背景
島津儀器(蘇州)有限公司様(以下島津儀器)は、分析計測製品の世界的リーディングカンパニーである島津製作所様(以下島津製作所)の海外生産拠点の中でも最大規模を誇り、中国で販売する分析計測製品の約2割を製造する非常に重要な生産拠点です。1998年、市場ニーズに対応した価格競争力の高い分析計測製品を生産・供給する工場としてここ蘇州に設立されて以来、主に中級・汎用機種の液体クロマトグラフ質量分析計(LC-MS)や液体クロマトグラフ(LC)、紫外可視分光光度計(UV)などを製造してきました。
2023年度から始まった中期経営計画において「グローバル製造の拡大」が掲げられ、既存工場の生産能力の強化と、2024年の夏に竣工予定である第4期工場の稼働によるさらなる生産能力の増強が明確な目標として掲げられました。
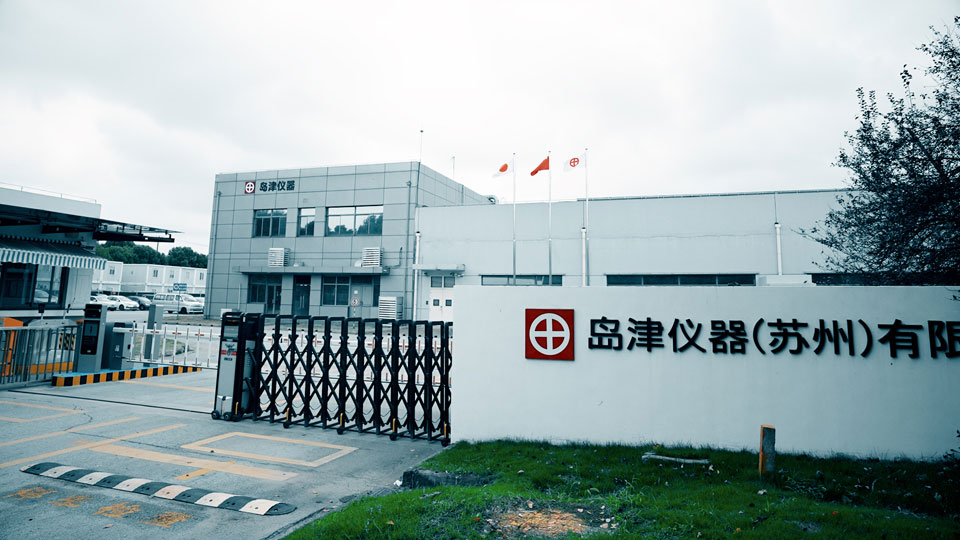
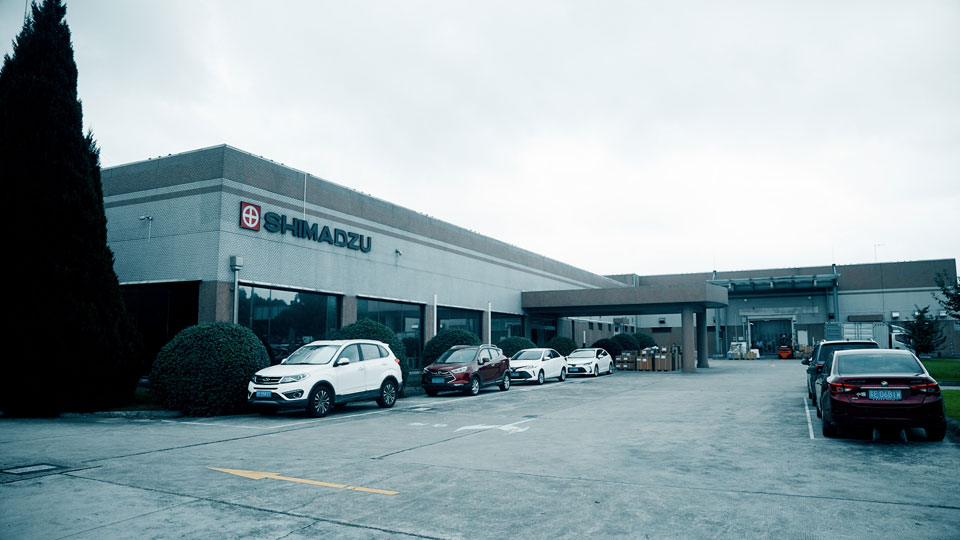
課題
既存工場の最適化とそのノウハウを水平展開した生産性の高い新規工場の稼働を実現し、市場ニーズに応える
