製造現場でDXが推進される理由
製造業DXに期待を集めるロボットの事例
製造業の現場では、製品の多様化や人材の確保、密集作業の解消など、さまざまな課題が顕在化しています。それらを解決するために、DXの推進、中でもロボットの活用に期待が集まっています。
ここでは、製造現場でDXが必要とされる理由と共に、DX推進において重要な役割を持つロボットについて解説します。また、ロボット導入による課題解決事例についてもご紹介します。
製造の現場でDXが必要とされる理由
製造業の現場では近年DX推進に注目が集まっていますが、まずは製造現場でDXが必要とされる理由について解説します。
1.製品の多様化による製品ライフサイクルの短期化への対応
従来の日本では、他の人と同じ製品、安価で経済的な製品を求める傾向が強くありました。しかし、経済産業省の消費インテリジェンス研究会が平成29年に発行した報告書によると、消費者は近年、「自分に合っているかどうか」を重視する傾向が強くなっています。
消費者の趣味趣向が多様化すると、従来から広く行われていた少品種大量生産から、多品種少量生産を実現できる製造工程の構築が重要になります。
また、グローバル化が進み海外製品が市場に入ることによって、さまざまな業界で競争が激化しています。競合各社が次々と新製品を発売するため、対抗するべく新たな製品を市場に投入する必要があり、一つの製品の寿命、ライフサイクルの短期化が進んでいます。
製造現場を自動化し、生産管理に必要なデータをリアルタイムに取得することで、多品種少量・変種変量生産であっても、生産計画を精緻に立てることができるようになります。
2.人件費の高騰に対応する人作業代替ニーズの高まり
日本では少子高齢化が進み、労働力人口の減少が顕著です。また、フリーランスや副業などさまざまな働き方が受け入れられるようになり、労働形態の多様化が進んでいます。
製造業では、熟練作業員の高齢化・退職という状況もある中で、新たな人材を確保し一定の技能レベルまで教育するには多くのコストがかかります。また、海外生産をする場合でも現地の経済成長による人件費の高騰が多くの製造業にとって課題となっています。
人件費を削減する案の一つとして、ロボットの導入による人作業の代替や補助が期待されます。
3.感染症の蔓延による密集作業のリスク対応
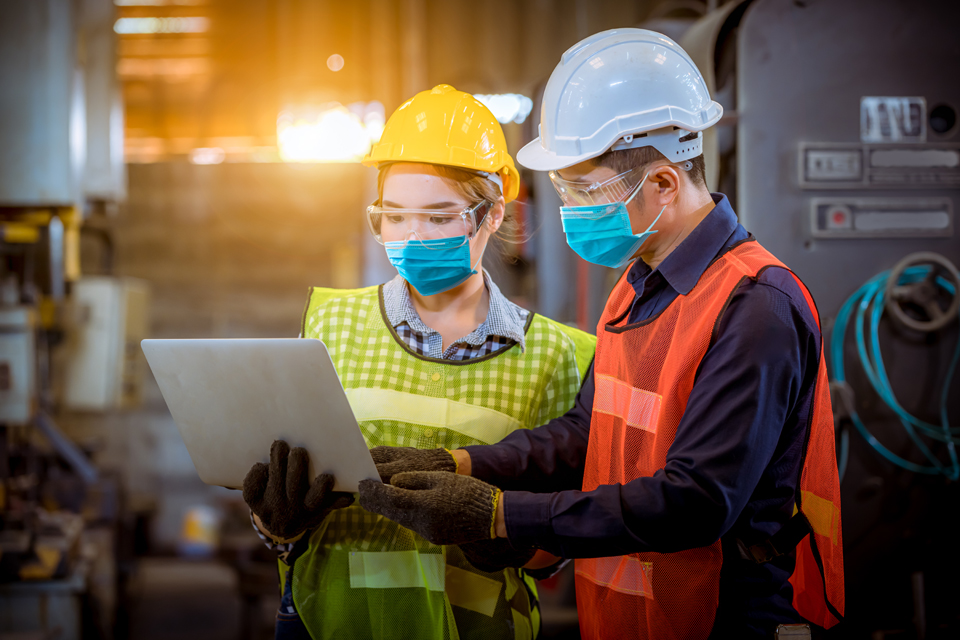
2020年春以降に蔓延した新型コロナウイルス感染症の影響で、人が密集した製造ラインは集団感染の可能性が高く、操業停止など生産活動上のリスクとみなされるようになりました。その結果、ライン省人化の検討が進められています。
製造工程から人の介在を減らすには、現場人作業の代替としてロボットを導入する方法や、生産情報・業務情報をデジタル化して拠点・工場間で状況をリアルタイムに把握できる仕組みが有効です。 また、点検や修理などの管理もリモートで実施できるようになっています。
4.グローバルでの製造品質標準化
販売地域の拡大や製造原価低減のため、日本企業がグローバルに生産拠点を置く機会も増えています。現地生産では一般的に、日本の生産工場をマザー工場として類似の製造ラインを構築します。しかし、国ごとの労働慣習や環境の違いがあり、日本と同様の製造品質を担保することは困難です。
品質の標準化を進めるためには、ばらつきが生じやすい作業の自動化を進める必要があります。
DX推進による製造自動化が課題解決のカギに
ここまで、多くの製造業が現場で抱えている4つの課題について解説しました。いずれの課題も、製造作業を「人」が行うために発生する「ムリ・ムダ・ムラ」をなくすことで解消できるものです。 まずはできる範囲で現場の自動化を進め、ゆくゆくはデータ活用・連携などより高度なデジタル化を進めることで、製造業が直面している課題の解決に繋がります。
製造業のDX推進で期待を集めるロボット 導入のメリットとは
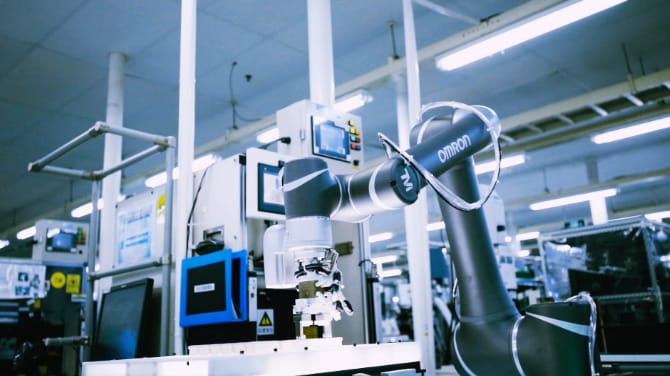
製造ラインの自動化にあたっては、ロボットの活用が注目を集めています。ロボット導入により、製造現場では以下のようなメリットがあります。
1.多品種少量生産、変種変量生産への対応
