工場自動化のカギ、AGV(無人搬送車)とは?
導入メリットやAMRとの違いを解説
工場の生産性を高める上で、工場内で使用する資材・部品や、仕掛品・完成品を運ぶ搬送の効率化は、ますます重要になっています。ここでは、工場自動化のカギを握る、AGV(無人搬送車)の最新技術と導入のメリットなどについて解説します。
AGVとは工場内のモノの搬送を自動化し生産性を向上
AGV(Automatic Guided Vehicle)とは、工場や倉庫などの中でモノを運ぶ、無人搬送車もしくは無人搬送ロボットのことです。製造ライン上の工程間や倉庫と製造ラインの間をつなぎ、モノの搬送を自動化して、工場内で作業する人を支援することがAGVの仕事です。
製造ライン上の各工程では、前の工程から仕掛品を受け取り、さまざまな資材・部品、工具、計測器などを使って作業し、完成品を次の工程に送っています。工場内では、多様なモノが、常に複雑に行き交っていますが、モノの搬送を人手で行っている現場は、作業を中断して搬送に時間を割くことで、製造ライン全体の生産性を低下させている可能性が高いのです。1つの工程の中断は、前後の工程の停滞を招き、細かな停滞が蓄積して大きな生産性の低下につながってしまいます。
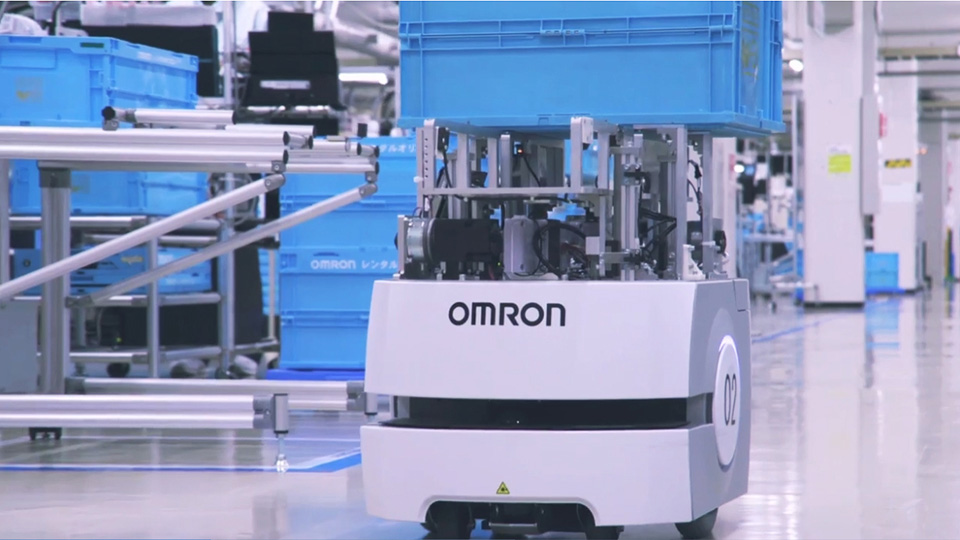
1990年代、こうした点に気づいた企業がAGVを導入し、工場の製造ライン全体の生産性を高める取り組みを始めました。モノの搬送を自動化することで、人はより付加価値の高い高性能な製造装置や工作機の操作、さらには繊細で複雑な組み立て作業などに時間を割り当てるようになりました。
AGVの課題
近年では、収益性の高い製品をタイムリーに生産していく多品種少量生産(変種変量生産)に対応したラインが盛んに構築されています。競争力の高い製造業企業の経営に欠かせない多品種少量生産ですが、AGVによる工場内搬送の自動化には限界があります。
多品種少量生産の製造ラインでは、各工程で生産する製品の種類が頻繁に変更されます。生産する製品の変更に応じて、各工程で使用する資材・部品、工具を入れ替える作業=段取り換え作業が必要になります。また、各工程の作業時間も変わってくるため、物資の補充や工程を終えた仕掛品を搬出するタイミングも変わってきます。工程の順路変更がある場合、仕掛品の搬送経路自体が変わる可能性もあります。
つまり、多品種少量生産現場における搬送工程は、ただ単に自動化するだけではなく、必要な時に、必要とする場所に、必要な量のモノを送り届ける、Just in Time(JIT)での自動搬送が求められるのです。
AGVは、多品種少量生産で求められる柔軟性の高い自動搬送を実現することが困難でした。AGVはモノを動かす始点と終点をあらかじめ決めておき、磁気テープなどのガイドラインを引いて、その上だけを走行する仕組みです。この方法では経路が引かれていない場所にモノを届けることはできず、走行経路を変えるには設備の変更が必要になるためです。