島津儀器には、主にオンライン排ガス分析計を生産している泰山工場と、主に分光光度計を製造している華山工場の2つの工場があります。「グローバル製造の拡大」と掲げられたように、市場ニーズの高いMS(質量分析計)上位機種の生産ラインアップ拡充やそれら製品の安定的な供給を実現するためには、従来の属人的な考えから脱却し、人を増やさずリードタイムを短くして生産性を向上させることが不可欠で、以下の3つがテーマとして挙がりました。
①泰山工場の改善
②崋山工場の改善
③既存工場の改善ノウハウを活かした第4期工場のコンサルティング
①既存の泰山工場の改善
泰山工場で製造している分析計の高い市場ニーズに対応するためには、現在の18~20日という生産リードタイムを15日以下に短縮しなければなりませんでした。そのため、短縮を妨げているボトルネックを特定する必要がありました。
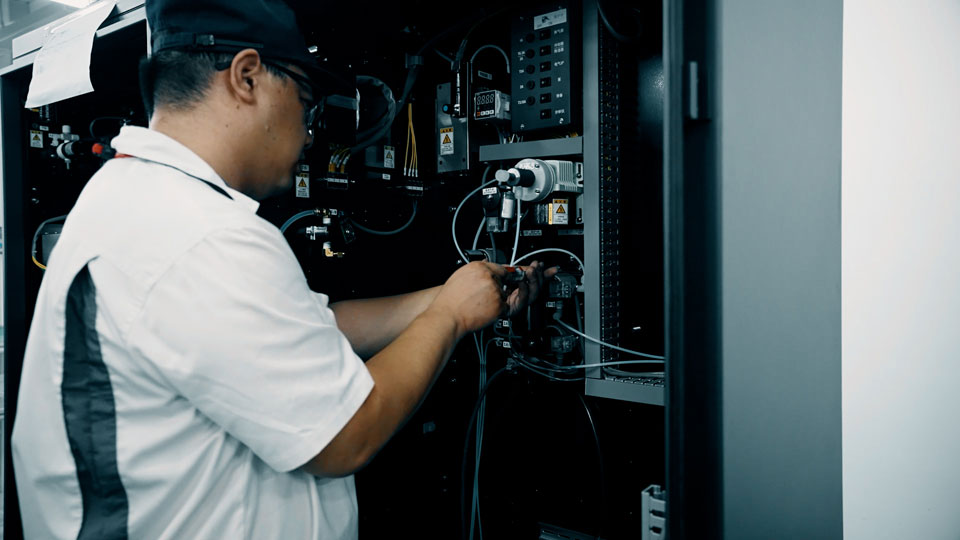
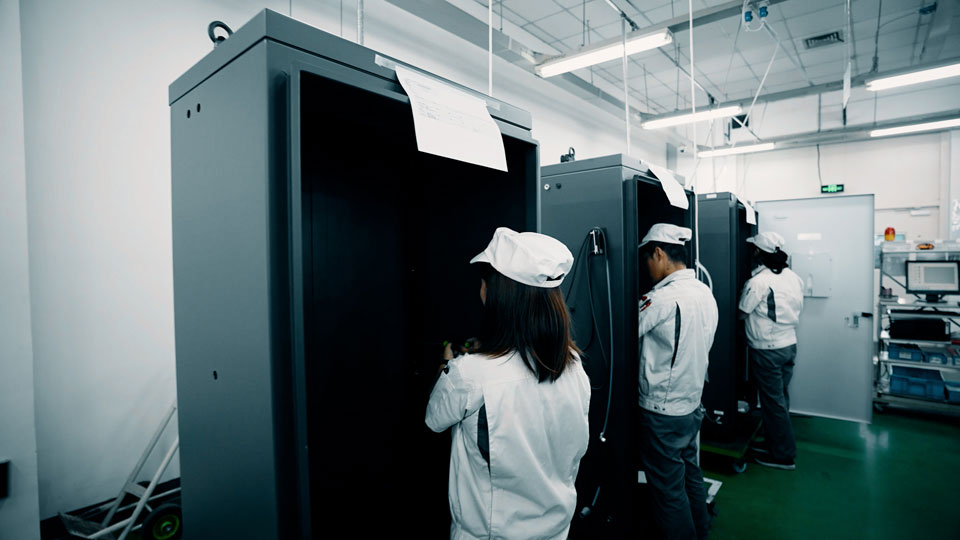
②既存の崋山工場の改善
崋山工場では分光光度計を製造していますが、今後の生産の余地を知るためにも現場の可視化や作業者の意識の改善が急務でした。
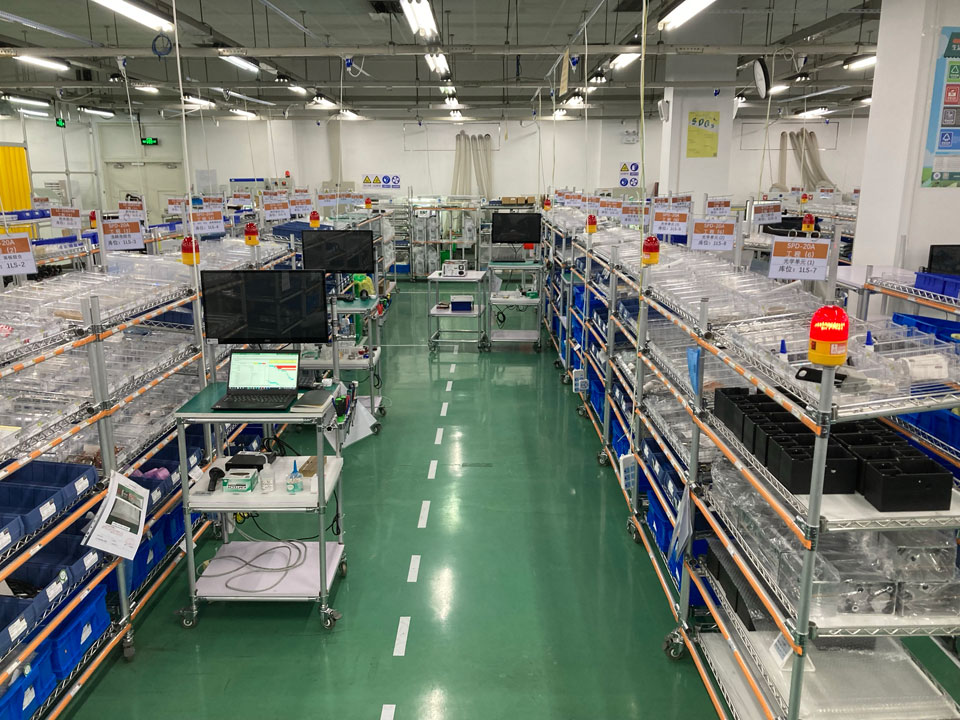
解決策
共通の認識を持ち共通の言語で語り合えるよう、IE教育を実施
