はんだ付けの自動化方法とは?ロボットが課題を解決
はんだ付けは、電気製品の製造に欠かせない工程です。一方で技術者の育成には時間がかかり、人材の確保が課題でもあります。従来人手に頼っていたはんだ付けですが、技術の進化により熟練技術者の技を自動化することができるようになりました。はんだ付けを自動化することで、高いレベルの作業と品質を再現でき、無駄を排した高効率の製造を実現できます。
はんだ付けの課題
はんだ付けは製造過程の中でも特殊な工程で、認定を受けた一部の技術者にしかできない作業です。加えて、近年は部品の小型化などで、はんだ付けには一層高い精度が求められています。一方、製造業界の慢性的な人手不足も影響し、ただでさえ技術習得には時間がかかる中、匠の技の継承者不在という問題が発生しています。これまで蓄積した熟練技術者の技術を継承できなくなる事態は企業にとって大きな損失といえます。
はんだ付けの自動化方法
これまで認定を受けた技術者・熟練技術者にしかできなかったはんだ付けですが、近年自動化技術が向上しています。
はんだ付けの自動化には、マウンターによる部品の実装や専用機など、様々なレベルや方法があります。
従来は専用機が多く使用されてきました。専用機ははんだ付けに特化した機械で、ピッキングからはんだ付けまでを自動で行うことができる工作機械です。作業の高速化が可能で、無人化、大量生産に向いています。一方で生産する製品が変わると、機械自体を交換する必要があるため、多品種の生産には向いていません。
最近では、産業用ロボットによる作業自動化も進んでいます。近年の産業用ロボットの進化はめざましく、機械には難しいとされてきた、人の経験値に依存するような感覚的な作業も高レベルで再現できるようになっています。産業用ロボットのアームにはんだごてを取り付けることで、さまざまなはんだ付けを自動で行うことができます。ロボットには「スカラロボット」と「協働ロボット」の2種類があります。
近年登場した協働ロボットは、アームの先端にエンドエフェクタを取り付けて使用します。エンドエフェクタにはさまざまな作業に特化した製品が揃っており、はんだ付け用のエンドエフェクタを取り付けることで、はんだ付けに適用できます。さらに協働ロボットは、人と一緒に作業できることも特筆すべき点の1つです。一般的に産業用ロボットは、安全対策のため柵で人と作業エリアを分けた配置が必要になります。一方、協働ロボットは、何かに触れると即座に動作を停止するなど、高い安全性を備えています。安全柵が不要で配置の自由度が高くスペースをとらないため、人のいた場所に代替として1台から導入することが可能です。また、スカラロボットよりも、アームの動作角度を柔軟に調節できることから汎用性が高く、作業をプログラムするティーチングも容易なため、多品種少量生産の現場に適しています。
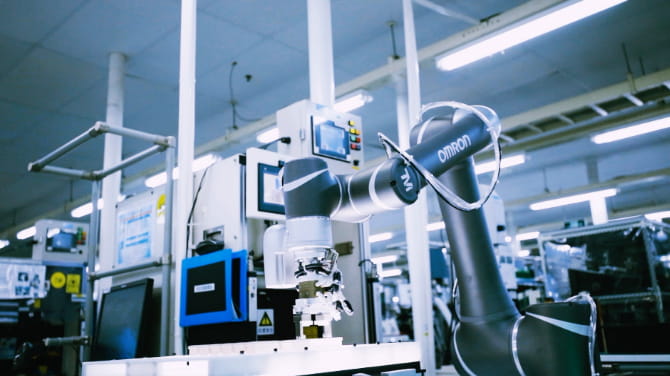
こうした特徴を活かし、自社の製造ラインに合わせた方法を選択することで、これまで以上に生産効率を上げることが可能になります。
ロボットによるはんだ付け自動化のメリット
はんだ付けをロボットで自動化するメリットは、部品をつかみながら角度を調整するなど、専用機では難しい高度作業を自動化できることです。また自動機に乗らない大型部品のはんだ付けも、ロボットを導入することで可能になります。さらに、近年のロボットはティーチングもタブレットを使って直感的な操作が可能になるなど、熟練した技術者でなくても取り扱うことができるようになっています。またロボットの導入にかかる費用も重要な検討課題となりますが、スカラロボットは、産業用ロボットの中では比較的安価なため、導入コストを抑えられることもメリットです。
はんだ付け作業の自動化は、ロボット単体で使用することもできますが、他のロボットと組み合わせることで、より複雑な作業の自動化も可能です。例えば自律走行搬送ロボット(AMR)をはんだ付け工程に組み込むことで、はんだ付けに必要な土台部品や、組み付ける部品の供給搬送まで自動化することができます。
さらに、別々な作業を割り振った協働ロボットを複数台インテグレートすることで、より生産性を上げることも可能です。例えばピックアンドプレースに協働ロボットを導入することで、部品をはんだ付けラインに置く作業まで自動化することもできるのです。
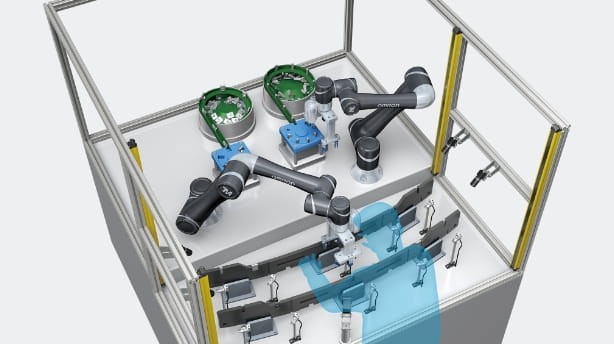
このようにロボットの導入は、人材不足を補い、高い品質で安定した製品の生産に寄与します。昨今は製品ニーズが多様化し、製造業には多品種少量生産への対応が求められます。汎用性の高い協働ロボットは、多品種展開や、急な製品仕様の変更にも柔軟に対応できます。
ロボット導入ステップ
では実際にロボットを導入するには何から始めたらよいのでしょうか。まずロボットが「何ができるか」を知り、次に「そのためにはどういう手順が必要か」を検討するというステップで進めます。
検討段階
まずは各ロボットがどのような機能・特長を持つのかを調べます。カタログなどの資料を読んで概要をつかみ、さらに体験会やセミナに参加することで、各ロボットの導入効果に対する理解を深めることができます。
国内4ヵ所に拠点を持つオムロンの「オートメーションセンタ」では、現場で扱っている実際のワークを持ち込み、実機で動作を試すことができます。
導入段階
導入イメージを固めたら、具体的な導入計画をまとめます。
社内にロボット導入技術者が不在の場合、導入にはロボットSIerが必要となります。 SIerの支援を受けながら、現場にロボットを導入し、動作を確認します。オムロンでは地域や自動化作業内容に合わせたSIerと連携し現場の状況をヒアリングした上で、具体的な設計とシステム構築支援を行っています。
運用段階
導入を終え、運用が始まった後でも、より大きな効果を得るためには活用法を逐次ブラッシュアップしていくことが重要です。またロボットの運用には安全教育が欠かせません。オムロンでは、安全教育やロボットのプログラミングなどのセミナコースを用意しています。
オムロンでは、ロボット本体に加え、はんだ付けに必要なロボットハンド(エンドエフェクタ)や、安全機器、ラインに必要な制御機器を幅広く取り揃えており、ライン全体の自動化を支援します。