綾部工場
自働化とスキルレス化を要所に使い
現場作業者の力を
最大限まで引き出す
綾部工場では、数cmのセンサから数m規模の検査装置まで、1カ所の工場で約2万品種を作る超多品種少量生産を行っています。アセンブリ工程が中心であり、製品設計と工程設計の作業を擦り合わせることによって、高品質な製品を高効率で生産しています。生産ライン内では、搬送など付加価値を生みにくい作業を自働化して、現場作業者の負荷を軽減しています。さらに、生産現場から得たデータを解析して、工程間に潜む生産効率や品質に及ぼす要因を洗い出して改善点を見える化。これまで経験豊富な熟練者の知見やスキルが求められた工程の高度な自働化によるスキルレスを実現しました。
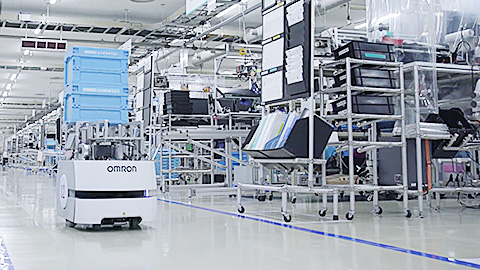
モバイルロボットで部品を自働搬送
人は製品価値を
向上させる作業に注力
セル生産による多品種少量生産を効率化するためには、必要な部品を、必要な時に、必要とする場所へ、確実に送り届ける必要があります。ただし、これは重要な作業ではありますが、製品価値の向上に直接つながる作業ではありません。綾部工場では、自律走行するモバイルロボットを導入し、運搬作業を自働化しました。人とロボットが協調する安全な搬送が構築でき、レイアウト変更にも柔軟に対応できます。これによって現場作業員は、付加価値の高い仕事に注力でき、リードタイムの短縮と仕掛在庫の削減を実現しました。
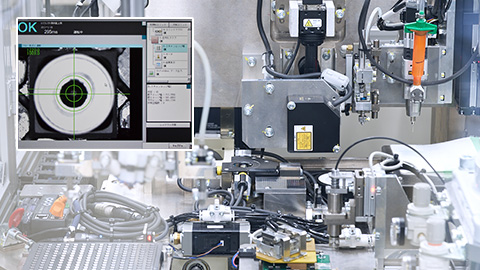
光学素子アライメント装置の
予知保全
最適タイミングでの保守を可能に
ファイバセンサの生産でのレンズ位置合わせは、投光性能を決める重要な工程です。綾部工場では、画像データや波形のようなプロセスデータをIoTによって収集してビッグデータ化。これを解析して位置のずれを自動補正し、品質を安定化。また、組立用設備での故障発生や不良発生の予兆を、AIコントローラによって事前察知して対処する予知保全を実践。従来行ってきた定期保全のような稼働時間で管理する保全を、設備の状態を管理して必要性が生じた場合に対処する保全へと変えました。これにより、生産ラインの停止を最小限に抑え、タイムリーな保守が可能になりました。
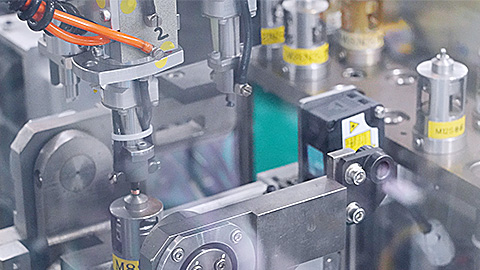
ロボットハンドの
わずかな位置ズレを検知し
設備の停止時間と部品ロスを削減
自動運転中の設備が起こすエラーによる停止(いわゆる“チョコ停”)は、稼働率や品質、安定性を低下させる要因になります。綾部工場では、自働化ラインのロボットハンド先端部のわずかな位置変動を変位センサで計測。特徴量の変化傾向を監視することによって、設備異常の兆候を検知し、未然にメンテナンスしています。これによって、設備エラーによってラインが停止する時間を削減すると共に、部品ロスも削減しました。

小型自走式搬送ロボットによる
搬送で
工程間マテハンを低コストで自働化
マテハンは、低付加価値でありながら自働化が難しい作業の代表例です。綾部工場では、工程間を自律搬送する「小型自走式搬送ロボット」を使った工程間フレキシブル搬送を実現し、マテハンを低コストで自働化しました。必要に応じて、柔軟かつ簡単に搬送ルートを変えられるように設計。個別加工設備のマテハン自働化と、市販のプラスチックレールを活用した低コスト化の追求によって、搬送部の設備コストの50%削減と、設計・製作に要する期間の20%短縮に成功しました。
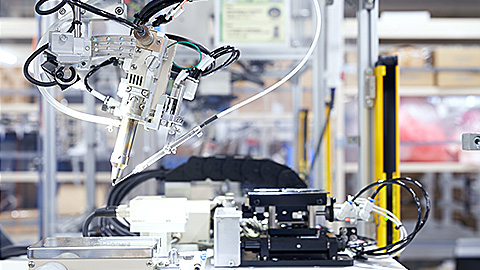
高難度のはんだ付け作業を
ロボット化
熟練者と同等の精度・速度で
スキルレスに
綾部工場では、高度な技能を持つ熟練者だけに許されていた高難度のはんだ付け作業を、ロボットによって自働化しました。熟練者の作業を高速度ビデオによって撮影し、動きを解析してロボットの動作をチューニング。歩留り99.97%以上の高品質で自働化し、さらに60日間を要していた習熟期間をゼロにしました。これによって、熟練者だけが持つ勘やコツなど属人的な暗黙知をシステム化に活用できる形式知に変えて、機械を使った作業による自働化に成功しました。
アクセス
綾部工場
- 住所
- 623-0105 京都府綾部市中山町鳴谷3-2
- アクセス
- JR京都駅よりJR山陰線特急で約70分 綾部駅下車
JR綾部駅よりタクシーにて約20分