実施する仕組みを実現します。
これにより、作業者の習熟度に関わらず安定した生産を行うことができます。
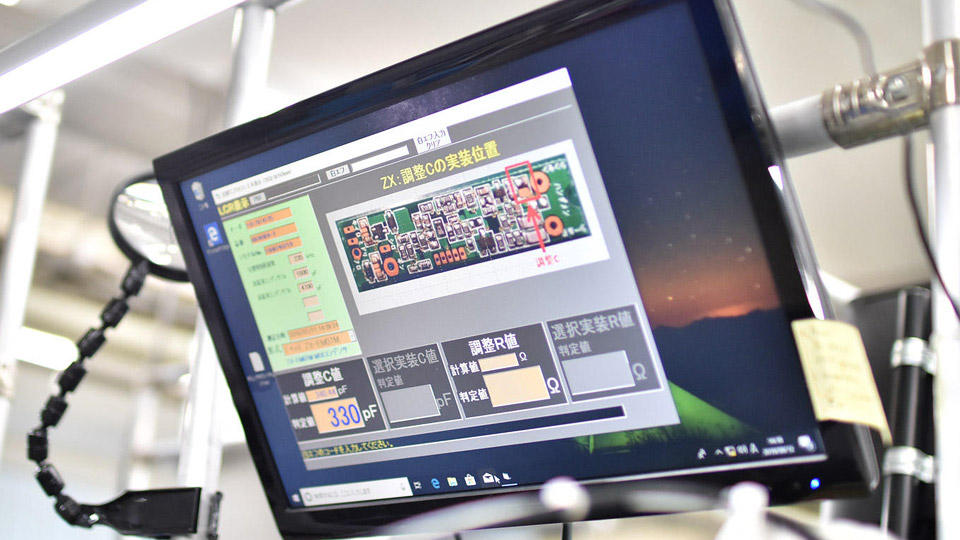
成果
工程管理トレーサビリティ導入により、品質向上と判断作業の大幅削減を実現。
人とシステムが協調する、働く喜びを感じられる現場に
人の作業を支援し、製品が作られる工程や作業内容といった製造情報も紐づけて一元管理できるシステムによって、正しく検査された製品をお客様に提供できるだけでなく、現場で働く作業者にとって、精神的・肉体的な負担であった判断作業をゼロ化し、生産性・品質の改善に加えて、作業者が安心して働ける現場づくりを実現することができました。
また、不具合で生産を止めることなく、生産リードタイムの改善を進めるシステムにまで進化させました。
高精度センサ生産ラインの判断作業合計 最大825回/日 → 0回/日
担当者の声
トレーサビリティシステムの展開と
トレース情報のさらなる拡大へ
多品種少量のセルライン生産をしている綾部工場では、人の判断に頼った工程が残っており、製造品質改善への大きな課題でした。
今回、トレーサビリティシステムによって品質や生産性改善だけでなく、人とシステムが協調する、働く喜びを感じられる生産現場の実現に取り組むことができました。別の工程の作業者の方からも横展開を希望する声が挙がっていると聞き、うれしく感じています。
今後はこのシステムの横展開に加え、部品情報の生産活用を視野に、システムの敷き詰めとトレース情報の拡大に取り組んでいきます。
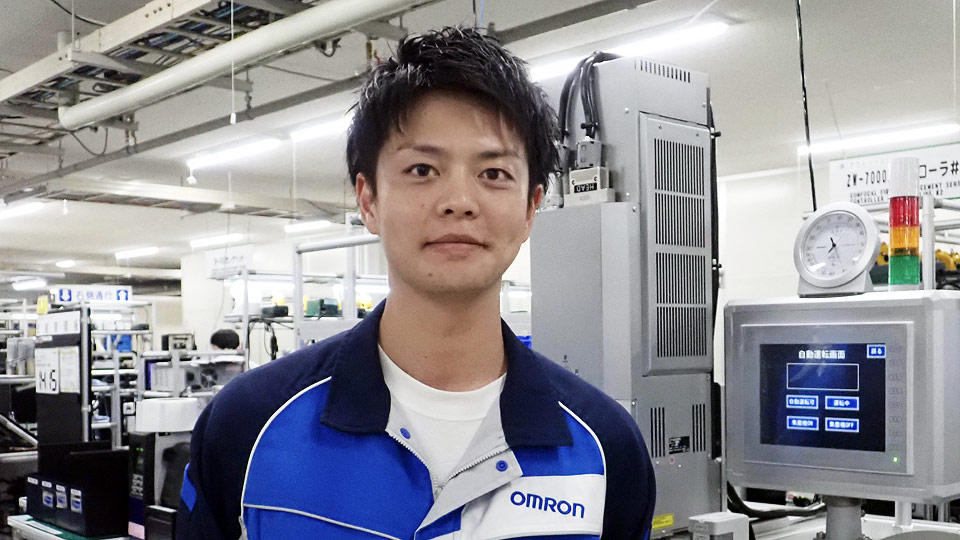
山下紘平