より柔軟な搬送を可能にするAGVの進化型、AMR
こうした課題を解決するために登場したのが、AGVの進化型と呼べるAMR(Autonomous Mobile Robot:自律走行搬送ロボット)です。AMRは、制御システムがその都度指定する始点と終点の間を、自ら最適経路を判断しながら走行します。走行中には、センサを使って周囲にあるモノや人の位置を把握し、安全で効率的なルートを算出して自律走行します。さらにAMRでは、障害物や人がいる場合には迂回・停止する機能も備えています。このため、ガイドラインやレールの設置は不要であり、作業者がいる通路を、安全に移動することが可能です。既存の製造ラインにもレイアウト変更なしで導入することもできます。

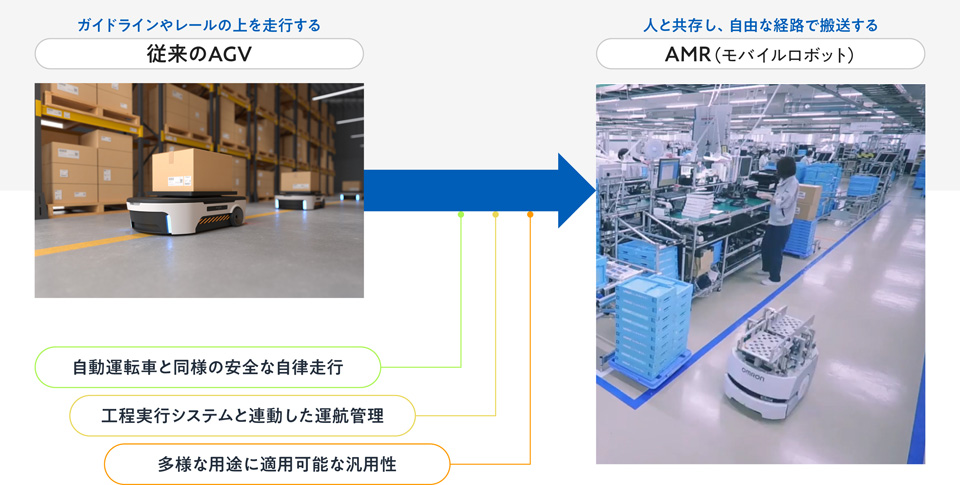
AGVでの搬送は、決められた場所の間を、決められたスケジュールに沿って担っていました。これに対し、AMRの搬送は、荷物を必要なタイミングで届けることができ、搬送経路の自由度の高さと、運行スケジュールの柔軟性から、理想的なJust in Time搬送が可能になります。
また、AMRは、複数台のAMRの動きや、MES(Manufacturing Execution System:工程実行システム)から得た周辺設備の制御情報を加味し、ムダな待ち時間を生まない効率的な運行管理を実現できます。近年では、保有しているAMRの稼働率を高め、しかも最短経路かつエネルギー効率の高い経路で運行させるような高度な管理も可能になってきています。
>AGVとAMRをそれぞれ導入するメリット
AGVやAMRは、製造ラインの生産性を高めるうえで、欠かせない設備になりました。ここでもう一度、AGVとAMRに共通する導入メリットと、AMR固有の導入メリットを整理してみましょう。
まずは、AGVとAMRに共通するメリットです。
低付加価値な搬送作業からの人の解放
搬送作業から解放した人員を高付加価値な作業へと振り当てることで、生産性向上や高品質化につながります。
少品種大量生産の現場でのJust in Timeでの搬送実現
MESと連動させて、現場の状況に応じてAGVもしくはAMRを運用することで、Just in Timeでの搬送が実現します。少品種大量生産の現場ならば、従来のAGVでもJust in Timeでの搬送に対応できます。
搬送工程におけるヒューマンエラー削減や身体的負荷の低減
部品・材料や工具などの搬送を自動化することで、ヒューマンエラーによる運び間違いなどのミスを削減できます。さらに、搬送作業における作業員の身体的な負荷軽減にも繋がります。
次に、AMR固有のメリットを挙げます。
多品種少量生産(変種変量生産)でのJust in Timeの実現
搬送経路の自由度が高いAMRならば、多品種少量生産の現場でも、MESの情報を活用し、複数台のAMRや周辺の付帯設備と連動制御させることで、効率的な搬送が可能になります。
多目的利用による稼働率(投資対効果)向上
