草津工場
先進技術と現場力の融合を推し進め
生産性向上とDbl.ppbレベルの
基板実装品質を追求
草津工場では、FAを制御するコントローラ系の製品約4800品種を生産しており、月産20台以下の生産が全体の85%以上という超多品種少量生産となっています。その超多品種少量生産を効率よく進めるためには、柔軟に対応可能な人手作業を効果的に活用する必要があります。草津工場では、生産ライン上から得たデータを継続的に蓄積・分析し、先進生産技術と人が持つ現場力を効果的に融合させる方策を常に探求。さらなる生産性向上と品質革新を目指しています。
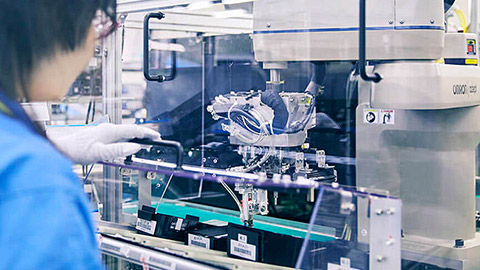
IEによる作業分析で“半自働化”
混流セルラインの生産性を
200%以上に
草津工場では、超多品種少量生産向けの混流セルラインを導入しています。混流セルラインでは、むやみに自働化を推し進めても、投資効果の高い生産性と品質の向上は実現しません。このため、生産現場での工程の稼働状況や作業の様子を科学的に分析・評価し、作業集約や自働化すべき作業を決め、半自働化の混流セルラインを構築。そこで、人と機械の最適な協調を実現し、混流セルラインの生産性が200%以上に向上しました。
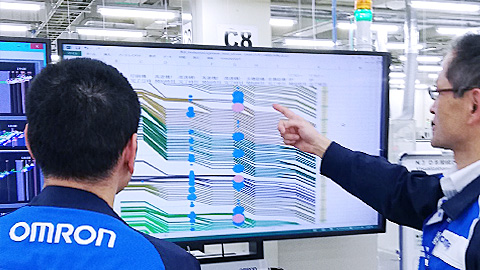
ビッグデータ解析で
ライン全体を見える化
非熟練者でも1/6の時間で
改善点を抽出
超多品種少量生産の生産効率と品質を効果的に高めるには、生産現場全体の稼働状況を俯瞰し、ネックとなる工程を洗い出し、的確な改善を加える必要があります。草津工場では、プリント基板の実装ライン上の全機械から稼働データを収集。これらを集約してビッグデータ解析することで、稼働状況を見える化しています。これまで改善点の抽出作業では、ラインと生産する製品に精通する熟練者の経験に頼っていました。見える化によって、熟練者でなくても、1/6の改善活動時間で生産性を30%向上し、同時に不良率をppbレベルへ低減する取り組みを進めています。
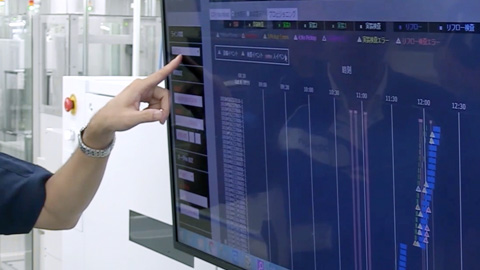
IoT活用による実装プロセスの革新で
工程間での基板1枚1枚の
推移を見える化
プリント基板の実装ラインでは、現場データ活用サービス「i-BELT」を導入。基板が、はんだ印刷、高速実装機、多機能実装機、リフロー炉の間を流れていく際のデータをPLCから収集し、可視化ツールを用いて、基板1枚1枚の時間軸に沿った動きを見える化しています。このデータを解析し、ラインの稼働率を押し下げている要因を調査することによって、改善に向けてラインバランスの調整余地がある部分を的確に見つけることができるようになりました。
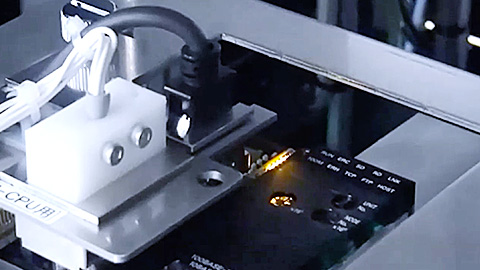
自働化の適用領域を拡大して
超多品種少量生産の
生産性をさらに向上
自働化が困難な超多品種生産を行う混流セルラインですが、自働化が効果的な部分については、積極的な自働化を推し進めています。草津工場では、LED点灯検査、ロータリー・スイッチ検査、バラ部品のピッキングと定位置供給、組立品の外観検査などを自働化しています。さらに、完成品の構内搬送も、モバイルロボットを使って自働化しています。
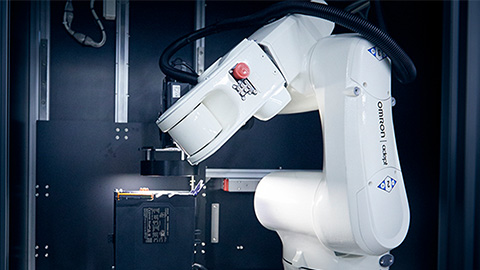
熟練者の感覚に頼る
官能検査を自働化
製品の外観検査は、これまで経験豊富な熟練者が目視で行っていました。こうした官能検査は、手間が掛り、非効率であるだけでなく、検査者のスキルやコンディションによって結果にバラつきが発生しやすい工程でした。草津工場では、検査箇所/項目と良品基準を定量化し細かく画像処理学習させて、熟練者を超える精度で安定した検査を実施できるようにしました。
アクセス
草津工場
- 住所
- 〒525-0035 滋賀県草津市西草津2-2-1
- アクセス
- JR東海道線 草津駅下車 南西へ徒歩約15分