島津儀器と共に課題解決に取り組むオムロンは、まずi-BELTサービスコーディネーターを島津儀器の現場に入れ、挙げられた課題の深堀を実施しました。コンサルティングで重要なのは共通の認識を持ち、共通の言語で語り合うことです。そこでオムロンは島津儀器の関係者や改善に興味を持っている方たちと同じ価値観で取り組めるよう、オムロンの生産現場の改善の理念や知識を使ったIE(インダストリアルエンジニアリング)教育を実施し、課題に対しての解決案を探りました。
①泰山工場の改善に向けた解決策
泰山工場では、工程の問題点を洗い出しそれぞれを分析しながらひとつひとつの問題を解決してきました。その中でも、サイクルタイムを計り可視化をしたところ、同じ工程でも作業者によって要する時間にバラツキがあることがわかり、特に検査工程が大きなボトルネックになっていることが明らかになりました。
検査工程では、従来は画面の数字を確認しOKかNGかを判断して、OKなら次の操作、NGなら相応の対応を取るというように、人によって判断時間に差が出る検査方法の半分を、バーコードだけで自動検査できるシステムに変える提案を行いました。
その他、改善の余地があった調達プロセスの見直しによる調達時間短縮、中間品生産の提案なども合わせて行うことで、リードタイムは15日まで短縮できることを試算しました。
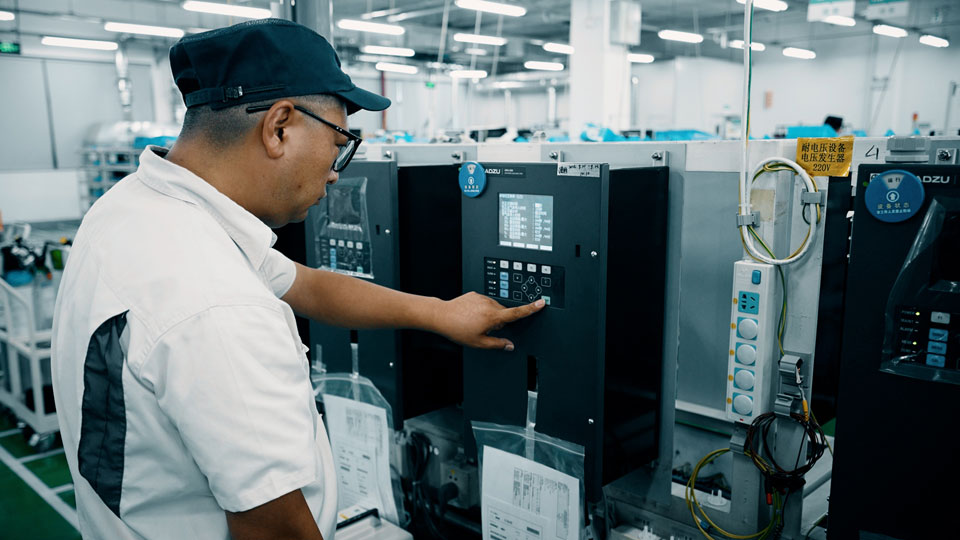
②崋山工場の改善に向けた解決策
崋山工場では、製造ラインの進捗管理、現品管理、余力管理にフォーカスして現状のデータをフル活用した分析を行いました。実際に現場が今どうなっているかを徹底的に可視化することで、目指す姿を明確にし、どのように改善に取り組むべきかを検討しました。
可視化されたデータからは、工程・位置・作業者が固定化されていないことが生産性向上の妨げとなっていることがわかり、固定化するために一個流し生産方式への変更を提案し、PDCAを回すワークショップを随時実施しながら作業者の意識改善も進めてきました。
成果
当初の目標として試算した数字はあくまでも理論上試算した数字であったものの、泰山工場で取り組んだNSA-3090(分析計)のラインについては製造リードタイムが18~20日であったところを試算通りの15日に短縮することができました。
華山工場で取り組んだSPD-20A(検査機器)のラインに関しては、工数が標準化に近づき作業者による工数変化を抑えることができた結果、12.5%もの生産性向上を実現しました。