協働ロボットの登場により、従来自動化の難しかった多品種少量生産や変種変量生産の製造現場においても、ロボットを用いた自動化が可能になりました。
従来自動化に使用されてきた産業用ロボットは、安全柵など固定の設備が必要で 、工事の工数や費用がかさむことから、多品種少量生産への対応は難しい状況でした。一方、協働ロボットは固定設備が不要のため、工程変更に柔軟に対応できます。 また、人と同じ環境で稼働できることから、人作業の補助や一部分の代替を通じた工程効率化も可能です。
2.人しかできなかった作業の代替
製造工程には、人の目と指先の感覚に頼った工程や、熟練した技術の求められる工程が多くあります。近年、ロボット技術の進歩により、従来はロボットで代替不可能であった繊細な工程がロボットで再現可能になっています。人間の目の代わりとなるビジョン機能を搭載し、指先のように圧力を感知する力覚センサを活用したロボットであれば、繊細な作業を人の代わりにできます。
3.作業者によるばらつきのない品質平準化
人作業では、作業者による品質ばらつきが発生します。人作業の代替として 工程にロボットを導入することで、作業者によるばらつきを削減でき、品質の平準化を実現できます。また、製造工程だけでなく検査工程についてもロボットが活用できます。画像認識技術の高度化により、ロボットで高精度な検査が実現できるようになりました。
ロボットの導入による製造業のDX推進事例
ロボットの更なる機能進化により、これまで解決が困難と思われていた製造ラインの課題を解決できる可能性があります。実際にロボットを導入することで課題を解消した、製造業のDX推進事例を3つ紹介します。
事例1:頻繁に作業内容や装置レイアウトが変わる多品種少量生産ラインの省人化対応
数時間ごとに稼働する工程が変更されるセル生産の工程において、人作業の自動化を検討した例です。 頻繁な工程変更へ対応するため、ロボットハンドの付け替えなど多用途に対応できる協働ロボットを導入し、自動化を実現しました。
また、組立工程だけでなく搬送工程も自動化し、頻繁な段取り替えによる作業ミスが生じないようにしました。搬送工程には、柔軟なライン変更に対応できる搬送ロボットであるAMR(自律走行搬送ロボット)を導入しました。AMRは障害物を認識して回避する、自律走行が可能な搬送ロボットです。AGV(無人搬送車)と異なり走行用のレール敷設が不要なため、柔軟な搬送経路対応が可能です。
協働ロボットとAMRを導入した結果、作業者への負担が減り、ES(従業員満足度)向上に繋がりました。さらに、投資回収期間も短縮できました。
事例2:人とロボットの協働による密な作業環境の解消
協働ロボットやAMRは人と同じ環境で運用可能であることから、Withコロナ対応など、人の多い現場の自動化に適しています。産業用ロボットは、設置に工数・工事費用がかかりますが、協働ロボットであれば、現状作業者のいるラインに対して徐々に作業者の代替として導入し、大幅な変更をせずに自動化を進められます。
動画:ロボットを活用してソーシャルディスタンスを保った生産現場への提案事例3:人の感覚に頼らない品質検査の平準化
製造現場における検査工程は、出荷前の最後のゲートであり、出荷品質を確保するために重要な工程です。検査工程は作業者の感覚に頼る部分が大きく、熟練作業者への属人化や、作業者の教育に時間がかかる点が課題となっています。
この事例では、ロボットと照明・カメラ・画像処理システムを組み合わせることにより、検査工程を自動化しました。 人による検査では、品質を優先するために判定基準内のバラつきを過剰に判定してしまう「過検出」が発生するため、正常判定率は80%程度でした。ロボットがAIでばらつきをパターン化・定量化することで、正常判定率は100%に向上し、品質の安定化に繋げました。また、検査時間の36%短縮を実現しました。
オムロンは、製造現場の課題を解決するためのDX推進に活用できる協働ロボット*や自動搬送モバイルロボットに加え、周辺機器や安全機器などのさまざまな制御機器を取り揃えており、ライン全体の自動化をご支援します。
- *オムロンは、「人と機械の新しい協調」を実現するロボットとして、協働ロボットの商品名称を「協調ロボット」としています