AMRは、走行経路の自由度が高く、多目的に利用して稼働率を向上できます。例えば、製造ラインが稼働している時間帯には物資の搬送に活用し、ラインが停止している時間帯には紫外線殺菌装置を載せて工場内を循環させ衛生的な製造環境の維持に活用するという方法があります。
人のいる作業現場での搬送自動化
AMRは、センサなどを活用し人を安全に回避するため、人が通る通路でも動かすことができます。AMRの導入に際してAMR専用の通路を用意する必要はなく、導入時や、導入後のライン変更に伴う設備変更も容易です。
AMRの活用事例
現在の生産ラインを変えずに自動搬送を実現した事例
オムロン草津工場/綾部工場
オムロンは、経営課題である人材不足や多品種少量生産に対応するため、搬送作業の大半をAMRにまかせることで、AGVでは実現が難しい小ロットで細かい搬送を自動化し、劇的な生産効率の向上に成功しました。走行経路は、導入ルートを走らせスキャンすることで、AMRが走行環境のデジタルマップを自動作成します。既存の設備配置は変えず、レイアウトも変更なしでオムロンのAMRであるモバイルロボットを導入。搬送リードタイムの短縮と作業者の精神的肉体的なストレスの低減にもつながりました。 導入事例:オムロン草津工場・綾部工場『「人材不足」「多品種少量生産への対応」という課題をモバイルロボットで解決』
アパレル業界での工場内搬送自動化でコスト競争力を向上した事例
株式会社センチュリーテクノコア様
紳士服メーカであるセンチュリーテクノコア様は、工場の増築に伴う工場内での搬送頻度の増大による生産効率の低下を、モバイルロボットの導入によって解消しました。リフト制御と運行管理を連動させることで、1階と2階の移動も自動化しています。同社では、2台のモバイルロボットを導入し、それらを一括管理することで、効率的な運用を実現しています。これによって、「国内生産」の弱点であるコスト競争力を補っています。 導入事例:株式会社センチュリーテクノコア様『自動搬送システムの実現で生産能率向上』
自律走行型の風量測定ロボットで、空調性能試験の工数を従来比75%削減
三機工業株式会社様
ビルなどの空調設備を設計・施工している三機工業様では、モバイルロボットを使って、施主に引き渡す前の検査を自動化しました。超高層ビルなど、大規模案件では、1000箇所を超える検査すべき場所があります。建物の図面データを基にモバイルロボットを動かして、送風口の直下に測定器を運び、空調の風量を自動測定しています。これによって、従来比75%の工数を削減しました。
オムロンでは、人の代わりに資材や部品を運搬し、生産性向上に貢献するAMRを提供しています。工場のレイアウトを変えることなく安全な自律走行を実現する機能や、複数台のAMRの一括管理やMESとの連携によってライン全体の生産性を向上させる機能を備えています。
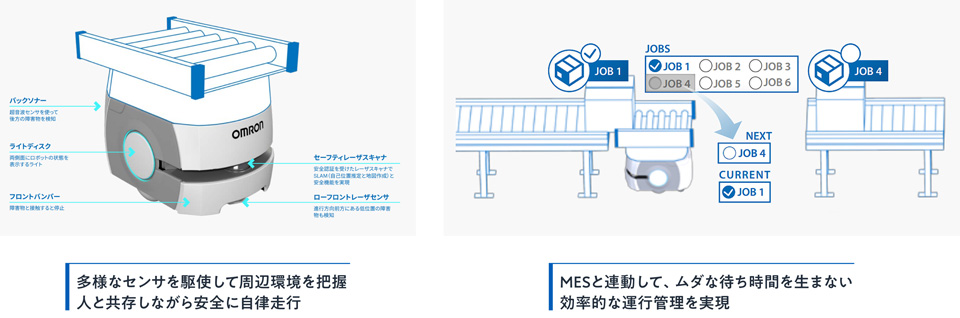
また、AMR以外にも協働ロボットや各種制御機器を取り揃えており、ライン全体の自動化をご支援します。