このようにIE教育やワークショップを通じ、島津儀器とオムロンが一緒に課題解決に取り組み、共創によって得られた「改善のノウハウ」と「自律的な行動ができる意識」を、2024年の夏から稼働が予定される第4期工場へのスムーズな水平展開につなげていくことが期待されています。
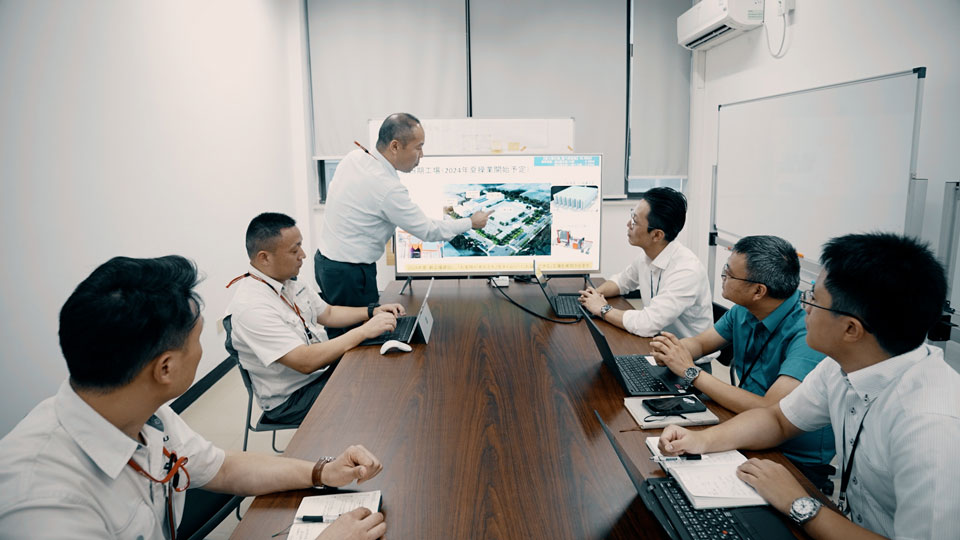
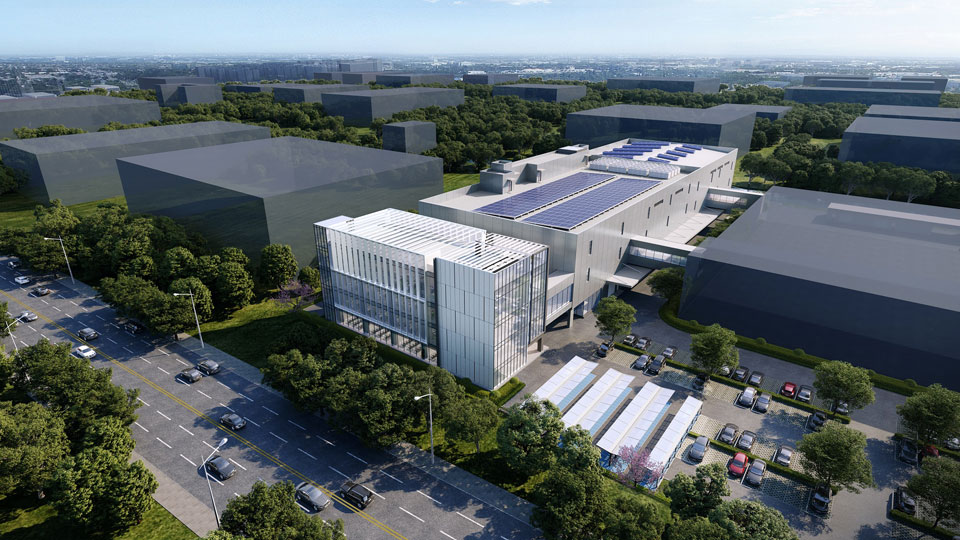
お客様の声
共創関係の中で的確にコンサルティングしていただきました
オムロンさんとの共創関係の中で、的確にコンサルティングしていただきました。
島津儀器の蘇州工場では非常にたくさんの分析計測製品を作っていますが、私たちが今回の改善の意義や考え方を理解していなければ、この後の水平展開はできません。今回オムロンさんと一緒に教育を進めることで、自分たちで理解することができたのがとてもよかったと思っています。
2つの工場での改善に新しい取り組みも加えながら属人化を脱却し、人員1.5倍で5年後の売上2倍を目指しますが、オムロンさんと一緒ならできると確信しています。
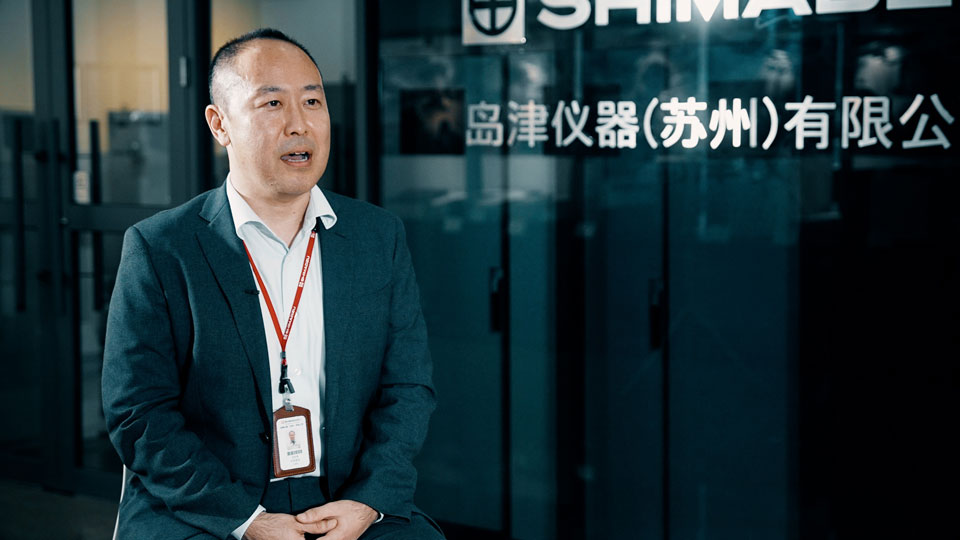
河村 政宏様